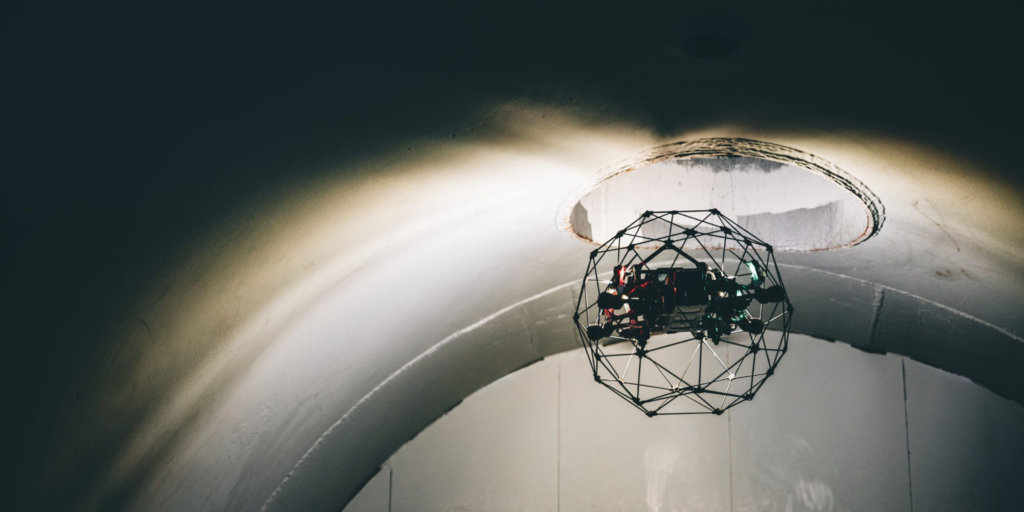
Article
Drones in Maritime Inspection: A Time-Saving, Cost-Effective Tool
The implementation of drones during shipping inspections is becoming essential as the maritime industry realizes the potential of drones to eliminate safety hazards, substantially lower maintenance costs, and perform inspections without the loss of production time. Drones are an advantageous tool while performing inspections in the air, underwater, and now even inside confined spaces such as holds and ballast tanks.
The detection of corrosion is paramount in the maritime industry with corrosion having the potential to inflict damage from the port’s infrastructures to the exterior and interior of vessels. It is important to conduct routine inspections in order to detect corrosion damage, but also corrosion must be consistently monitored to track the corrosion’s growth. Lack of frequency should not be a limitation in such an important inspection. Drones can provide high quality visual representations of the inspection area that can be viewed in real-time or saved for future comparisons.
“The more you know about what’s out there in terms of NDT tools and monitoring techniques, the more equipped you’ll be to make a choice that will preserve the longevity of the assets you’re in charge of monitoring,” says Jason Acerbi, CTO and VP of Sales at MFE.
In the Air
In the air, using drones eliminates the need to utilize expensive and time-consuming methods. The taller tanks on ships can reach more than 25 meters high and may require the construction of scaffolding and hung staging equipment. Not only is this dangerous for inspectors, but this process requires machinery to be shut down–a very costly practice. Drones are able to carry out the same inspection quickly and efficiently with inspectors remaining on the ground.
In order to fly a drone as a commercial operator, the FAA requires pilots to pass a Part 107 Certification Exam and follow specific guidelines to ensure maximum safety while flying. There are drone training courses that will prepare you for the exam and train you for an industrial environment inspection such as MFE Rentals’ five-day Advanced Drone Piloting Course. The course trains pilots in the complexities involved in advanced commercial drone operation such as creating a pre-flight checklist, compensating for erratic movement, accommodating for structures in line of flight, making appropriate camera choices, and creating a flight plan.
FAA regulations require pilots to keep their drone within sight during flight and use a secondary visual observer for those utilizing first person views or similar technology. Pilots may also only fly during daylight or in twilight and maintain a maximum of 400 feet above the ground or higher if the drone remains within 400 feet of a structure.
However, the FAA does not monitor the enclosed air spaces involved in many industrial inspections. Consequently, the FAA Part 107 Exam is not a requirement for the inspection of confined spaces.
Confined Spaces
Indoor inspection such as inside the hull of a ship has many challenges. The atmosphere within a tank is dark and hot, and inside the tanks, inspectors may be exposed to dangerous gases that may not be detectable by smell. Inspections are usually performed by a team of inspectors who must climb on ropes without safety nets. If not ropes, then scaffolding must be constructed within the space. This is a time-consuming, expensive, and dangerous project.
The use of caged drone technology allows inspectors to conduct these inspections in a fraction of the time while eliminating health risks and financial costs. Caged drone manufacturer Flyability conducted a case study with their Elios caged drone and was able to perform an inspection on six tanks in two days compared to the tanks’ usual inspections that lasted 18 days and consisted of three to four rope inspectors.
In a subsequent case study, Flyability used Elios to inspect the ballast tank of one of CMA CGM’s container ships. They needed to inspect the 323 meter vessel’s general integrity, corrosion level, and monitor the anodes within the ballast. The ballast was 15 meters long with two manholes that were 600mm and 400mm respectively. An inspection that normally required three to four inspectors utilizing ropes, oxygen monitoring devices, and extensive safety equipment was conducted by one pilot with three flights that were 10 minutes long each. The caged drone’s collision tolerance and onboard lighting allowed the pilot to maneuver the drone safely and efficiently without any external lighting.
Underwater
Drones can also be used to perform visual inspections underwater. Underwater drones allow port authorities and border security professionals to perform hull inspections on each passing vessel. These underwater drones or ROVs eliminate the need to send a diver underwater and vessels aren’t forced to incur expensive delays while drydocking.
The ROV camera records the condition of the hull markings, rudders, sacrificial anodes, and propellers. Also the Deep Trekker ROV systems, like the PIVOT, can be outfitted with a thickness gauge to test the thickness of the hull.
As technology advances, the use of drones will only increase with features on the horizon such as detailed 3D models of interior assets and more advanced automations. With its use in the air, confined spaces, and under water, drones are a crucial time-saving and cost effective tool for the maritime industry.
To learn more about how the Flyability Elios and Elios 2 or to request a quote, contact us at sales@mfe-is.com.