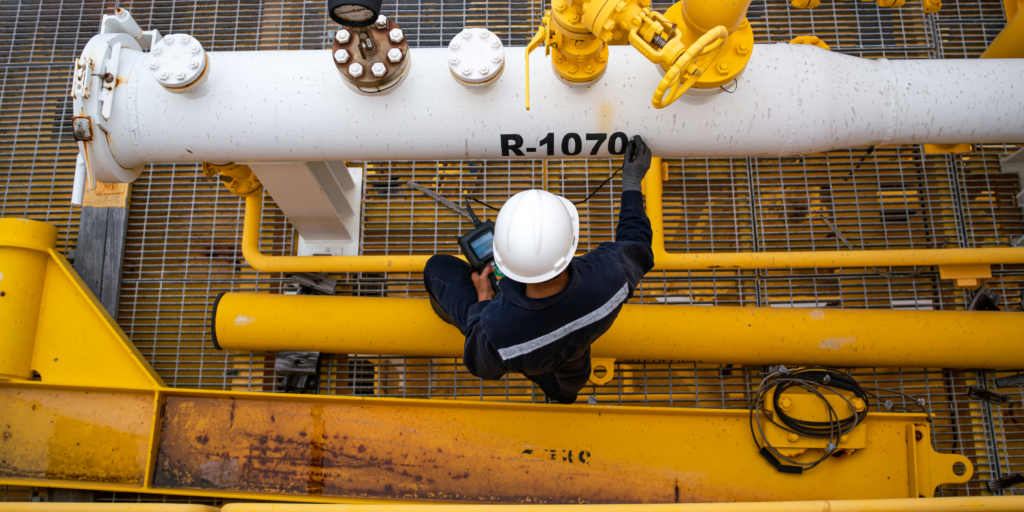
Guide
NDT: The Complete Guide to Non-Destructive Testing [Updated for 2025]
Non-Destructive Testing (NDT) is an inspection term that refers to inspecting a material or object without harming it.
In contrast, Destructive Testing (DT) is an inspection term for testing a material or object in a way that will harm or even destroy it. By preserving the subject’s original state, NDT provides a cost-effective, reliable means of monitoring and maintaining systems, ensuring long-term operational efficiency and safety.
In inspection terminology, the words testing and inspecting mean basically the same thing: deriving information about the condition of a material or asset that will help inform maintenance decisions to prolong the life of the material or asset.
NDT (Non-Destructive Testing) is also commonly called:
- NDE (non-destructive examination)
- NDE (non-destructive evaluation)
- NDI (non-destructive inspection)
Note: This guide is quite long. We suggest using the menu to the right to jump to the areas that most interest you.
What Is NDT?
Inspectors use NDT testing to collect information about a material in ways that do not alter it—that is, ways that don’t destroy it, unlike Destructive Testing (DT).
All of the most common inspection techniques are non-destructive—for example, visual inspections, in which an inspector uses the naked eye to evaluate the condition of an asset.
But NDT isn’t used just by inspectors.
NDT applications span industrial inspections in heavy industries like power generation and oil and gas, where it serves an important function in preventive maintenance.
Inspectors may do NDT that doesn’t require special equipment, such as visually assessing the condition of a pipeline, or they may use advanced tools like ultrasonic sensors to detect hidden flaws.
NDT can also be used to describe work in medicine and healthcare: Procedures like ultrasounds and MRIs are forms of NDT, since they provide internal insights without the need for invasive actions.
Whether an inspector is doing basic visual NDT that doesn’t require any equipment or is using sophisticated NDT technology, the objective remains the same: to gather high-quality data about the condition of an asset without damaging it.
A Short History of NDT
Non-Destructive Testing (NDT) has a rich history that dates back over a century, evolving significantly in both technique and application. Here’s a brief look at its development and key milestones:
- Early 1900s. The foundational concept of NDT began with the development of X-ray technology by Wilhelm Conrad Roentgen in 1895. By the early 1900s, industrial radiography took off with the use of X-rays to examine castings and welds in factories.
- 1920s. The oil and gas industry began using ultrasonic testing to inspect pipelines, marking one of the first major industrial applications of NDT.
- 1940s. Magnetic particle and dye penetrant techniques were developed, providing simpler methods for surface inspection. This era also saw the increased use of ultrasonic and radiographic testing during World War II to ensure the integrity of weapons and armored vehicles.
- 1950s-1960s. The term “Non-Destructive Testing” started to gain traction, and the field saw significant technological advances. During this time, professional societies such as the American Society for Nondestructive Testing (ASNT) were established, promoting standards and training.
- 1970s. Advancements in electronic technology further refined NDT methods. Eddy current testing became more sophisticated with digital processing, enhancing its capabilities in flaw detection.
