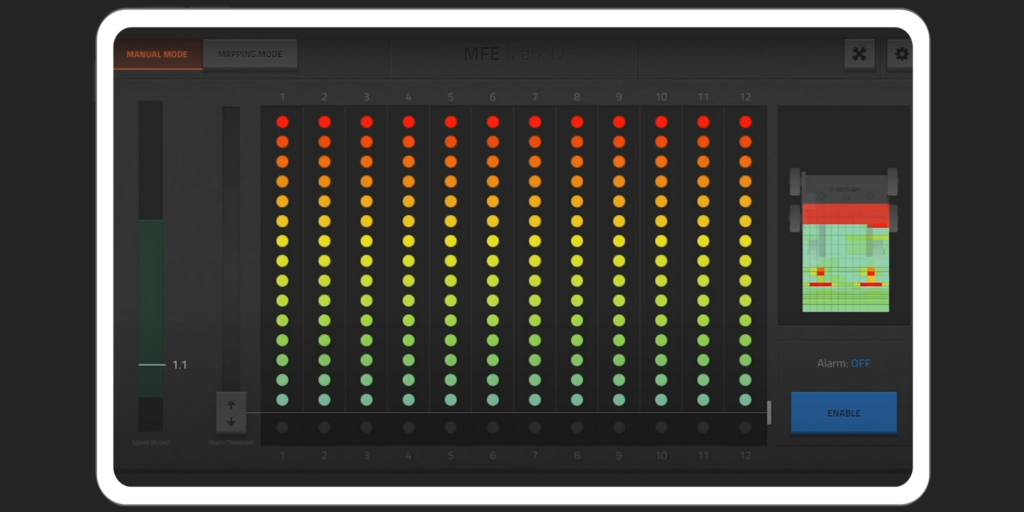
Guide
Magnetic Flux Leakage (MFL): An In-Depth Guide
Magnetic flux leakage testing is an NDT method in which inspectors magnetize a material to identify disruptions in its magnetic field caused by flaws, such as cracks or corrosion.
→ Jump to MFL equipment rentals and sales.
→ Jump to MFL training.
In simple terms, MFL involves magnetizing a steel structure and then measuring the disturbances—or “leakage”—in the magnetic field.
These disturbances occur when the magnetic field encounters a defect, such as a crack or a weakened area. The magnetic flux leakage equipment used for this testing detects these variations and provides data that inspectors can analyze to assess the severity and location of the defect.
Other common terms for magnetic flux leakage testing include:
- MFL testing
- MFL inspection
- Magnetic flux leakage inspection
- Flux leakage testing
- Magnetic leakage field testing
- Magnetic flux testing
- Leakage flux testing
MFL testing is particularly important in heavy industries, where safety is paramount.
Its ability to detect and address flaws before they result in catastrophic failures is why MFL remains a cornerstone of industrial inspection programs, especially in the oil and gas, energy, and manufacturing sectors.
In this guide to magnetic flux leakage we’ll cover what it is, how it works, the top MFL equipment on the market, and a lot more.
Looking for a specific topic? Use the menu on the right to jump around.
Magnetic Flux Leakage (MFL) Equipment for Rent & Sale
Want to buy or rent MFL equipment? Keep reading to see the top options on the market.
1. MFE Mark IV Tank Floor Scanner
The Mark IV Tank Floor Scanner is a robust magnetic flux leakage (MFL) tool specifically designed for inspecting tank floors. Its advanced technology provides highly accurate detection of corrosion, pitting, and material thinning. The Mark IV offers enhanced data acquisition and coverage, making it one of the most effective solutions for large tank inspections in challenging environments.
- High-resolution data collection. Provides detailed reports on corrosion and material loss for maintenance planning.
- Improved maneuverability. The lightweight, ergonomic design ensures easy use in confined spaces.
- Comprehensive inspection coverage. Offers wide-range scanning for complete tank floor assessment.
- Durable build. Built to withstand harsh industrial conditions and provide long-lasting performance.
Buy or rent the Mark IV Tank Floor Scanner.
2. MFE Edge
The MFE Edge is an advanced magnetic flux leakage (MFL) scanner designed for efficient and high-performance tank floor inspections.
