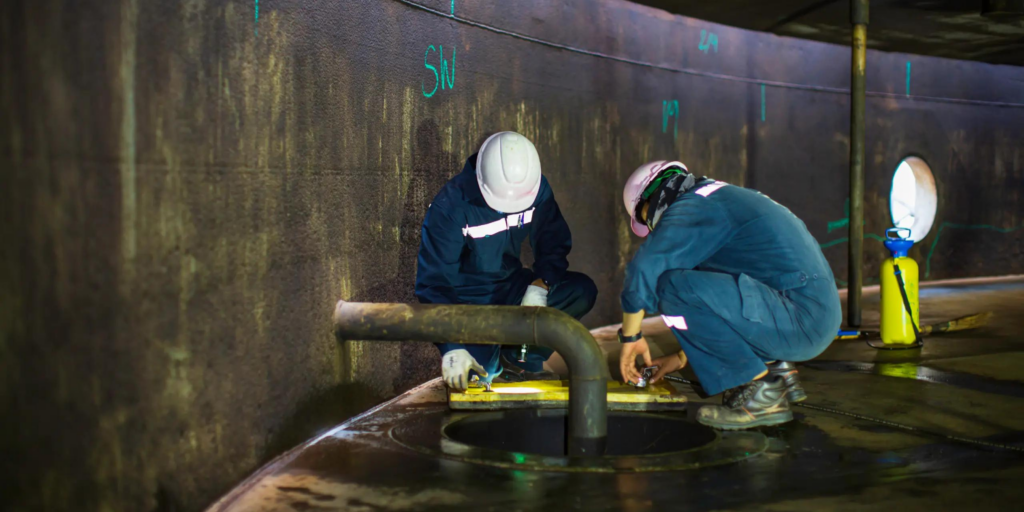
Guide
Leak Testing: An In-Depth Guide [New for 2025]
Leak Testing is an NDT method that uses pressure to detect and locate leaks in systems and components, ensuring the integrity, safety, and performance of these systems.
Alternate phrases for leak testing include:
- Leak detection
- Pressure testing
- Leak assessment
- Leak evaluation
- Leak verification
Leak testing is particularly effective for identifying and evaluating leaks and defects in systems and components, including:
- Pressure loss. Detects leaks that cause a drop in pressure within sealed systems such as pipelines, tanks, and HVAC systems.
- Gas leaks. Identifies and locates leaks of gases, including hazardous substances, in pipelines, valves, and storage containers.
- Liquid leaks. Finds leaks in liquid-carrying systems such as fuel lines, hydraulic systems, and water distribution networks.
- Seal integrity. Evaluates the effectiveness of seals and gaskets in preventing leaks in critical applications like automotive engines and aerospace components.
- Vacuum system integrity. Ensures the integrity of vacuum systems by detecting leaks that could compromise performance or safety.
Leak testing is used extensively in industries as diverse as oil and gas, power generation, aerospace, automotive, and manufacturing, where even small leaks can lead to significant safety hazards, environmental concerns, and operational inefficiencies.
This article provides a comprehensive overview of leak testing, exploring the tools and techniques used, the various types of leak testing methods, the scenarios where it’s most beneficial, and the industries that use it most often for inspections.
Have a specific topic in mind? Use the menu to the right to jump around within this guide.
What Is Leak Testing?
At a high level, a leak test involves applying a test medium (such as gas, liquid, or air) to the system and detecting the presence of leaks through various means.
The primary goal of leak testing is to ensure that systems are free from leaks that could compromise their integrity, safety, and functionality.
Keep reading to learn how leak testing works and some of its primary advantages—as well as its limitations.
Principles of Leak Testing
The fundamental principle of leak testing is based on the detection of escaping test medium from a pressurized system or component.
Here are the key steps involved in leak testing:
- Pressurization. The system or component under test is pressurized using a test medium, such as air, gas, or liquid. The pressure applied is usually higher than the operating pressure of the system to ensure that any leaks can be detected.
- Detection. Various techniques and tools are used to detect the presence of leaks. These techniques can include visual inspection, acoustic detection, chemical detection, or electronic sensors. The choice of detection method depends on the size of the leak, the type of test medium, and the specific requirements of the inspection.
