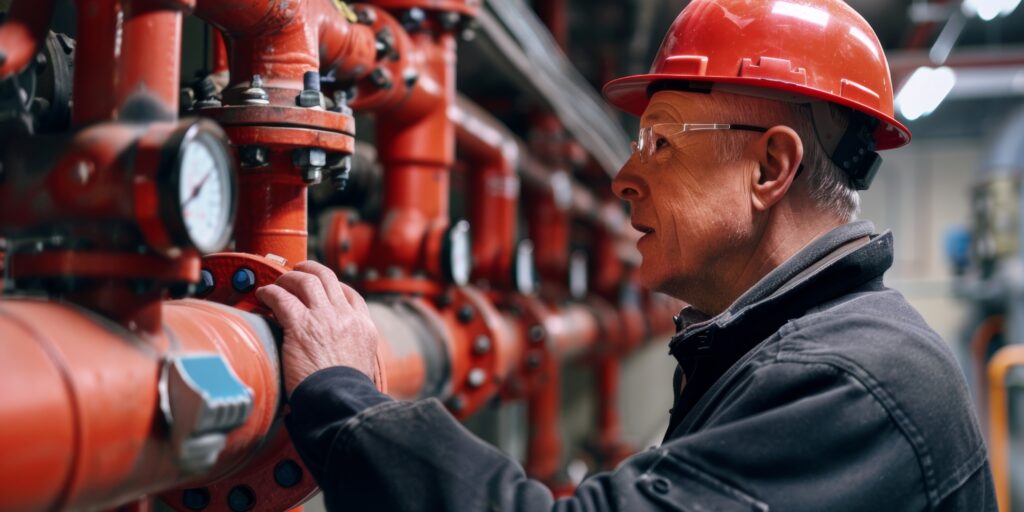
Guide
Gas Leak Detectors: Top Models & More [New for 2025]
Gas leak detectors are devices used to identify the presence of gas leaks by sensing and measuring various gases in an environment to ensure safety and prevent potential hazards.
→ Jump to gas leak detector rentals and sales.
In industrial inspections, gas leak detectors are essential tools for identifying dangerous leaks that could pose serious safety risks. Think of a gas leak detector as a super-sensitive nose that can smell even the smallest gas leaks, whether they’re from natural gas, methane, or other hazardous gases.
It helps workers in industries like oil and gas, power generation, and manufacturing to catch leaks early, preventing accidents, saving costs, and ensuring the environment stays safe. By “sniffing” out leaks, gas leak detectors play a critical role in keeping operations running smoothly and protecting both people and the planet.
Gas leak detectors are also commonly called:
- Gas sniffers
- Gas monitors
- Gas detection units
- Gas detection systems
- Leak detection instruments
- Gas analyzers
Best Gas Leak Detectors for Rent and Sale [New for 2025]
Choosing the right gas leak detector is critical for ensuring safety and compliance in various industrial and residential settings. Here are some of the top models on the market, organized by type.
Jump to the specific type of gas leak detector you’re looking for:
Optical Gas Imaging Cameras
1. MFE Detect LW
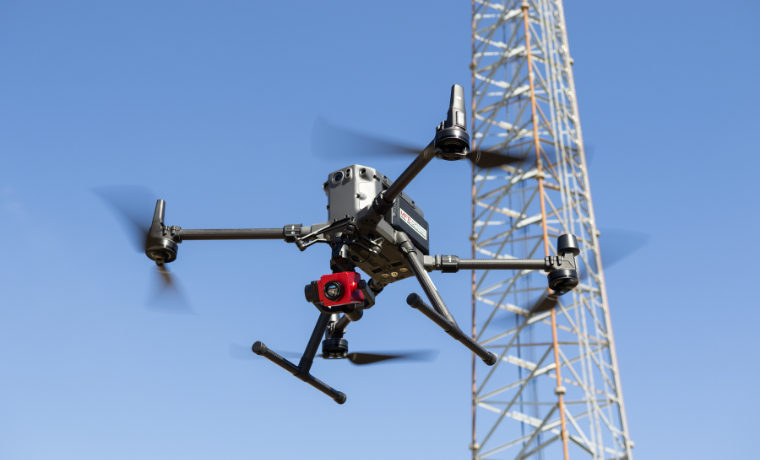
The MFE Detect LW is a pioneering long-wave infrared (LWIR) optical gas imaging (OGI) camera, purpose-built for aerial methane leak detection using DJI M300/M350 drones. With its real-time visualization and compliance with OOOOa, b, c, and Appendix K standards, the MFE Detect LW streamlines gas inspection, especially in large, industrial settings.