With a compact, lightweight design, the MFE Edge provides exceptional maneuverability while delivering accurate and detailed assessments of material loss due to corrosion or thinning. Its user-friendly interface and advanced data collection capabilities make it a go-to tool for inspectors working in challenging environments.
- Lightweight design. Ensures ease of use and improved maneuverability, even in tight or difficult-to-reach spaces.
- High-resolution data collection. Provides precise measurements of corrosion and material loss, essential for effective maintenance planning.
- Advanced software integration. Seamlessly integrates with data collection software for enhanced reporting and analysis capabilities.
- Durable construction. Built to withstand harsh industrial environments, ensuring reliability and longevity in field use.
3. MFE 2412 Mark II
The 2412 Mark II is a reliable and high-performing magnetic flux leakage (MFL) scanner specifically designed for tank floor inspections. With its large 24-inch scanning width and advanced data acquisition system, it provides rapid and precise detection of corrosion, pitting, and material thinning. The Mark II is known for its ease of use and robust construction, making it suitable for use in harsh industrial environments.
- Large 24-inch scan width. Enables quick and efficient inspections of large tank areas.
- Accurate data collection. Delivers precise detection of defects for effective maintenance planning.
- Durable design. Built to withstand rugged field conditions for long-lasting performance.
- User-friendly interface. Simple operation ensures ease of use, even for less experienced operators.
4. MFE HandScan
The MFE HandScan is a portable magnetic flux leakage (MFL) scanner designed for precise, small-scale inspections of ferrous materials. Its compact, lightweight design makes it easy to operate in confined spaces while providing accurate detection of corrosion, pitting, and material loss. Ideal for spot inspections, the HandScan is widely used for testing hard-to-reach areas on tank floors, pipes, and other steel structures.
- Compact design. Enables easy operation in tight or confined spaces.
- Accurate spot inspections. Ideal for detecting localized defects in ferrous materials.
- User-friendly interface. Simple to operate, making it suitable for quick, on-the-go inspections.
- Durable construction. Built for use in harsh industrial environments.
5. MFE Mark III Tank Floor Scanner
The Mark III Tank Floor Scanner is an advanced magnetic flux leakage (MFL) tool designed for fast and accurate tank floor inspections.
With its larger scanning width and high-resolution data collection, the Mark III ensures the early detection of corrosion and material loss. Its robust design and easy maneuverability make it ideal for large-scale tank floor assessments in demanding industrial environments.
- Wide scanning area. Increases inspection efficiency, reducing inspection time for large tanks.
- High-resolution data. Provides detailed corrosion and defect reports for maintenance planning.
- Durable construction. Built to handle harsh industrial conditions.
- User-friendly operation. Simple interface for effective on-site use.
Buy the Mark III Tank Floor Scanner.
MFL Training
We offer comprehensive MFL training that covers all aspects of magnetic flux leakage testing, from understanding the technology to hands-on inspection techniques.
Our training is designed for individuals and companies aiming to enhance their knowledge of MFL testing and improve inspection performance in industries like oil and gas, transportation, and manufacturing.
MFL Training Overview
Our 40-hour MFL Training Class takes place at our headquarters in Dripping Springs, Texas, providing hands-on instruction led by Bryan Duke and the Duke family, experts in MFL for oil, pipeline, and tank inspections.
Classes are limited to 12 students and include classroom sessions, shop demonstrations, and hands-on training on-site. The course follows API 653 Annex G and SNT TC1A standards and includes quizzes, a final exam, and a practical test for certification.
MFL Training Details
- The training is a multi-day course taught by experienced Level II and III MFL inspectors.
- Participants receive hands-on training with MFL equipment, covering proper operation and data interpretation.
- Successful students receive a certification of completion from MFE Inspection Solutions.
Types of MFL Training
- Group training. Join scheduled classes for a collaborative learning experience.
- Personalized training. Companies can arrange private training sessions for their employees (minimum of three participants).
View our upcoming MFL training sessions now.
What Is Magnetic Flux Leakage?
Magnetic Flux Leakage (MFL) technology operates on the principles of magnetism and how magnetic fields interact with ferrous materials.
The process involves creating a strong magnetic field within a material and then using MFL equipment to detect disturbances in that field caused by defects.