- Quantification. In some cases, it is important to quantify the size and rate of the leak. This can be done using specialized instruments that measure the flow rate or volume of the escaping test medium.
Advantages of Leak Testing
- High sensitivity. Leak testing methods are highly sensitive and can detect even the smallest leaks that might not be noticeable through other inspection methods.
- Versatility. Leak testing can be applied to a wide range of systems and components, including pipelines, tanks, valves, heat exchangers, and sealed containers.
- Safety assurance. By detecting and locating leaks, leak testing helps ensure the safety and reliability of critical systems, preventing potential hazards and failures.
- Environmental protection. Leak testing is crucial for identifying leaks in systems that handle hazardous or environmentally sensitive materials, helping to prevent contamination and environmental damage.
Limitations of Leak Testing
- Complexity. Some leak testing methods can be complex and require specialized equipment and trained personnel to perform accurately.
- Time-consuming. Certain leak testing methods can be time-consuming, especially when testing large systems or components with multiple potential leak points.
- Environmental sensitivity. The effectiveness of some leak testing methods can be influenced by environmental conditions, such as temperature, humidity, and background noise.
Leak Testing Tools
Leak Testing relies on a variety of specialized tools and equipment designed to pressurize systems, detect leaks, and quantify leak rates. These tools are essential for performing accurate and reliable inspections.
Below is a detailed overview of the primary tools used in leak testing. Below are the most common types of acoustic emission testing tools. We’ve organized these tools into four categories, with specific types listed for each one.
1. Pressure Sources
I. Gas cylinders and compressors are devices used to pressurize the system or component under test using gasses such as air, nitrogen, or helium.
- How they work. Gas cylinders provide a controlled source of pressurized gas, while compressors generate pressurized air on-site.
- Applications. Used to pressurize systems for leak detection, suitable for both small-scale and large-scale applications.
II. Liquid pumps are pumps used to pressurize the system with liquids such as water or oil.
- How they work. The pump forces the liquid into the system, increasing the internal pressure.
- Applications. Commonly used for hydrostatic testing of pipelines, tanks, and pressure vessels.
2. Detection Devices
I. Bubble test equipment are simple tools such as soap solutions or bubble-forming liquids.
- How they work. The pressurized system is coated with the bubble solution, and leaks are detected by observing the formation of bubbles.
- Applications. Suitable for low-pressure systems and visible leak detection, often used in plumbing and HVAC inspections.
II. Helium mass spectrometers are highly sensitive instruments that detect trace amounts of helium gas.
- How they work. Helium is used as a tracer gas, and the mass spectrometer detects its presence at leak points.
- Applications. Ideal for high-sensitivity leak detection in vacuum systems, aerospace components, and sealed electronics.
III. Ultrasonic leak detectors are devices that detect the high-frequency sound waves produced by gas or air escaping from a leak.
- How they work. The detector converts ultrasonic sound waves into audible signals, allowing the operator to locate the leak.
- Applications. Used for detecting leaks in pressurized gas systems, steam lines, and compressed air systems.
IV. Pressure decay testers are instruments that measure the drop in pressure within a sealed system over time.
- How they work. The system is pressurized, and the tester monitors the pressure. A decrease in pressure indicates a leak.
- Applications. Suitable for leak testing of sealed components, containers, and assemblies.
3. Tracer Gas Detection Systems
I. Sniffer probes are handheld probes used to detect the presence of tracer gasses such as helium or hydrogen.
- How they work. The probe is moved around potential leak areas, and the detection system alerts the operator to the presence of the tracer gas.
- Applications. Used for pinpointing leaks in pipelines, refrigeration systems, and vacuum chambers.
II. Infrared gas analyzers are instruments that use infrared sensors to detect specific gasses.
- How they work. The analyzer measures the absorption of infrared light by the tracer gas, providing a quantitative measure of the gas concentration.
- Applications. Suitable for detecting leaks in systems containing refrigerants, hydrocarbons, and other infrared-absorbing gases.
4. Sealing and Isolation Tools
I. Inflatable plugs and bladders are devices used to temporarily seal sections of a pipeline or system during leak testing.
- How they work. The plug or bladder is inserted into the pipeline and inflated to create a seal, isolating the section for testing.