- 1980s onwards. The introduction of digital technology revolutionized NDT. Techniques such as digital radiography and phased array ultrasonics emerged, allowing for more precise and detailed inspections.
- 2000s to today. Modern NDT now integrates advanced computational methods and robotics, pushing the capabilities of traditional testing methods. There are comprehensive international standards governing NDT processes across various industries, ensuring safety, efficiency, and quality. Standards such as those from the American Petroleum Institute (API) and International Organization for Standardization (ISO) provide guidelines that are critical in industries including aerospace, manufacturing, and energy.
This progression illustrates how NDT has evolved from simple visual inspections and basic tools to a sophisticated discipline crucial to modern manufacturing and safety protocols.
The continuous refinement of techniques and standards highlights NDT’s essential role in industrial innovation and safety management.
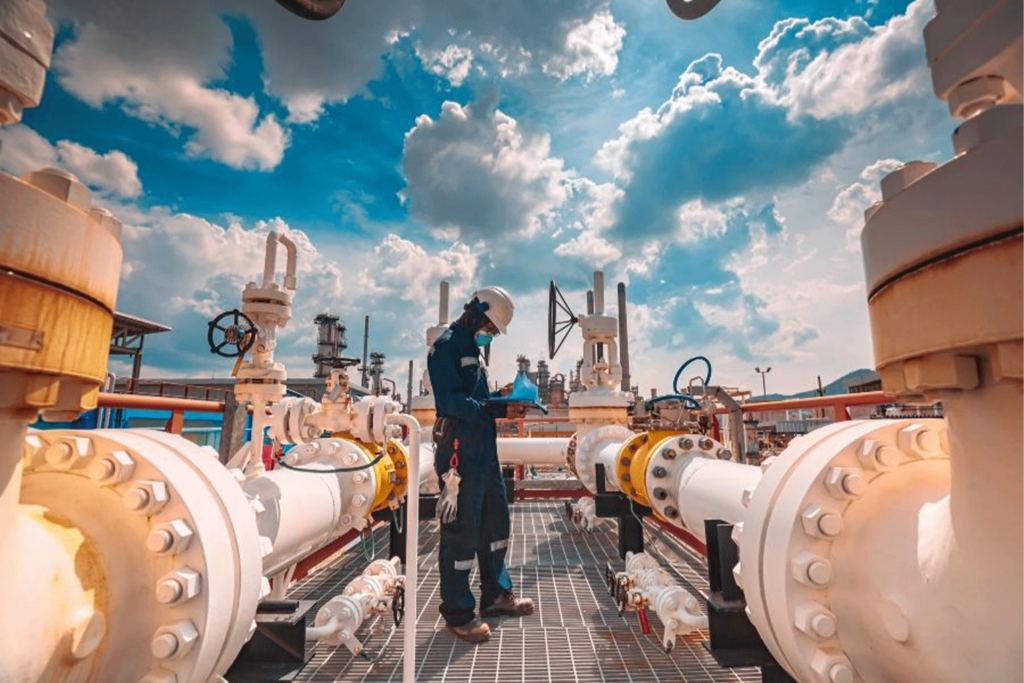
The Top Five Benefits of Non-Destructive Testing
Non-destructive testing is an important part of maintaining operational efficiency, safety, and reliability in various industrial sectors, and it’s a key component in quality control processes.
Having an NDT protocol:
1. Ensures Safety
One of the primary objectives of NDT is to ensure the safety of products, transportation systems, and infrastructure used around the world. It plays a critical role in inspecting and certifying the safety of items we use daily, and it’s crucial for detecting flaws that could lead to severe accidents if left unchecked.
2. Saves Money Over Time
NDT is also significant due to its cost-efficiency. By identifying defects or irregularities early in the production cycle or operational life of equipment, it helps in avoiding the substantial costs associated with catastrophic failures or extensive repairs. The early detection of defects enables industries to address issues promptly, thereby reducing downtime and associated costs.
3. Helps Reduce Unplanned Outages and Downtimes
In industries like nuclear power, NDT helps in identifying defects such as weld discontinuities and structural anomalies within materials. The detection of such defects is crucial to prevent unplanned outages and ensure the continuous and reliable operation of facilities, significantly impacting industrial productivity and operational success.
4. Preserves Structural Integrity
NDT’s non-invasive nature is essential in preserving the structural integrity of the materials tested. Since the methods used in NDT do not damage or alter the material, component, or assembly being tested, they remain in their operational condition after the test, which is crucial for maintaining the longevity and performance of the materials and components.
5. Supports Quality Control
NDT provides the highest level of quality control throughout all stages of assembling any equipment or structure. It is instrumental in ensuring that the products meet the requisite standards and specifications, thereby guaranteeing customer satisfaction and adherence to regulatory compliance. It is a practical and flexible technique that can find issues or flaws in materials without compromising their quality.