Here’s a detailed look at how this MFL technology works:
1. The Physics Behind Magnetic Flux Leakage
MFL is based on the fundamental properties of ferromagnetic materials, such as steel, which become magnetized when exposed to a magnetic field.
When a magnetic field is applied, it flows through the material in a uniform pattern, creating a steady magnetic flux. If the material is free of defects, the magnetic flux remains contained within the material.
2. Creating Magnetic Fields in Ferrous Materials
A magnetic flux leakage detector magnetizes the ferrous material being inspected using a strong magnetic field.
This magnetic field is generated by passing electric current through magnets or coils integrated into the magnetic flux leakage equipment.
As the magnetic field flows through the material, it aligns the domains within the ferromagnetic material, making it fully magnetized.
3. How Leakage Occurs When There’s a Flaw or Defect
When there’s a flaw, such as a crack, corrosion, or thinning in the material, it disrupts the magnetic flux, causing some of the magnetic field to “leak” out of the material.
This magnetic leakage is detected by sensors within the magnetic flux leakage detector, which are typically positioned just above the surface of the material.
The sensors pick up these disturbances and translate them into electrical signals, which can be analyzed to determine the size, location, and nature of the defect.
By using magnetic flux leakage equipment, inspectors can efficiently detect and assess hidden defects that could potentially lead to failure in industrial components like pipelines, storage tanks, and other ferrous structures.
Types of Magnetic Flux Leakage Equipment
In this section, we cover the main types of MFL equipment.
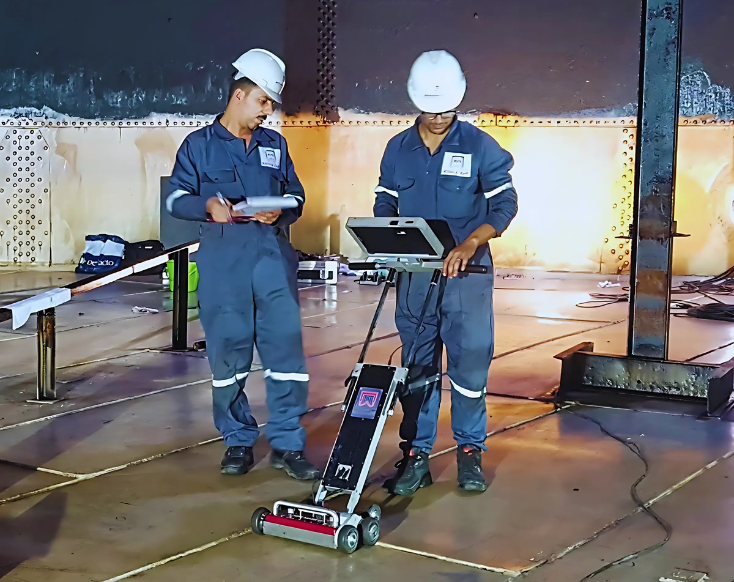
1. Handheld MFL Scanners
Handheld MFL scanners are portable devices designed for small-scale or localized inspections.
These tools are used by operators to manually scan areas like welds, joints, or small sections of ferrous materials. Due to their portability, handheld MFL scanners are particularly effective for spot inspections of storage tanks, pipelines, and structural steel components.
- Key features. Lightweight, easy to transport, and capable of detecting both surface and subsurface defects in ferrous materials.
- Use cases. Ideal for inspecting welds, joints, and small areas of storage tanks or pipelines in oil and gas facilities. These scanners are also commonly used in maintenance inspections where quick spot-checks are required.
2. Inline MFL Tools (Smart Pigs)
Inline magnetic flux leakage tools, often referred to as “smart pigs,” are used for large-scale inspections of pipelines.
These automated tools are inserted into pipelines and travel through them, conducting a comprehensive inspection of the pipeline’s interior. The tool generates a magnetic field and detects any magnetic flux leakage caused by defects in the pipeline wall.
- Key features. Can inspect long distances of pipelines in a single pass, highly automated, and capable of detecting corrosion, cracks, and material loss.
- Use cases. Inline MFL tools are most commonly deployed in the oil and gas industry for pipeline integrity assessments, ensuring that pipelines used for transporting crude oil, natural gas, and other materials are free from defects that could lead to leaks or ruptures.