- Applications. Commonly used in pipeline maintenance, sewer inspections, and pressure testing of isolated sections.
II. Vacuum chambers are enclosures used to create a vacuum environment around the test object.
- How they work. The chamber is evacuated to a low pressure, and leaks are detected by monitoring pressure changes or using tracer gasses.
- Applications. Ideal for testing sealed electronics, aerospace components, and small assemblies.
Types of Leak Testing
Leak Testing encompasses several techniques, each tailored to specific inspection needs and applications. These methods vary in their approach to detecting and quantifying leaks. Here are the main types of leak testing:
1. Bubble Testing
A simple and cost-effective method that uses a soap solution or bubble-forming liquid to detect leaks.
- How it works. The pressurized system is coated with the bubble solution, and leaks are identified by observing the formation of bubbles at leak points.
- Applications. Suitable for low-pressure systems, plumbing, HVAC inspections, and identifying visible leaks.
2. Pressure Decay Testing
A method that measures the drop in pressure within a sealed system over time to detect leaks.
- How it works. The system is pressurized, and the pressure is monitored. A decrease in pressure indicates a leak.
- Applications. Used for testing sealed components, containers, and assemblies, commonly applied in automotive, aerospace, and packaging industries.
3. Vacuum Decay Testing
A technique that detects leaks by monitoring the increase in pressure within a vacuum-sealed system.
- How it works. The system is evacuated to a vacuum, and the pressure is monitored. An increase in pressure indicates a leak.
- Applications. Ideal for testing sealed electronics, medical devices, and vacuum systems.
4. Tracer Gas Testing
A highly sensitive method that uses tracer gasses such as helium or hydrogen to detect and locate leaks.
- How it works. The system is pressurized with the tracer gas, and detection equipment such as mass spectrometers or sniffer probes is used to identify the presence of the gas at leak points.
- Applications. Suitable for high-sensitivity leak detection in vacuum systems, aerospace components, refrigeration systems, and sealed electronics.
5. Helium Mass Spectrometry
An advanced method that uses helium as a tracer gas and detects leaks with a mass spectrometer.
- How it works. TThe system is pressurized with helium, and a mass spectrometer detects helium atoms escaping from leaks, providing precise leak location and quantification.
- Applications. Ideal for high-sensitivity leak detection in critical applications such as aerospace, semiconductor manufacturing, and high-vacuum systems.
6. Ultrasonic Leak Detection
A method that detects the high-frequency sound waves produced by gas or air escaping from a leak.
- How it works. An ultrasonic detector converts the ultrasonic sound waves into audible signals, allowing the operator to locate the leak.
- Applications. Used for detecting leaks in pressurized gas systems, steam lines, compressed air systems, and pipelines.
7. Hydrostatic Testing
A method that uses water or another liquid to pressurize the system and detect leaks.
- How it works. The system is filled with water and pressurized, and leaks are identified by observing the escape of water from the system or by measuring pressure drops.
- Applications. Commonly used for testing pipelines, pressure vessels, tanks, and plumbing systems.
When Is Leak Testing Required
Leak Testing is essential in a range of scenarios to ensure the quality, safety, and reliability of systems and components.
Here are some key situations when leak testing is required:
1. Quality Control and Assurance in Manufacturing
- Production processes. During manufacturing, leak testing is used to verify that components and systems meet specified quality standards. This involves detecting leaks that could compromise the integrity and performance of the final product.
- Incoming material inspection. Leak testing is employed to inspect raw materials and components before they are used in production, ensuring they meet the required specifications and are free from leaks.
2. Safety Compliance and Regulatory Requirements
- Regulatory standards. Many industries are subject to stringent safety regulations that mandate regular leak testing. Compliance with these regulations ensures that systems and components meet safety standards, reducing the risk of accidents and failures.
- Certification and accreditation. Leak testing is often required for certification purposes, such as obtaining pressure vessel and pipeline certifications from regulatory bodies.
3. Preventive Maintenance and Scheduled Inspections
- Routine maintenance. Leak testing is part of regular preventive maintenance schedules to monitor the condition of critical systems and infrastructure. This helps in early detection of potential leaks, preventing unexpected failures and downtime.