Non-destructive testing is indispensable in contemporary industrial practices, addressing safety, reliability, and quality control needs across various sectors.
Its ability to detect flaws early, without causing damage to the subjects, makes it a crucial tool in the prevention of industrial accidents, maintenance of structural integrity, and assurance of product quality, underlining its comprehensive importance in industrial operations.
NDT Techniques: The Top 11 Types of NDT Methods
When inspectors use the term NDT, they’re referring to a group of analysis methods used to evaluate the properties of materials, components, or systems without causing them damage.
These NDT techniques are essential ways for inspectors to collect the data they need in order to make key determinations about the integrity of the assets they’re tasked with inspecting.
NDT methods can vary widely, each suited to different types of materials and detection needs. But they all have the same goal: to help inspectors discover potential issues before they lead to serious failures.
Here are the 11 most common NDT techniques, listed in alphabetical order.
- Visual NDT (VT)
- Thermographic Testing (TT)
- Ultrasonic NDT (UT)
- Acoustic Emission NDT (AE)
- Eddy Current NDT (ET)
- Ground Penetrating Radar (GPR)
- Dye Penetrant NDT (PT)
- Leak Testing (LT)
- Magnetic Particle NDT (MT)
- Radiography NDT (RT)
- Shearography NDT
1. Visual NDT (VT)
Visual Testing (VT), one of the most fundamental forms of Non-Destructive Testing (NDT), involves the inspection of materials, components, and assemblies to identify visible surface defects such as corrosion, misalignments, physical damage, and inconsistencies in workmanship.
This method relies on the direct observation by inspectors, often assisted by tools such as magnifying glasses, mirrors, borescopes, or video equipment to enhance visibility in hard-to-reach areas.
How to Do Visual Non Destructive Evaluation
- Preparation. Clean the object to remove any dirt, grease, or coatings that might obscure surface imperfections. Good lighting is crucial for effective visual inspection.
- Equipment selection. Depending on the inspection requirements, choose appropriate visual aids such as magnifiers, flashlights, or video inspection tools.
- Inspection procedure. Systematically examine the surface of the material. For large or complex surfaces, follow a methodical pattern to ensure no areas are missed.
- Defect identification. Look for any irregularities on the surface that might indicate defects. Use markers or tags to note the locations of flaws for further analysis or repair.
- Reporting. Document the findings with descriptions, measurements, photographs, or video captures. Provide a detailed report that can be used for quality control and maintenance records.
Applications for Visual Non-Destructive Examination
- Power generation. For routine maintenance checks on equipment to prevent failures.
- Construction. For assessing the condition of structures and components like beams, pipes, and welds.
- Manufacturing. To check for surface defects in raw materials and finished products.
- Automotive. Inspecting components during assembly for cracks, scratches, or improper fittings.
Learn more about visual inspections in this in-depth guide.
2. Thermographic Testing (TT)
Thermographic Testing (TT), also known as Infrared Testing, is a non-destructive testing technique that utilizes infrared imaging and thermal cameras to detect variations in thermal energy emitted from an object. This method identifies defects in materials by capturing and analyzing the heat signatures that differ from the normal areas due to variations in thermal conductivity caused by flaws such as cracks, voids, or delaminations.
How to Do Thermographic Non Destructive Evaluation
- Setup. Prepare the infrared camera and adjust it to the specific settings required for the material and the type of inspection.
- Thermal equilibration. Allow the test object to reach a thermal equilibrium if necessary, or apply a controlled heat source to enhance thermal contrast.
- Image capturing. Scan the object with the infrared camera systematically to cover the entire area. Capture thermal images that will show different heat patterns.
- Data analysis. Use specialized software to analyze the thermal images. Look for abnormal patterns that indicate potential defects.
- Reporting. Generate a detailed report with thermal images and analysis to provide conclusions and recommendations based on the findings.
Applications for Thermographic Non-Destructive Examination
- Building inspections. Detecting heat leaks, moisture intrusion, and electrical faults in buildings.
- Electrical systems. Identifying overheated components or poor connections in electrical installations.
- Mechanical systems. Monitoring bearings, motors, and other mechanical equipment for overheating issues.
Learn more about thermographic inspections in this in-depth guide.
3. Ultrasonic NDT (UT)
Ultrasonic Non-Destructive Testing (UT) is a method used to detect internal flaws, measure thickness, and evaluate material properties through the use of high-frequency sound waves. The technique involves sending ultrasonic wave pulses into a material and then analyzing the waves that are reflected back or transmitted through the material to identify anomalies.
How to Do Ultrasonic Non Destructive Evaluation
- Equipment setup. Prepare the ultrasonic testing device and select the appropriate transducer based on the material properties and the type of inspection required.