- Type of gas leak detector. Long-Wave Infrared Optical Gas Imaging Camera
- Key features. High-responsivity uncooled focal plane array detector, real-time methane visualization, DJI Pilot software compatibility, and dual video output for versatile aerial inspections.
- Types of gas it can detect. Primarily methane
- Key applications. Ideal for large-scale industrial inspections, environmental compliance checks, landfill monitoring, and aerial methane emission assessments across the energy sector.
Learn more about the MFE Detect LW.
2. MFE Detect MW (MFE OGI Camera)
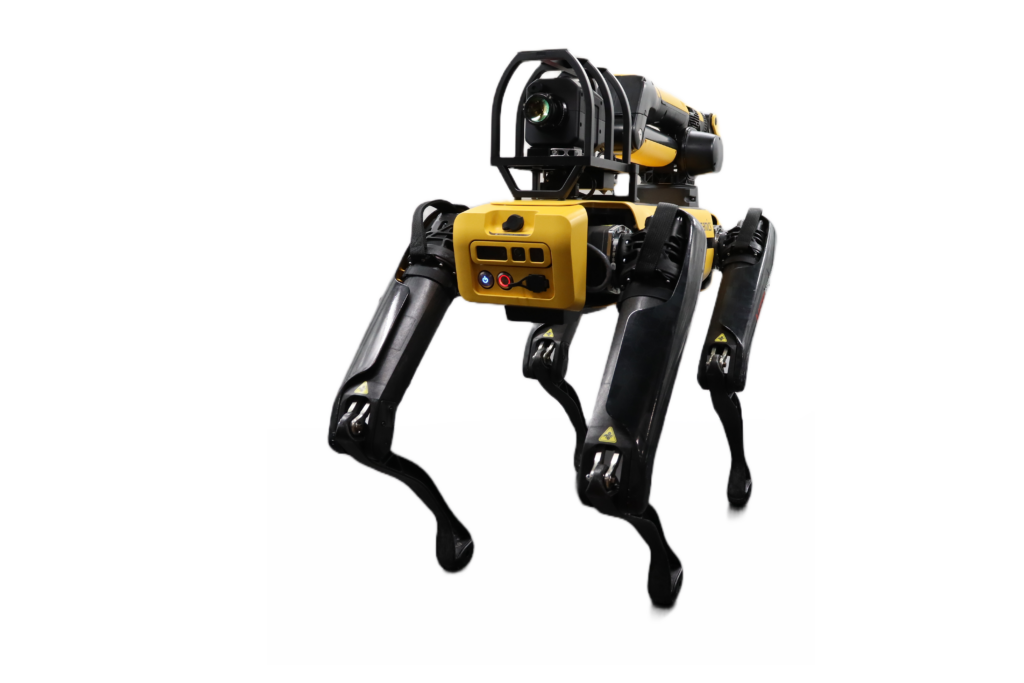
The MFE OGI Camera is a highly specialized optical gas imaging device designed to detect and visualize hydrocarbon gas leaks such as methane, propane, and butane. This advanced tool is crucial for industries looking to maintain safety standards, reduce environmental impact, and enhance operational efficiency by quickly identifying and addressing gas leaks.
- Type of gas leak detector. Optical Gas Imaging Camera
- Key features. High sensitivity to hydrocarbon gases, capable of capturing gas plumes in motion, integrates with software for detailed analysis.