- Condition monitoring. Continuous or periodic leak testing enables the monitoring of systems under operational conditions, providing valuable data on their health and predicting their remaining service life.
4. Environmental Protection
- Hazardous systems. Leak testing is crucial for identifying leaks in systems that handle hazardous or environmentally sensitive materials, such as chemicals, gasses, and fuels. Detecting and addressing leaks helps prevent environmental contamination and health risks.
- Pipeline monitoring. Leak testing is used to monitor pipelines for leaks that could lead to environmental disasters, ensuring the safe and efficient transportation of fluids and gasses.
5. Research and Development
- Material and component testing. In research and development, leak testing helps characterize new materials and components, studying their behavior under different conditions. This information is vital for developing advanced materials and systems with enhanced performance and reliability.
- Prototype evaluation. Leak testing is used to evaluate prototypes, identifying any flaws or weaknesses that need to be addressed before full-scale production.
The Top 5 Industries that Rely on Leak Testing + Specific Applications They Use
Leak Testing is a versatile non-destructive testing method with applications across a wide range of industries.
Here are the top five industries that use leak testing, with specific applications covered for each one.
Oil and Gas Industry
In the oil and gas industry, leak testing is vital for maintaining the safety and reliability of pipelines and other infrastructure.
- Pipeline integrity testing. Leak testing is used to detect leaks in pipelines, ensuring their integrity and preventing leaks or ruptures that could lead to environmental disasters.
- Storage tank testing. Leak testing helps ensure the integrity of storage tanks, detecting leaks that could lead to the loss of stored materials and environmental contamination.
- Well integrity testing. Leak testing is used to verify the integrity of wells, detecting leaks that could compromise safety and operational efficiency.
Power Generation Industry
In the power generation industry, leak testing is essential for maintaining the integrity of critical components in power plants.
- Steam generator testing. Leak testing is used to detect leaks in steam generators, ensuring they can operate efficiently and safely under high pressure and temperature conditions.
- Condenser testing. Leak testing helps verify the integrity of condensers, detecting leaks that could compromise their performance and efficiency.
- Transformer and generator testing. Leak testing is employed to ensure the integrity of transformers and generators, detecting leaks that could lead to equipment failure and power outages.
Manufacturing Industry
In the manufacturing industry, leak testing is crucial for ensuring product quality and reliability.
- Quality assurance. Leak testing is used to inspect raw materials, intermediate products, and final assemblies for leaks, ensuring that only defect-free products reach the customer.
- Component testing. Leak testing is employed to verify the integrity of manufactured components, ensuring they meet design specifications and performance requirements.
- Packaging testing. Leak testing helps ensure the integrity of packaging, detecting leaks that could lead to product contamination and spoilage.
Aerospace Industry
The aerospace industry relies heavily on leak testing to maintain the safety and performance of aircraft components.
- Fuel system integrity. Leak testing is used to ensure the integrity of aircraft fuel systems, detecting leaks that could lead to fuel loss and potential safety hazards.
- Cabin pressure testing. Leak testing helps verify the integrity of aircraft cabins, ensuring they can maintain proper pressure levels during flight.
- Hydraulic system testing. Leak testing is essential for maintaining the performance and reliability of aircraft hydraulic systems, detecting leaks that could compromise system functionality.
Automotive Industry
The automotive industry employs leak testing to ensure the quality and safety of vehicle components.
- Engine component testing. Leak testing is used to detect leaks in engine components such as cylinder heads, crankcases, and cooling systems, ensuring they meet safety and performance standards.
- Fuel system testing. Leak testing helps ensure the integrity of fuel systems, detecting leaks that could lead to fuel loss, environmental contamination, and safety risks.
- HVAC system testing. Leak testing is used to verify the integrity of vehicle HVAC systems, ensuring they can maintain proper temperature and humidity levels.
Best Practices for Leak Testing
To ensure the effectiveness and reliability of leak testing, it is essential to follow best practices. These guidelines help maximize the accuracy of inspections and minimize the risks associated with the testing process.
1. Proper Training and Certification
- Qualified personnel. Ensure that leak testing is conducted by trained and certified technicians. Certification from recognized bodies such as the American Society for Nondestructive Testing (ASNT) or equivalent organizations is essential. Properly trained personnel are more likely to conduct accurate inspections and correctly interpret results.