- Couplant application. Apply a gel or liquid couplant to the surface of the test object to facilitate the efficient transmission of ultrasonic waves.
- Scanning. Move the transducer over the surface of the material. The device sends sound waves into the material, which reflect back upon encountering flaws or interfaces.
- Signal interpretation. Analyze the signals captured by the transducer. Flaws are indicated by the presence of reflected wave signals before they are expected, or by the absence of expected reflections.
- Documentation. Record the findings and map the location and size of any defects for further evaluation and decision-making.
Applications for Ultrasonic Non-Destructive Examination
- Oil and Gas. Inspecting pipelines and pressure vessels for corrosion and cracks.
- Aerospace. Checking aircraft fuselage and engine components for defects.
- Manufacturing. Quality control of metals and welded joints.
- Automotive. Evaluating critical components like engine blocks and axles for internal defects.
Learn more about ultrasonic testing in this in-depth guide.
4. Acoustic Emission NDT (AE)
Acoustic Emission (AE) Non-Destructive Testing is a method used to monitor changes in the internal structure of materials by detecting transient elastic waves, which are generated when a material undergoes deformation due to mechanical stress.
How to Do AE Non Destructive Evaluation
- To conduct AE testing, sensors are strategically placed on the surface of the structure or material being inspected.
- These sensors capture the high-frequency waves produced by the release of energy from sources such as cracks forming or growing.
- The data collected is then analyzed to determine the location and severity of any potential issues.
- Testing is often performed under load to ensure that active faults are detected.
Applications for AE Non-Destructive Examination
- Pressure vessels and storage tanks. For detecting corrosion and cracks.
- Bridges and civil structures. For monitoring structural integrity.
- Aerospace components. For fatigue crack detection.
Learn more about acoustic emission testing in this in-depth guide.
5. Eddy Current NDT (ET)
Eddy Current Testing (ET) is a non-destructive testing method that utilizes electromagnetic induction to detect flaws in conductive materials. It involves generating a circular electric current (eddy current) within the material using a coil carrying an alternating current. The interaction of the eddy currents with the material helps identify discontinuities based on changes in the current’s flow pattern.
How to Do Eddy Current Non Destructive Evaluation
The process of conducting Eddy Current Testing typically includes the following steps:
- Equipment Setup: Configure the eddy current instrument and select the appropriate probe based on the material and type of inspection.
- Calibration: Calibrate the instrument using standards that are similar in conductivity and geometry to the test specimen.
- Scanning: Move the probe along the surface of the material. The probe sends alternating current through the material, creating eddy currents.
- Data Analysis: Monitor the readings on the eddy current instrument; fluctuations in the eddy current’s impedance indicate flaws.
- Interpretation: Analyze the data collected to determine the location, size, and possible type of flaw.
Applications for Eddy Current Non-Destructive Examination
- Aerospace. For the inspection of aircraft fuselage and engine components.
- Manufacturing. To check the integrity of metal tubes and bars in production lines.
- Automotive. For detecting cracks or corrosion in engine parts and automotive structures.
Learn more about eddy current testing in this in-depth guide.
6. Ground Penetrating Radar (GPR)
Ground Penetrating Radar (GPR) is a non-destructive testing method that uses radar pulses to image the subsurface. This technology involves emitting high-frequency radio waves into the ground and recording the echoes that return from subsurface structures to create images or profiles of subsurface features. GPR can detect objects, changes in material, voids, and cracks.
How to Conduct GPR Non Destructive Evaluation
- Setup equipment. Assemble the GPR system which typically includes a control unit, antenna, and data recording unit.
- Survey planning. Map out the area to be surveyed and define the grid for the scans to ensure comprehensive coverage.
- Data collection. Push or tow the GPR equipment over the target area. The radar waves penetrate the ground and reflect signals back to the antenna.
- Data interpretation. Use software to analyze the radar data and construct an image of the subsurface. Different materials and structures will reflect waves differently, creating a profile of the area below.
- Reporting. Generate reports based on the radar data with interpretations of subsurface anomalies and recommendations for further action if needed.
Applications for GPR Non-Destructive Examination
- Civil engineering. To locate rebar in concrete, measure thickness, and detect voids beneath surfaces.
- Utility location. For finding and mapping underground utilities such as pipes and cables.
- Environmental studies. For mapping soil layers, finding underground storage tanks, and identifying contaminated sites.
- Archaeology. To detect and map archaeological features without excavation.
Learn more about ground penetrating radar NDT in this in-depth guide.
7. Dye Penetrant NDT (PT)
Dye Penetrant Inspection (DPI), also known as Liquid Penetrant Inspection (LPI) or Penetrant Testing (PT), is a widely used Non-Destructive Testing (NDT) method that helps to detect surface-breaking defects in non-porous materials. This method involves applying a liquid dye to the surface of the material, which penetrates into any flaws and is then drawn out to reveal defects through visible inspection.