3. Tank Floor MFL Scanners
Tank floor MFL scanners are specialized pieces of equipment designed to inspect the floors of large storage tanks.
These scanners are critical for detecting corrosion or material thinning at the bottom of tanks, where liquids and chemicals are stored, as this is one of the most vulnerable areas for corrosion due to contact with stored substances.
- Key features. Designed for flat surfaces, can cover large areas of tank floors, and capable of detecting subsurface defects like corrosion or pitting.
- Use cases. Primarily used in refineries, chemical plants, and oil storage facilities to inspect the floors of large storage tanks, ensuring they maintain their structural integrity and preventing leaks or spills.
4. Rail Inspection MFL Devices
Rail inspection MFL devices are used to inspect rail tracks and other critical rail components for flaws that could lead to accidents or service disruptions.
These devices are typically mounted on rail cars or specially designed inspection vehicles that scan the tracks as they move along them. By identifying defects such as cracks, corrosion, or material fatigue in railways, rail inspection MFL devices help ensure the safety and reliability of rail networks.
- Key features. Designed to scan long sections of rail tracks quickly, capable of detecting surface and subsurface defects, and suitable for use in high-speed inspections.
- Use cases. Commonly used by transportation companies to inspect rail tracks and rail-related infrastructure. These devices help prevent derailments and ensure that rail systems remain operational and safe for passengers and cargo.
5. Automated MFL Systems
Automated MFL systems are integrated into manufacturing lines to inspect steel plates, pipes, and other ferrous components as they are produced.
These systems are typically stationary and operate automatically, providing real-time inspection data to ensure that products meet quality standards before they are shipped or used in critical applications.
- Key features. Fully automated, capable of continuous inspection, and integrated into production lines for real-time quality control.
- Use cases. Widely used in the steel manufacturing industry to inspect products such as steel plates, pipes, and other ferrous components. These systems help ensure that products are free from defects and meet the required specifications before they are sent to customers.
Applications of Magnetic Flux Leakage (MFL) Testing
Magnetic flux leakage testing is a critical NDT method used across a range of industries that require accurate and reliable methods to detect flaws in ferrous materials.
MFL’s ability to identify defects such as cracks, corrosion, and material thinning makes it a preferred choice for ensuring the safety and integrity of critical infrastructure.
Here are the top industries that use MFL testing, with key use cases listed for each one.
1. Oil and Gas
The oil and gas industry relies heavily on magnetic flux leakage testing for the inspection of pipelines and storage tanks.
Given the high stakes involved in the transportation and storage of oil and gas, MFL plays a crucial role in identifying defects that could lead to leaks, ruptures, or catastrophic failures. MFL is often used in inline inspection tools, also known as “smart pigs,” to inspect long stretches of pipeline from the inside, ensuring safe operations.
Oil and Gas Use Cases
- Pipeline integrity monitoring. MFL tools are used to inspect thousands of miles of pipeline in real-time to detect corrosion or cracks that may compromise flow and lead to environmental hazards.
- Tank inspection. MFL is applied to the floors and walls of above-ground storage tanks to detect material thinning and prevent hazardous leaks.
- Offshore platform inspection. Offshore oil rigs employ MFL technology to monitor structural integrity in corrosive marine environments where equipment is at greater risk of degradation.
2. Transportation Industry
In the transportation sector, MFL testing is frequently used to inspect rail tracks and axles.
By using a magnetic flux leakage detector, transportation companies can identify and address flaws in steel components, reducing the risk of accidents and improving the safety of trains and other vehicles. This proactive approach to maintenance ensures the longevity of critical transportation infrastructure.
Transportation Use Cases
- Railway track inspection. MFL is used to scan miles of rail lines to detect small cracks or corrosion that could lead to derailments if left untreated.
- Train axle testing. Train axles are regularly inspected using MFL equipment to detect fatigue or stress-related defects that might lead to operational failures.
- Bridges and overpasses. Steel components in bridges and overpasses are inspected with MFL technology to ensure their structural integrity and longevity.
3. Manufacturing Industry
In manufacturing, particularly in industries that produce steel and ferrous components, magnetic flux leakage equipment is used to inspect products such as steel plates, pipes, and other fabricated parts.
MFL testing helps manufacturers ensure that their products meet quality standards and are free from hidden defects that could compromise performance during use.