- Types of gas it can detect. Methane, propane, butane, and other hydrocarbons
- Key applications. Widely used in the oil and gas industry, petrochemical plants, and biogas facilities to monitor and manage gas emissions and improve safety protocols.
Learn more about the MFE Detect MW (MFE OGI Camera).
3. OGI – 640 Optical Gas Imaging Payload
The OGI – 640 Optical Gas Imaging Payload is a high-performance camera specifically designed for detecting and visualizing small gas leaks in industrial settings. This device integrates seamlessly with unmanned aerial vehicles (UAVs) to provide aerial surveillance capabilities that enhance leak detection processes in expansive and hard-to-reach areas.
- Type of gas leak detector. Optical Gas Imaging Camera
- Key features. Features a spectral range optimized for methane and other hydrocarbons, high thermal sensitivity, and real-time imaging capabilities
- Types of gas it can detect. Methane, sulfur hexafluoride, and 3+ more
- Key applications. Used predominantly in the oil and gas sectors for pipeline monitoring, tank inspections, and large-scale facility surveys
Learn more about the OGI – 640.
3. FLIR GF320
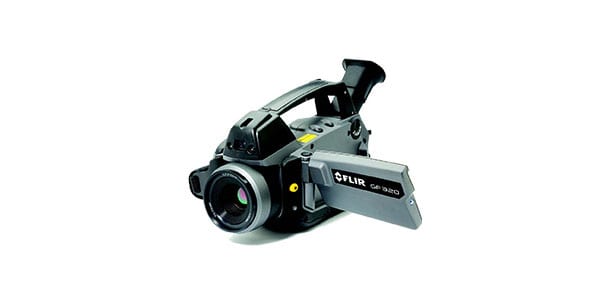
The FLIR GF320 is an advanced infrared camera designed for detecting volatile organic compounds (VOCs) and other hydrocarbon gases. This thermal imaging camera is renowned for its ability to visually identify gas leaks and pinpoint their exact location, making it a vital tool in industrial maintenance and environmental monitoring.
- Type of gas leak detector. Infrared Camera.
- Key features. High sensitivity mode, captures temperatures from -20°C to +350°C, incorporates a cooled Quantum Well Infrared Photodetector (QWIP)
- Types of gas it can detect. Methane, propane, butane, and 20+ more
- Key applications. Oil and gas industry inspections, chemical plant monitoring, and environmental regulations compliance
Learn more about the FLIR GF320.
4. FLIR GF77
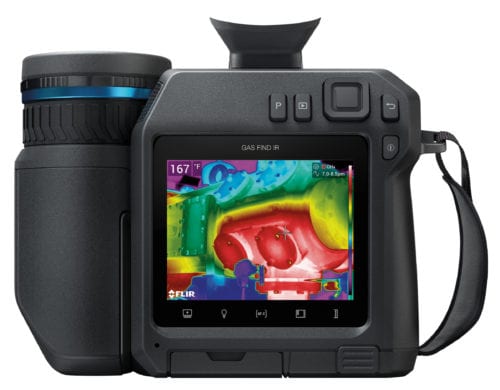
The FLIR GF77 is a groundbreaking uncooled optical gas imaging camera designed to detect methane, sulfur hexafluoride, and other gases. This cost-effective solution broadens the capabilities of industrial gas detection by providing high sensitivity, continuous gas visualization, and improved accuracy and safety without the need for cooling.
- Type of gas leak detector. Uncooled Optical Gas Imaging Camera
- Key features. Affordable alternative with a broad spectral range, capable of detecting benzene, ethanol, ethylbenzene, heptane, hexane, isoprene, methanol, MEK, MIBK, pentane, 1-pentene, toluene, xylene, butane, ethane, methane, propane, ethylene, and propylene.
- Types of gas it can detect. Primarily used for detecting methane, sulfur hexafluoride, and 17+ more hydrocarbon-based gases
- Key applications. Ideal for detecting and visualizing gas leaks in industrial settings, environmental monitoring, and energy industry applications such as oil and gas extraction and refining
Learn more about the FLIR GF77.
