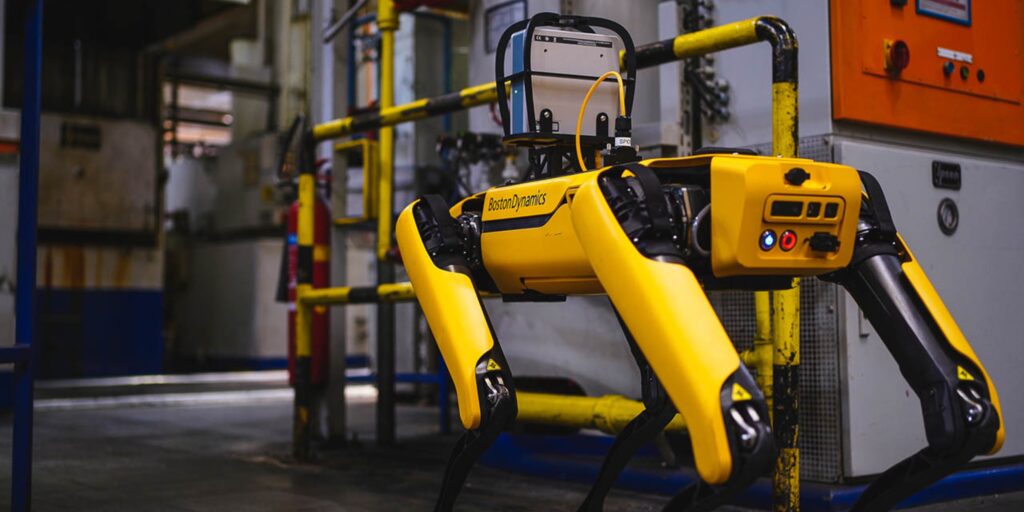
Guide
What Is Acoustic Imaging? Best Acoustic Imaging Cameras and More
Acoustic imaging is a non-destructive testing method that uses sound waves to detect and visualize structural defects, leaks, or mechanical anomalies in industrial systems.
→ Jump to acoustic imaging cameras for sale and rent.
Alternate names for acoustic imaging include:
- Ultrasonic imaging
- Sound imaging
- Acoustic holography
- Sonic visualization
Acoustic imaging works by capturing sound waves generated by a device or naturally occurring processes. Acoustic imaging is one type of acoustic leak detection—others include ultrasonic leak detection and acoustic emission testing.
These sound waves are converted into visual data by an acoustic imaging camera, allowing inspectors to identify issues such as leaks, friction, or mechanical failures that are invisible to the naked eye.
Compared to other inspection methods, acoustic imaging offers advantages like the ability to detect defects in complex environments, work in noisy or harsh conditions, and perform inspections from a safe distance. This makes it indispensable for applications like pipeline inspections, machinery maintenance, and equipment monitoring across various industries.
In this guide to acoustic imaging we’ll share the top acoustic imaging cameras for sale, what acoustic imaging is and how it works, and a lot more.
Best Acoustic Cameras for Sale and Rent [New for 2024]
Want to buy or rent an acoustic camera? Here are the top options on the market.
1. Fluke SV600 Acoustic Imager
The Fluke SV600 Acoustic Imager is an advanced device designed for real-time, continuous sound imaging in industrial environments.
The SV600 utilizes sophisticated acoustic technology to detect sound anomalies like leaks or mechanical failures, making it ideal for monitoring large, noisy spaces. Its ability to pinpoint issues quickly helps reduce downtime and improve maintenance efficiency.
- Detection range. Covers wide areas for real-time monitoring
- Key features. Continuous imaging, high-resolution sound mapping, quick identification of anomalies
- Applications. Industrial leak detection, mechanical monitoring, and predictive maintenance
- Display. High-definition display with intuitive interface
Learn more about the Fluke SV600 Acoustic Imager.
Crysound 2623 – Acoustic Imager
The Crysound 2623 Acoustic Imager is a high-performance device designed to detect and visualize sound waves, offering real-time identification of mechanical faults and leaks in industrial environments.
The 2623 uses advanced acoustic imaging technology to capture sound data, ideal for applications that require precise, non-invasive monitoring of equipment.
- Detection range. Wide-area coverage for detailed sound detection
- Key features. High-resolution acoustic mapping, real-time anomaly detection, and portable design
- Applications. Leak detection, mechanical fault monitoring, and industrial inspections
- Display. High-definition display with intuitive controls
Learn more about the Crysound 2623 Acoustic Imager.
Crysound 8124 Handheld Acoustic Imager
Crysound 8124 Handheld Acoustic Imager
The Crysound 8124 Handheld Acoustic Imager is a portable and versatile device designed for detecting and visualizing sound sources in real-time.
The 8124 uses advanced acoustic imaging technology to capture sound data, making it ideal for identifying leaks, mechanical faults, and other issues in industrial environments. Its lightweight design and intuitive interface allow for efficient inspections in various settings.