- Continuous education. Encourage ongoing education and training to keep technicians updated on the latest techniques, equipment, and industry standards. This can include workshops, seminars, and certification renewal courses. Staying current with industry developments helps maintain high standards of inspection quality.
2. Appropriate Equipment Selection
- Selection of pressure sources. Choose the appropriate pressure sources (gas cylinders, compressors, or liquid pumps) based on the type of system and the test requirements. The correct pressure source ensures the system is adequately pressurized for accurate leak detection.
- Detection device selection. Use suitable detection devices (bubble test equipment, helium mass spectrometers, ultrasonic leak detectors, etc.) that match the sensitivity and specificity needed for the inspection. The right detection device enhances the accuracy of leak identification.
3. Surface Preparation
- Clean surfaces. Thoroughly clean the surface of the system or component to remove any contaminants such as dirt, grease, oil, and paint. Contaminants can impede the detection of leaks and affect the visibility of indications. Proper cleaning ensures accurate and reliable results.
- Smooth surfaces. Ensure the surface is smooth and free from any coatings or obstructions that might hinder the inspection process. Smooth surfaces improve the effectiveness of detection devices and enhance the visibility of leaks.
4. Inspection Procedures
- Standard operating procedures (SOPs). Develop and adhere to detailed SOPs for each type of leak testing. SOPs ensure consistency, thoroughness, and compliance with regulatory requirements. They provide a step-by-step guide to performing inspections, helping to maintain high standards.
- Controlled application. Apply the test medium (gas or liquid) evenly across the system and allow sufficient time for the medium to permeate any potential leaks. Controlled application and appropriate dwell time are crucial for the test medium to reveal all leaks effectively.
- Leak detection. Use the selected detection devices to identify leaks accurately. Ensure that the detection method is appropriate for the type and size of leaks expected.
5. Inspection Conditions
- Adequate lighting. Ensure appropriate lighting conditions for the inspection. Use visible light for inspections with bubble tests and UV light for inspections with fluorescent tracer gasses. Adequate lighting is essential for accurately detecting and interpreting indications.
- Environmental control. Perform inspections in a controlled environment to avoid contamination and ensure consistent results. Factors such as temperature, humidity, and cleanliness of the inspection area can affect the test outcomes.
6. Data Recording and Analysis
- Systematic documentation. Record and document inspection data systematically, including leak locations, sizes, and rates. Accurate documentation helps in tracking the condition of systems over time and provides valuable information for future inspections.
- Advanced software. Utilize advanced data analysis software that can enhance the interpretation of results, generate detailed reports, and store inspection records efficiently. Digital tools help streamline the inspection process and improve accuracy.
7. Regular Equipment Maintenance
- Routine checks. Perform regular maintenance and routine checks on leak testing equipment to ensure it is in good working condition. This includes inspecting pressure sources, detection devices, and calibration tools for wear and damage.
- Calibration. Regularly calibrate inspection equipment according to manufacturer guidelines and industry standards to maintain accuracy and reliability. Calibration ensures that the equipment performs correctly and provides consistent results.
8. Safety Protocols
- Protective gear. Ensure that technicians wear appropriate protective gear, such as gloves, safety glasses, and protective clothing, to protect against exposure to test mediums and chemicals used in the detection process. Safety gear helps prevent skin contact and inhalation of potentially harmful substances.
- Safe handling of chemicals. Follow safe handling procedures for chemicals and gasses used in leak testing, including proper storage, use, and disposal. Proper handling minimizes health risks and environmental impact.
- Ventilation. Conduct inspections in well-ventilated areas to avoid the buildup of fumes from test mediums and chemicals. Good ventilation reduces the risk of inhaling hazardous vapors.
9. Compliance with Regulations
- Regulatory standards. Ensure compliance with all relevant regulatory standards and guidelines for leak testing. This includes obtaining necessary certifications and adhering to industry best practices. Compliance ensures that inspections meet required safety and quality standards.
- Inspections and audits. Conduct regular inspections and audits to verify compliance with safety protocols and regulatory requirements. Address any identified issues promptly to maintain a safe and compliant inspection environment.