Multi-Gas Detectors
5. Teledyne FLIR MUVE C360
The Teledyne FLIR MUVE C360 is a multi-gas detector specifically designed for use with unmanned aerial systems (UAS) to enhance situational awareness in hazardous environments. This cutting-edge tool rapidly assesses chemical hazards, providing real-time data that can be critical for safety in emergency response situations.
- Type of gas leak detector. Multi-Gas Detector for UAS
- Key features. Integrates with FLIR VueLink, provides a 360-degree view, can detect up to eight chemical hazards simultaneously, offers plug-and-play integration with UAS.
- Types of gas it can detect. Capable of detecting a wide range of chemical threats including VOCs, toxic gases, and combustibles
- Key applications. Primarily used in emergency response, environmental monitoring, and industrial inspections
Learn more about the Teledyne FLIR MUVE C360.
6. RAE Systems QRAE 3
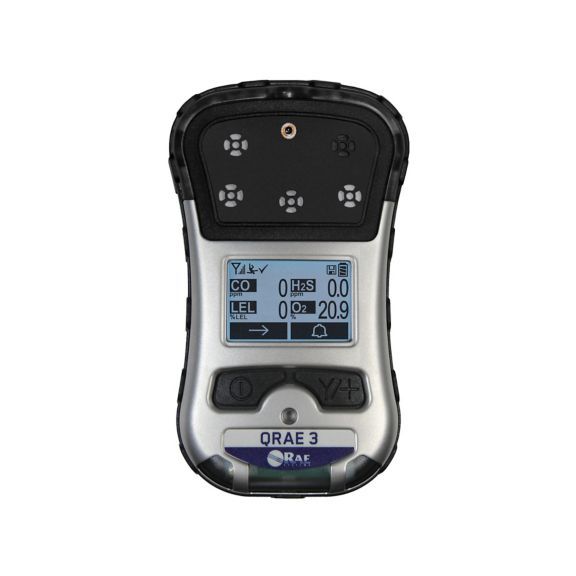
The RAE Systems QRAE 3 is a versatile, rugged four-gas monitor designed for a wide range of applications in hazardous environments. This portable detector is capable of detecting combustibles, oxygen, carbon monoxide, and hydrogen sulfide, making it an essential tool for ensuring workplace safety.
- Key applications. Ideal for confined space entry and general safety and compliance in chemical plants, oil and gas operations, and emergency response environments
- Type of gas leak detector. Portable Multi-Gas Monitor
- Key features. Easy-to-change battery pack, large graphical display, real-time gas concentration readings, and fully automated bump testing and calibration with AutoRAE 2
- Types of gas it can detect. Combustibles, oxygen, carbon monoxide, hydrogen sulfide.
Specific Gas Detectors
7. SPX MGD2002
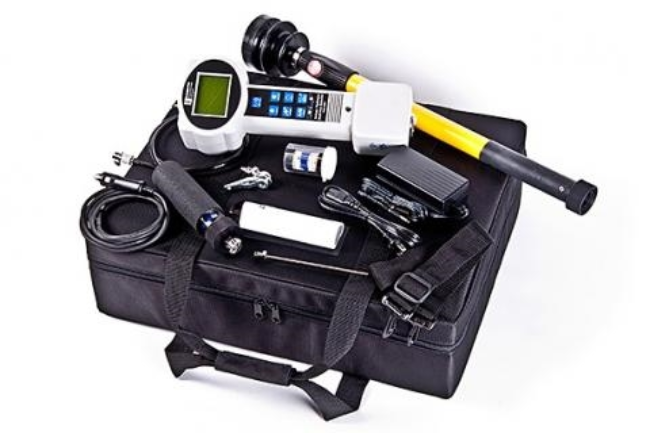
The SPX MGD2002 Multi-Gas Leak Detector is designed to pinpoint the precise location of leaks in various enclosed environments. This highly sensitive detector is suitable for detecting helium, hydrogen, and other gases, making it ideal for a range of applications from utility to industrial environments.