How to Do Dye Penetrant Testing Non Destructive Evaluation
Here are the key steps for penetrant testing:
- Pre-cleaning. The surface of the material is cleaned to remove any dirt, oil, or other contaminants that might prevent dye penetration.
- Application of penetrant. A visible or fluorescent dye is applied over the surface.
- Dwell time. The penetrant is left to soak into any surface breaks for a specific period.
- Excess penetrant removal. The excess penetrant is carefully cleaned off the surface.
- Developer application. A developer is applied, which helps draw out the penetrant from the defects to create a visible indication.
- Do the inspection. The final step is the visual inspection under appropriate lighting conditions to identify any indications that represent defects.
Applications for Dye Penetrant Non-Destructive Examination
- Aerospace. For inspections of critical components such as turbine blades and fuselage structures.
- Automotive. In checking casting, forgings, and welds on vehicle components.
- Metal fabrication. To ensure the integrity of structural components.
Learn more about dye penetrant testing in this in-depth guide.
8. Leak Testing (LT)
Leak Testing (LT), also known as Leak Detection, is a non-destructive testing method used to check systems and containers for leaks and to ensure their integrity and tightness. This method involves the application of pressure or vacuum to a system and monitoring it for changes, which can indicate the presence of a leak. Various techniques such as bubble testing, pressure decay, and helium sniffing are employed based on the required sensitivity and the nature of the system being tested.
How to Conduct Leak Testing Non Destructive Evaluation
- Preparation. Ensure the test object is clean and dry. Any contaminants or moisture can affect the results.
- Sealing. Close off all ports and connections of the test piece except where the test medium (air, water, helium) will be introduced.
- Testing. Introduce the test medium into the system. For vacuum tests, evacuate the air inside the test object.
- Monitoring. Observe for a predetermined time for signs of the test medium escaping, using methods appropriate to the medium (e.g., soap solution for bubble tests, electronic detectors for gas tests).
- Data analysis. Measure and record the rate of pressure change or detect the presence of test medium outside the test object, which would indicate a leak.
Applications for Leak Testing Non-Destructive Examination
- Pharmaceutical. Ensuring the integrity of packaging to maintain sterility.
- Automotive. Testing fuel systems, radiators, and air conditioning units for leaks.
- Aerospace. Checking the tightness of hydraulic systems and fuel tanks.
- Manufacturing. Verifying the leak-tightness of valves, tanks, and vessels.
Learn more about leak testing in this in-depth guide.
9. Magnetic Particle NDT (MT)
Magnetic Particle Testing (MT), also known as Magnetic Particle Inspection, is a non-destructive testing technique used to detect surface and slightly subsurface discontinuities in ferromagnetic materials. This method utilizes a magnetic field and ferrous particles suspended in a liquid or dry form to reveal defects. The magnetic field causes the particles to gather at any surface flaws, creating a visible indication under proper lighting conditions, especially when using fluorescent particles.
How to Do Magnetic Particle Non Destructive Evaluation
- Surface preparation. Clean the test surface to remove any dirt, grease, or paint that might inhibit particle movement.
- Magnetization. Apply a magnetic field to the test material using direct or indirect magnetization techniques. The method chosen depends on the material’s geometry and the type of defect sought.
- Application of particles. Sprinkle or spray magnetic particles over the area being tested while the part is magnetized.
- Inspection. Observe the test surface under appropriate lighting. Any discontinuities will attract the particles, forming visible indications.
- Demagnetization. If necessary, demagnetize the component to remove any residual magnetic field, which could affect its future use or further testing.
Applications for Magentic Particle Non-Destructive Examination
- Oil and Gas. Inspecting pipelines and drilling equipment for stress corrosion cracks.
- Aerospace. Checking aircraft components for cracks due to fatigue.
- Automotive. Testing critical safety components like axles, rods, and gears.
- Manufacturing. Quality control of castings, forgings, and welds during production.
Learn more about magnetic particle inspection in this in-depth guide.
10. Industrial Radiography NDT
Radiography Testing (RT), or radiographic inspection, is a non-destructive testing technique that uses X-rays or gamma rays to view the internal structure of a component. By exposing a part to radiation and capturing the image on a detector or film, differences in material density and variations in thickness are highlighted, revealing defects such as cracks, voids, or inclusions.
How to Do Radiography Non Destructive Evaluation
- Preparation. Isolate the component and ensure that it is free from any external materials that could interfere with the imaging process.
- Safety measures. Set up appropriate safety barriers and warning signs to protect operators and nearby personnel from radiation exposure.
- Exposure. Position the radiation source on one side of the object and the film or detector on the opposite side. The radiation passing through the object creates an image that reflects its internal structure.