Manufacturing Use Cases
- Steel plate testing. MFL is used to inspect large steel plates for flaws that might compromise their strength when used in construction or industrial equipment.
- Pipe manufacturing. MFL is employed in the production of steel pipes to detect potential defects that could result in failure during use, particularly in critical applications like oil and gas transport.
- Automotive parts testing. MFL technology is applied to inspect ferrous components in vehicles, such as chassis and axles, ensuring they meet safety standards.
4. Power Generation
Inspectors at power plants, especially those using boilers, heat exchangers, and other high-pressure equipment, employ magnetic flux leakage testing to inspect critical components.
Detecting defects in these components helps avoid costly downtime and ensures that the equipment operates safely under extreme conditions.
Power Generation Use Cases
- Boiler inspections. Inspectors use MFL to test boilers for material thinning or stress cracks that could lead to dangerous failures under high pressure.
- Heat exchanger tubes. MFL testing helps detect defects in heat exchanger tubes, ensuring efficient thermal transfer and preventing unexpected breakdowns.
- Power plant infrastructure. Inspectors test structural steel components in power plants, such as girders and supports, using MFL technology to ensure they remain sound and capable of supporting high loads.
Advantages and Limitations of Magnetic Flux Leakage (MFL) Testing
Magnetic flux leakage testing has several benefits that make it a preferred choice for non-destructive evaluation in various industries.
However, like any technology, it also has its limitations. Understanding both the advantages and constraints of MFL is essential for optimizing its application in industrial inspections.
Advantages of Magnetic Flux Leakage Testing
- Detection of surface and subsurface defects. MFL technology excels at identifying both surface-level flaws, such as cracks and corrosion, and subsurface defects that are not visible to the naked eye. This comprehensive detection capability ensures a thorough assessment of the integrity of ferrous materials.
- High-speed inspection. Magnetic flux leakage inline inspection allows for rapid scanning of long sections of pipelines and other structures without the need for shutdowns or interruptions in service. This efficiency reduces downtime and increases productivity.
- Cost-effective. Compared to other non-destructive testing methods, MFL testing is relatively affordable. The equipment is durable and can be used repeatedly for various inspections, lowering the overall cost of maintenance and safety assurance.
- Versatility. MFL equipment can be adapted to inspect a wide range of ferrous materials and structures, including pipelines, storage tanks, rail tracks, and automotive components. This versatility makes it suitable for multiple applications across different industries.
- Real-time data collection. MFL systems provide immediate feedback during inspections, allowing for the prompt identification and documentation of defects. This real-time data is crucial for making timely maintenance decisions and preventing potential failures.
Limitations of Magnetic Flux Leakage Testing
- Difficulty in detecting smaller cracks. While MFL is effective at identifying a range of defects, it can struggle to detect very small or fine cracks. These minor flaws may go unnoticed, potentially allowing them to develop into more significant issues over time.
- Material dependence. MFL testing is primarily effective on ferrous materials. Non-ferrous materials, such as aluminum or copper, do not respond to magnetic flux leakage in the same way, limiting the applicability of MFL in certain contexts.
- Surface condition sensitivity. The accuracy of MFL testing can be affected by the surface condition of the material being inspected. Surface roughness, coatings, or debris can interfere with the magnetic field and the detection of leakage, potentially leading to false readings or missed defects.
- Equipment calibration and maintenance. To ensure accurate results, magnetic flux leakage equipment requires regular calibration and maintenance. Failure to properly maintain the equipment can result in unreliable data and compromised inspection outcomes.
- Operator expertise. Effective MFL testing relies on the skill and experience of the operator. Proper training is essential to interpret the data correctly and to identify defects accurately. Inexperienced operators may misinterpret results, leading to incorrect assessments of material integrity.
Despite its limitations, the advantages of magnetic flux leakage equipment make it an invaluable tool for magnetic flux leakage inline inspection in industries where safety and integrity are paramount.
Frequently Asked Questions About Magnetic Flux Leakage (MFL) Testing
What is magnetic flux leakage testing?
Magnetic flux leakage testing is a non-destructive testing (NDT) method used to identify surface and subsurface defects in ferrous materials. It works by magnetizing the material and detecting disruptions, or “leakage,” in the magnetic field caused by defects like cracks, corrosion, or material thinning. This method is commonly used in the inspection of pipelines, storage tanks, and other steel structures to ensure their structural integrity.