- Type of gas leak detector. Multi-Gas Leak Detector
- Key features. High sensitivity settings for minute leak detection, digital signal processing, and versatile sensor options
- Types of gas it can detect. Helium, hydrogen, and others
- Key applications. Utility companies use it for integrity tests on gas lines and tanks, while it is also applicable in HVAC systems and vehicle maintenance facilities for leak testing
Learn more about the SPX MGD2002.
Acoustic Imagers
8. Crysound 2623 – Acoustic Imager
The Crysound 2623 Acoustic Imager is engineered for exceptional precision in locating and visualizing sound sources that indicate leaks and discharges in industrial environments. This advanced tool combines auditory and visual elements to provide real-time analysis, making it an invaluable asset for maintenance teams.
- Type of gas leak detector. Acoustic Imaging Camera
- Key features. High-resolution acoustic imaging, real-time sound mapping, lightweight and ergonomic design, and capable of operating in noisy environments
- Types of gas it can detect. Detects leaks through sound, not specific to any one gas but effective for any emitting audible frequencies under pressure
- Key applications. Particularly useful in compressed air systems, steam systems, and vacuum systems where detecting gas, air, or vacuum leaks are critical for operational efficiency and safety
Learn more about the Crysound 2623.
9. Fluke SV600
The Fluke SV600 Fixed Acoustic Imager is designed for continuous monitoring in industrial environments. This advanced tool uses sound imaging to detect and visualize air and gas leaks or changes in mechanical sound signatures, which could indicate equipment failures. It is particularly useful for monitoring compressors, steam systems, and vacuum systems in real-time, enhancing preventative maintenance strategies.
- Type of gas leak detector. Fixed Acoustic Imaging Camera
- Key features. Continuous sound mapping, durable for industrial use, integrates with the Fluke Connect software for data analysis and reporting.
- Types of gas it can detect. Primarily used for detecting air and gas leaks through acoustic signatures.
- Key applications. Ideal for industries such as manufacturing, utilities, and oil and gas, where early detection of leaks can prevent large-scale operational disruptions.
Learn more about the Fluke SV600.
10. Crysound 8124
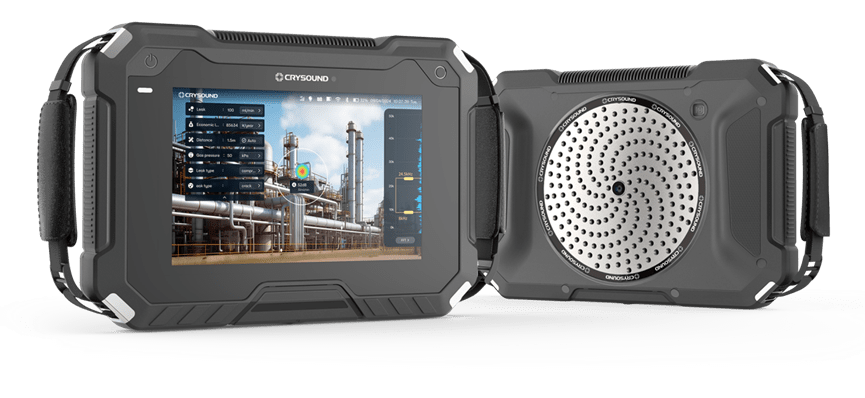
The Crysound 8124 Handheld Acoustic Imager is engineered for precision in detecting and visualizing sound sources that signal leaks and emissions. This portable device is optimized for use in a variety of industrial environments, offering real-time audio and visual leak detection that aids in efficient maintenance and operations.
- Type of gas leak detector. Handheld Acoustic Imaging Camera
- Key features. Real-time sound visualization, lightweight design, easy to operate with a simple user interface, capable of distinguishing sound frequencies associated with leaks.
- Types of gas it can detect. Designed to detect a range of gas leaks audible within human hearing ranges, particularly effective for air and steam leaks.
- Key applications. Useful in sectors like utilities and manufacturing where quick and accurate detection of leaks can prevent downtime and enhance safety.
Learn more about the Crysound 8124.