- Development and analysis. Develop the film in a darkroom setting (for traditional film) or process the digital image. Analyze the image for any irregularities that indicate defects.
- Reporting. Document the findings and provide recommendations based on the analysis.
Applications for Radiography Non-Destructive Examination
- Oil and Gas. Examining pipelines and pressure vessels for corrosion and weld quality.
- Construction. Assessing structural integrity in steel and reinforced concrete.
- Aerospace. Inspecting components for cracks and material integrity to ensure flight safety.
- Automotive. Checking welds and castings in critical vehicle parts.
Learn more about industrial radiography in this in-depth guide.
11. Shearography NDT
Shearography, a non-destructive testing (NDT) method, is used primarily to detect defects in composite materials, laminates, and bonded structures. This technique utilizes the optical measurement of surface deformations caused by stress differences when an object is subjected to mechanical, thermal, or vacuum stress. Shearography provides a quick and effective means of examining large areas to identify subsurface anomalies like delaminations, voids, and other defects.
How to Do Shearography Non Destructive Evaluation
- Setup and calibration. Position the shearography camera system to focus on the target area. Calibrate the device according to the specific test requirements.
- Application of stress. Apply stress to the material through mechanical load, heat, or vacuum, depending on the nature of the test object and the expected types of defects.
- Capturing images. Capture the initial and stressed states of the object’s surface using the shearography equipment. The camera records changes in the interference pattern of the laser light reflected from the surface.
- Data analysis. Analyze the captured images to detect any distortion patterns that indicate defects.
- Documentation. Document the findings with photographic evidence and detailed reports on the detected anomalies.
Applications for Shearography Non-Destructive Examination
- Aerospace. Inspecting aircraft composites and honeycomb structures for integrity and damage.
- Automotive. Examining car tires and composite body parts for hidden defects.
- Manufacturing. Quality control of composite materials used in various industrial applications.
- Marine. Checking the integrity of fiberglass and composite boat hulls.
Emerging NDT Techniques
Advancements in the sphere of non-destructive testing technology are at the forefront of modern industrial progression, amalgamating innovation with precision to elevate the efficacy of inspection processes.
Here are some of the top emerging NDT techniques:
- Total Focusing Method (TFM)
- Laser Shearography
- Infrared Thermography
- Terahertz NDE
These techniques are bolstering the capacities of NDT, rendering it more proficient in deciphering material inconsistencies and abnormalities.
The trajectory in NDT is also characterized by an increasing prominence of ultrasonic testing, projected to lead the way in future trends. The ever-evolving market dynamics necessitate a continuous refinement in ultrasonic testing methodologies, ensuring that they remain attuned to the emerging complexities and the escalating demand for more sophisticated inspection techniques.
Including wireless connectivity with test probes and sensors is another milestone in NDT’s evolution. This revolutionary modification has paved the way for real-time data processing and enhanced data interpretation capabilities, rendering the sector more agile and responsive.
Advancements in NDT technology are instrumental in steering the professional inspection landscape towards unprecedented horizons.
The convergence of emerging technologies, integrated solutions, and innovative methodologies is fortifying the foundation of non-destructive testing, ensuring its sustained relevance and adaptability in the face of the ever-evolving industrial ecosystem.
Non-Destructive Testing Equipment and Technology
In the world of NDT, an array of sophisticated equipment and technologies plays a pivotal role in conducting precise and efficient evaluations.
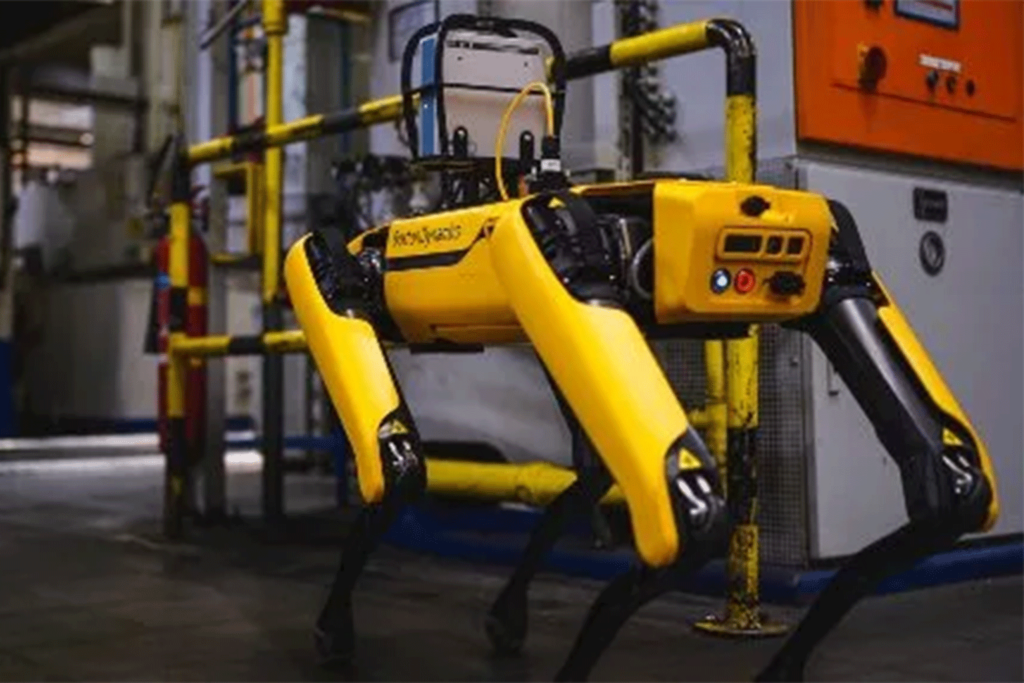
Essential Equipment in Non-Destructive Testing
The essential equipment in NDT varies across techniques.