What does MFL stand for?
MFL stands for Magnetic Flux Leakage. It refers to the principle by which a magnetized material “leaks” its magnetic field when there is a defect present, such as a crack or corrosion. The leakage is detected by specialized equipment, allowing inspectors to identify and assess flaws in ferrous materials.
MFL may also stand for:
- Modern Foreign Languages. Refers to languages that are currently spoken and taught, such as Spanish or German15.
- Maximum Foreseeable Loss. A term used in insurance, particularly related to property insurance, indicating the largest loss that could occur under a given set of circumstances12.
- Madden Football League. A gaming league based on the popular Madden NFL video game series13.
- Market Frankford Line. A subway line in Philadelphia, often referred to by its abbreviation MFL4.
How accurate is MFL testing?
MFL testing is known for its reliability in detecting medium to large defects, including both surface and subsurface flaws. However, the accuracy of magnetic flux leakage equipment can vary based on factors such as the size of the defect, surface condition, and calibration of the equipment. While MFL is excellent for detecting larger flaws, very small cracks may sometimes go undetected, making it important to supplement MFL with other testing methods if high precision is required.
What industries use magnetic flux leakage detectors?
Magnetic flux leakage detectors are widely used across various industries, particularly in those where the integrity of steel structures is critical. Key industries include:
- Oil and Gas. Used for pipeline and storage tank inspections to detect corrosion and prevent leaks.
- Transportation. Applied in rail track inspections and to assess the condition of train axles and other critical components.
- Manufacturing. Utilized for inspecting steel plates, pipes, and other ferrous components during the production process to ensure quality.
- Power Generation. Inspections of boilers, heat exchangers, and other high-pressure equipment rely on MFL to ensure operational safety.
What are the types of magnetic flux leakage testing?
There are two main types of magnetic flux leakage testing:
- Handheld MFL testing. Typically used for small-scale inspections, such as localized tank inspections or structural steel assessments, where the operator manually moves the magnetic flux leakage detector across the surface.
- Inline MFL inspection. Used for large-scale inspections, such as pipelines, where automated tools, known as “smart pigs,” move through the pipeline conducting magnetic flux leakage inline inspections to detect flaws over long distances.
What materials can be inspected using MFL testing?
Magnetic flux leakage testing is specifically designed for ferrous materials, such as steel and iron. Non-ferrous materials, like aluminum and copper, do not respond to magnetic flux and therefore cannot be inspected using MFL. MFL is widely used for inspecting pipelines, storage tanks, and structural steel components made from ferrous materials.
How long does an MFL inspection take?
The duration of an MFL inspection depends on the size and complexity of the structure being inspected. Handheld MFL scanners can inspect small areas in minutes, while inline MFL tools used for pipeline inspections may take several hours to cover long distances. The time also depends on the condition of the material and the type of defects present.
What is the difference between MFL and ultrasonic testing?
Magnetic flux leakage testing and ultrasonic testing are both non-destructive methods used to detect defects in materials. MFL is used specifically for ferrous materials and detects both surface and subsurface defects by measuring magnetic field disruptions. Ultrasonic testing, on the other hand, uses high-frequency sound waves to detect flaws in a wide range of materials, including non-ferrous metals, and can detect smaller cracks that MFL might miss.
Can MFL testing be performed on coated surfaces?
Yes, MFL testing can be performed on coated surfaces. However, the coating must not be too thick, as it can interfere with the magnetic field and reduce the accuracy of the detection. Thin coatings are generally acceptable, but thicker coatings may require special adjustments or supplementary testing methods.
What’s the difference between Magnetic Flux Leakage and Eddy Current NDT testing?
While both Magnetic Flux Leakage (MFL) and Eddy Current testing are non-destructive testing methods, they differ in their application and materials. MFL is specifically used for ferrous materials and detects flaws by measuring disturbances in the magnetic field. Eddy Current testing uses electromagnetic induction to detect defects in both ferrous and non-ferrous materials, and it is especially effective for detecting surface and near-surface flaws. Eddy current is often preferred for thinner materials and non-ferrous metals.