Choosing the Right Gas Leak Detector
Need help finding the right gas leak detector? There are several factors that should guide your decision, including the specific requirements of the environment and the type of gas or gases you need to detect.
Here are four key considerations when choosing a gas leak detector, as well as information on the different types out there to help you choose.
Factors to Consider
1. Type of Gas
Different detectors are optimized for different gases. Ensure the detector is suitable for detecting the specific gases used in your facility.
2. Sensitivity and Accuracy
The detector should have the sensitivity required to detect the smallest leak at the necessary accuracy levels to prevent false alarms and ensure safety.
3. Environmental Conditions
Consider whether the detector needs to operate in extreme temperatures, humid conditions, or in the presence of other chemicals that could affect its operation.
4. Regulatory Requirements
Ensure the gas leak detector meets all local and international safety standards and certifications relevant to your industry.
Types of Gas Leak Detectors
There are several types of gas leak detectors, each suited to different operational needs:
1. Portable Detectors
These are handheld devices that provide flexibility and mobility, ideal for personnel to carry around and use in different locations within a facility.
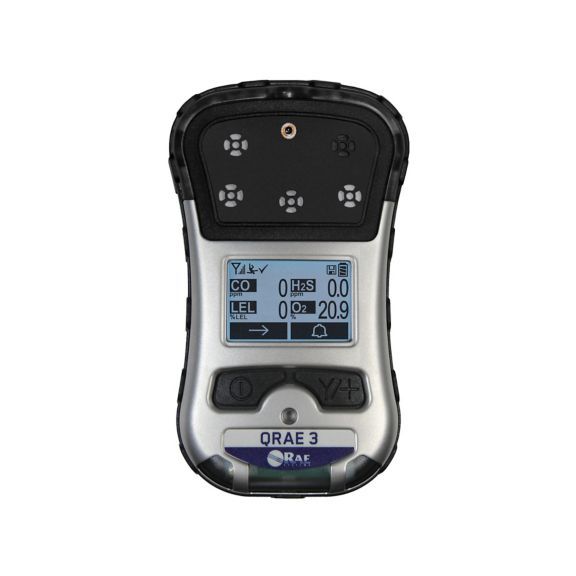
A portable gas leak detector from RAE Systems
2. Fixed Systems
Installed permanently in a location, these systems provide continuous monitoring and are ideal for detecting leaks in areas where gas use is constant and extensive, such as in production areas or around storage tanks.
3. Semi-Portable/Fixed Point Detectors
These are less mobile than handheld units but can be moved and set up in various locations as needed. They strike a balance between fixed and portable systems, offering more robust monitoring without the installation requirements of fully fixed systems.
Choosing the right type of gas leak detector involves balancing these factors to find the most effective solution for your specific circumstances. Whether it’s a portable unit for on-the-go inspections or a comprehensive fixed system for constant monitoring, the right choice will enhance your ability to detect and respond to gas leaks promptly.
How Gas Leak Detectors Work
Understanding how gas leak detectors work can help users effectively employ these devices to prevent potential hazards.
Here’s an overview of the technology and principles behind gas leak detection:
Gas Sensor Types
Gas leak detectors use different types of sensors to identify gas leaks, each suitable for specific gases and applications.
Here are the most common types of gas sensors:
- Electrochemical sensors. These sensors measure the concentration of gas by producing a chemical reaction that generates a current. The current’s strength is proportional to the amount of gas present, making it effective for detecting toxic gases like carbon monoxide.
- Semiconductor sensors. Based on changes in conductivity in a semiconductor material when exposed to a gas, these sensors are commonly used for reactive gases.
- Infrared sensors. These detect specific gas types based on their absorption of infrared light. Infrared sensors are particularly useful for volatile organic compounds and hydrocarbon gases.
- Ultrasonic sensors. They detect the sound of gas leaking from pipes or equipment. This method is highly effective in industrial applications where high-pressure systems are prevalent.
How Gas Detection Sensors Work
Gas detection works basically the same regardless of the type of detector you’re using.