For example, ultrasonic testing employs transducers and flaw detectors to detect discontinuities within materials, while radiographic testing uses X-ray and gamma-ray equipment to examine the internal structures of the test subject.
Additionally, Magnetic Particle Testing necessitates the use of magnetic yokes and Liquid Penetrant Testing requires penetrant and developer to detect surface-breaking defects.
The precision and reliability of results are directly influenced by the choice of this essential equipment, enforcing a meticulous selection process tailored to the specific needs and nature of the inspection.
[Related Read: The Best NDT Equipment for Sale 2023]
Automated vs. Manual NDT Methods
The juxtaposition of automated and manual NDT methods showcases a profound contrast in execution and outcome.
Automated NDT offers repeatability, consistency, and high-speed inspections, optimizing the process for large-scale evaluations. It mitigates human error and fatigue, providing an unswerving approach to inspections.
Conversely, manual methods bring forth the invaluable aspect of human intuition and judgment, essential in scenarios where complex decision-making and adaptability are paramount. The synergy of automated and manual methods allows for a comprehensive inspection strategy, balancing the rigor and nuances of non-destructive testing effectively.
The Role of Robotics in NDT
Robotics has ushered in a new era in NDT, encapsulating the benefits of automation and enhancing them with increased reachability and adaptability.
Robots, with their ability to access confined and hazardous spaces, have broadened the scope of inspections, ensuring safety and efficacy. The integration of robotic systems with advanced NDT technologies facilitates meticulous inspections in environments previously deemed inaccessible or hazardous.
This amalgamation not only changes the capabilities of NDT professionals but also safeguards them against potential risks inherent to intricate inspection environments.
The integration and continuous evolution of equipment, technologies, and methodologies in NDT are instrumental in advancing the field.
The interplay between essential equipment, technological advancements, automation, manual methods, and robotics is shaping the future of non-destructive testing, fortifying its role in material and structural assessments.
The commitment to innovation and adaptability within the NDT community is propelling the discipline forward, ensuring it remains at the forefront of inspection and evaluation endeavors.
Standards and Certifications in Non-Destructive Testing
Adhering to recognized standards and obtaining relevant certifications are crucial steps in ensuring the reliability and effectiveness of testing methods. Standards function as comprehensive guides depicting suitable techniques and methods to detect and evaluate flaws in materials and objects without causing any damage.
Certifications, on the other hand, validate the competence of professionals performing the tests, thereby maintaining the integrity of the NDT process.
The American Society for Nondestructive Testing (ASNT) is a prominent organization contributing substantially to the development of standards and certifications in the NDT domain. The ASNT Standards and Practices encompass a broad array of norms and guidelines at both international and national levels, shaping the qualification and certification criteria for personnel engaged in NDT.
One notable standard is the ANSI/ASNT CP-106, which is a modified adoption of ISO 9712. This standard, slated for an update in 2023, specifically governs the qualification and certification of NDT personnel, outlining the requisite knowledge, skills, and abilities for various levels of certification.
Moreover, the ASTM International also offers a compilation of nondestructive testing standards. These standards provide intricate guides, detailing the appropriate methods and techniques for detecting and evaluating flaws in different materials and objects.
The industry acknowledges three principal levels of NDT certification:
- NDT Level 1
- NDT Level 2
- NDT Level 3
These levels represent a progressive ascent in responsibility and expertise, with Level 1 being the entry point and Level 3 signifying high-level proficiency and comprehensive understanding of NDT methods and principles.
Global perspectives on qualifications and certifications of NDT personnel are crucial for maintaining uniformity and consistency in practices. The British Institute of Non-Destructive Testing (BINDT) is an example of an international entity working toward harmonizing the qualification and certification processes, ensuring a coherent approach to NDT & condition monitoring across the globe.