Here are the key steps:
1. Detection
The sensor reacts with the gas (or detects its presence through other means such as sound or light absorption), initiating the detection process.
2. Signal Processing
The initial reaction is converted into an electrical signal that is processed by the detector’s electronic system.
3. Readout
The processed signal is displayed on the detector’s interface, alerting the user to the presence and often the concentration of the gas.
4. Calibration and Maintenance
To ensure accuracy and reliability, gas leak detectors require regular calibration and maintenance. Calibration involves adjusting the detector’s readings to match known gas concentrations, ensuring the device remains accurate over time.
5. Safety Integration
Modern gas leak detectors often integrate with safety systems, providing automated responses such as alarms, system shutoffs, or ventilation activation, enhancing safety protocols in hazardous environments.
Calibration and Maintenance for Gas Leak Detectors
Regular calibration and maintenance are essential to ensure the accuracy and reliability of gas leak detectors. Whether in industrial settings, commercial environments, or homes, these devices play a crucial role in maintaining safety. Failing to calibrate can lead to inaccurate readings, which may result in undetected leaks or false alarms.
Why Calibration Is Important
Calibration adjusts the gas leak detector to ensure it can accurately identify the presence and concentration of gases. Over time, sensors can drift, leading to incorrect readings. By calibrating the detector periodically, you ensure its sensitivity and accuracy, which are critical when detecting harmful or flammable gases.
How to Calibrate a Gas Leak Detector
- Use a calibration gas. Apply a known concentration of gas to the detector to compare the reading with the actual concentration. This helps adjust the detector’s response to ensure accuracy.
- Follow manufacturer guidelines. Each gas leak detector model may have specific calibration instructions. Always refer to the manufacturer’s guidelines for calibration frequency and procedures.
- Perform a bump test. A bump test briefly exposes the detector to a test gas, ensuring it responds correctly and provides a proper reading.
Other Essential Maintenance Tasks
- Sensor replacement. The sensors in gas leak detectors degrade over time. It’s important to replace them periodically according to the manufacturer’s recommendations.
- Battery maintenance. Ensure the batteries are regularly charged or replaced. Failing to do so can result in the device not functioning when needed.
- Regular cleaning. Clean the exterior and any exposed components of the detector to prevent debris from affecting performance. Be cautious not to damage the sensors while cleaning.
- Firmware updates. For digital gas leak detectors, ensure that the firmware is up to date to maintain optimal performance and incorporate the latest safety features.
Recommended Calibration Frequency
How often calibration should be performed depends on the device and its environment. Gas detectors used in harsh or industrial environments typically require more frequent calibration, usually every 3-6 months. For less demanding environments, annual calibration may suffice.
Signs That Calibration or Maintenance is Needed
- The detector fails a bump test or gives inconsistent readings.
- It triggers false alarms or fails to detect gases it previously identified accurately.
- The manufacturer’s recommended calibration interval has been reached.
Proper calibration and regular maintenance are key to the reliable operation of gas leak detectors.
Following these practices ensures that the equipment can effectively detect and alert personnel to gas leaks, enhancing workplace safety and preventing potentially catastrophic events.
Who Uses a Gas Leak Detector?
A person who uses a gas leak detector is often referred to as a gas leak detector operator or simply an inspector.
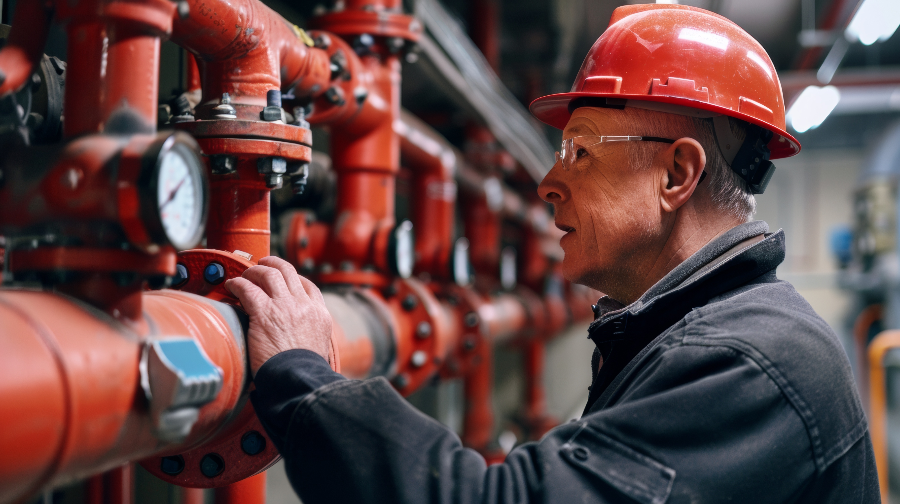
However, the specific title can vary based on the industry and context. Here are a few examples of titles for individuals who might use gas leak detectors:
Safety Inspectors
In industries where safety is a priority, such as oil and gas or manufacturing, inspectors focus on ensuring that facilities comply with safety standards, including monitoring for gas leaks.
Maintenance Technicians
In many facilities, maintenance technicians are responsible for routine checks and maintenance, which include using gas leak detectors to prevent accidents and ensure operational efficiency.
Environmental Technicians
In environmental monitoring and compliance, these technicians use gas leak detectors to ensure that no harmful gases are being released into the environment in violation of regulations.
Pipeline Operator
In the pipeline industry, operators use gas leak detectors to monitor for leaks in pipelines that transport gas and other substances to prevent environmental disasters and ensure the integrity of the pipeline.
HVAC Technicians
In the heating, ventilation, and air conditioning (HVAC) industry, technicians use gas leak detectors to ensure that heating systems, especially those that use gas, are operating safely and efficiently.
Gas Leak Detector FAQ
Gas leak detectors are crucial tools for ensuring safety in environments where gases are used or produced. Here are frequently asked questions about gas leak detectors to provide clarity and help users understand their importance and functionality.
What is a gas leak detector?
A gas leak detector is a device that senses the presence of gases in an area, often as part of a safety system. This type of equipment is used to detect a gas leak and interface with a control system so a process can be automatically shut down.
How do gas leak detectors work?
Gas leak detectors use various types of sensors to identify and measure gases. Common types include electrochemical sensors for detecting toxic gases, infrared sensors for hydrocarbons, ultrasonic sensors for high-pressure gas leaks, and semiconductor sensors for reactive gases.
What types of gas can be detected with a gas leak detector?
Gas leak detectors can detect a variety of gases, including but not limited to methane, propane, carbon monoxide, hydrogen sulfide, and ammonia. The specific gases a detector can identify depend on the sensor types and calibration of the device.
How often should gas leak detectors be calibrated?
Calibration frequencies for gas leak detectors depend on the manufacturer’s recommendations, usage, and the environment where they are used. Generally, it is advisable to calibrate detectors at least annually, or more frequently in harsh environments or after exposure to gases that can desensitize the sensors.
Can a gas leak detector be used to detect leaks from any gas appliance?
While gas leak detectors can detect leaks from many types of gas appliances, it is important to ensure the detector is suitable for the specific type of gas used by the appliance. Always check the detector’s specifications to ensure compatibility with the gas type.
What are the best practices for using a gas leak detector?
Best practices for using a gas leak detector include testing the device regularly, ensuring it is properly calibrated, using the detector according to the manufacturer’s instructions, and performing routine maintenance. It’s also crucial to train personnel on how to respond to the alarms generated by the detector.
Where should a gas leak detector be installed?
Gas leak detectors should be installed near potential leak sources, such as gas pipelines, valves, and appliances. They should also be placed in areas where gas accumulation could occur, such as low points for heavier-than-air gases and high points for lighter-than-air gases.
Can gas leak detectors detect leaks outdoors?
Yes, some gas leak detectors are designed for outdoor use and can detect gas leaks in environments such as pipelines, oil rigs, and storage tanks. Outdoor detectors are typically more robust and designed to withstand environmental factors like weather and temperature variations.