Standards and certifications in NDT are pivotal in upholding the reliability, credibility, and uniformity of nondestructive testing methods and practices. By following established standards and obtaining necessary certifications, NDT professionals can assure the quality and dependability of their work, thereby contributing to the safety and longevity of materials and structures in various industries.
Non-Destructive Testing Careers and Training
Within the expansive field of non-destructive testing, there are many opportunities for technicians who are inclined toward meticulous inspection and evaluation.
Building a career in NDT necessitates a profound understanding of testing methodologies that discern the integrity of materials without compromising their functionality, rendering this profession both intricate and indispensable.
Building a Career in Non-Destructive Testing
Starting a career in NDT is a good fit for individuals with an acumen for analytical precision and a penchant for technological advancements. This career path is steeped in continuous learning and necessitates a robust comprehension of various testing methods, including but not limited to, ultrasonic, magnetic-particle, and liquid penetrant testing.
The acquisition of pertinent knowledge is pivotal, enabling professionals to adeptly assess the internal and external conditions of materials, thereby precluding structural deficiencies.
NDT Certification Levels and Requirements
NDT professionals need to attain certifications to authenticate their proficiency, and these are segmented into three pivotal levels, denoting the depth of their expertise.
- NDT Level 1 empowers individuals with rudimentary proficiency to conduct specific tests under supervision.
- Transitioning to Level 2 signifies a heightened comprehension and the capability to execute and supervise tests autonomously.
- Attaining Level 3 is emblematic of advanced mastery, authorizing professionals to establish and oversee testing procedures and protocols.
Additionally, certain inspection methods and NDT equipment require additional training.
Top NDT Training and Certification Programs
Several reputed institutions offer extensive NDT training programs, designed to imbue aspiring professionals with the requisite skills and knowledge.
For instance, organizations such as ASNT provide platforms for networking and professional development, facilitating the refinement of skills and acquisition of knowledge.
Comprehensive training programs are instrumental in sculpting adept professionals equipped to navigate the nuanced landscape of non-destructive testing proficiently.
[Related read: The Best NDT Training Courses 2023]
Career Opportunities and Salary Expectations in NDT
The employment landscape in NDT is replete with diverse opportunities spanning various industries, as outlined in the above section. The versatility of this profession enables adept professionals to select a specialization aligned with their preferences and expertise.
Career progression is intertwined with continuous learning and the attainment of higher certification levels.
Salaries in NDT are proportionate with experience and certification levels, with Level 3 professionals being paid the highest salaries due to their advanced knowledge and leadership roles in developing and managing NDT procedures.
NDT is a multidisciplinary field offering a plethora of career opportunities for individuals inclined towards analytical evaluation and testing. The journey necessitates dedication to learning and adherence to rigorous standards to ensure the seamless integration into the diverse and dynamic environment of non-destructive testing.
Additional Resources in the Field of Non-Destructive Testing
In the realm of non-destructive testing, continuing education with the latest developments and technologies are crucial. Below are pivotal resources that every professional in the inspection field should consider to enhance their knowledge and expertise.
Recommended NDT Books and Publications
To deepen your understanding of non-destructive testing methods, a plethora of books and publications are available.
- The Inspectioneering Journal is a noteworthy publication, shedding light on new developments in the field of inspection and NDT. It offers in-depth articles, case studies, and insights from industry experts.
- The American Society for Nondestructive Testing also provides ample opportunities to access scholarly articles, journals, and books, serving as a contributor or peer reviewer, and thus is a significant resource for expanding one’s knowledge base in NDT.
Top NDT Forums and Online Communities
Engaging with online communities and forums is essential for discussion, knowledge exchange, and staying updated on industry trends and best practices.
- NDT.net is the largest open-access portal for Nondestructive Testing, offering a platform for conference proceedings, journal articles, news, products, and services. This portal is a fertile ground for professionals looking to delve into discussions, research, training, and certification in NDT.
- OnestopNDT is a platform backed by professionals, serves as an informative dais, elucidating every aspect related to non-destructive testing, thereby contributing to the knowledge pool of NDT enthusiasts.
- Check out LinkedIn groups centered around NDT technicians like NDT & Inspection Services Professionals and NDT Technologies (more here).
The Leading NDT Equipment Supplier
Equipping oneself with state-of-the-art tools is imperative for professionals in the field. NDT equipment providers like MFE Inspection Solutions specialize in NDT, RVI, and environmental inspection tools and are renowned suppliers in the industry, catering to a variety of inspection methods.
By using these resources, inspection professionals can gain skills and knowledge, and also foster connections with fellow experts while keeping pace with the advancements in non-destructive testing methodologies.