- Detection range. Suitable for pinpointing sound sources in complex environments
- Key features. Real-time sound visualization, portable design, user-friendly interface
- Applications. Leak detection, machinery diagnostics, industrial inspections
- Display. High-definition display with intuitive controls
Learn more about the Crysound 8124 Handheld Acoustic Imager.
How Acoustic Imaging Works
Acoustic imaging converts sound waves into visual images, allowing inspectors to detect anomalies such as leaks, cracks, or friction in industrial systems.
This method relies on the use of an acoustic imager, which captures sound waves and processes them into visual data for analysis.
Keep reading for a breakdown of how acoustic imaging technology works.
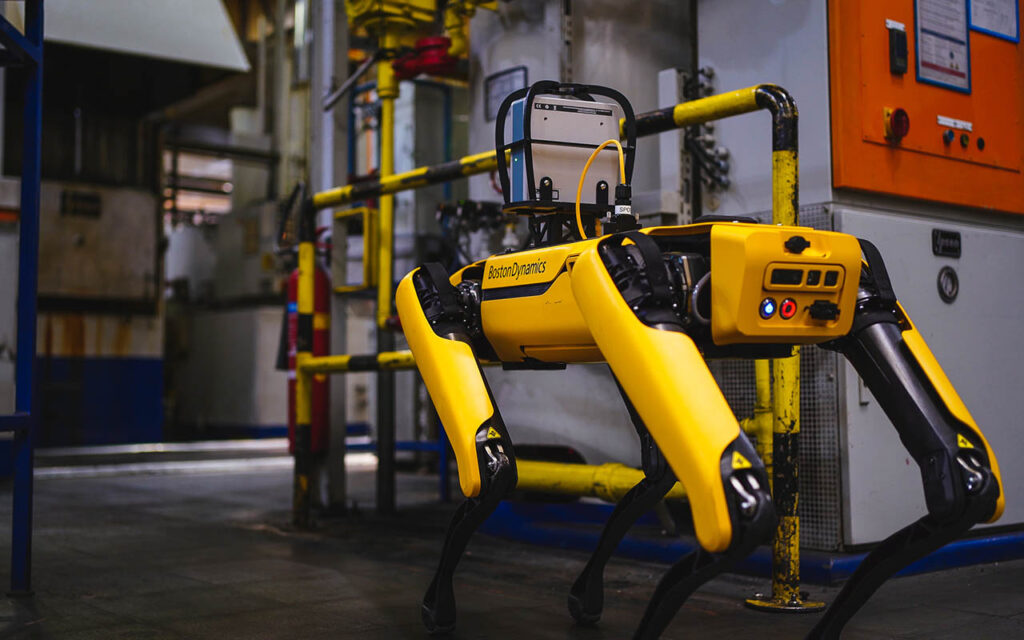
Principles of Sound Wave Detection
Acoustic imaging is based on the principle that different materials and mechanical conditions emit unique sound waves.
When there’s a defect, such as a gas leak or mechanical issue, that defect produces sound at specific frequencies—frequencies that make it stand out.
An acoustic inspection camera can detect these sound waves, even if they are outside the range of human hearing, and help inspectors capture them for further analysis.
Capturing Sound with an Acoustic Imager
An acoustic imager uses an array of microphones or sensors to pick up sound waves from the surrounding environment.
The number of microphones and the precision of the device determine the sensitivity and accuracy of detection. The best acoustic imaging cameras can pinpoint the source of a sound with remarkable accuracy, making them invaluable for industrial inspections.
Converting Sound into Visual Data
Once the sound waves are detected, the acoustic imaging camera converts them into visual data.
The device processes these signals and creates a visual representation, often a color-coded image, that highlights the location and intensity of the sound. This visual data allows inspectors to easily identify areas of concern and assess the severity of any detected issues.
By capturing and converting sound data, acoustic imaging provides a non-invasive way to diagnose mechanical issues and improve maintenance efficiency.
The Difference Between Acoustic Imaging and Acoustic Emission Testing
Acoustic imaging and acoustic emission testing are related techniques that both involve the use of sound waves, but they aren’t the same.
Acoustic imaging uses ultrasound to produce real-time visual representations of sound. It actively generates sound waves and converts them into images, allowing us to “see” sounds that are typically undetectable to human ears1.
This technique is often used for:
- Detecting and visualizing air or gas leaks
- Pinpointing sources of sound in industrial environments
- Creating visual maps of sound patterns
Acoustic emission testing, on the other hand, is a passive technique that “listens” for energy released by materials under stress. It detects and analyzes high-frequency acoustic waves emitted when a material undergoes deformation or damage.
Key aspects of acoustic emission testing include:
- Monitoring structures during operation to detect active defects
- Early detection of cracks, fractures, or other discontinuities
- Real-time assessment of structural integrity
Key Differences Between Acoustic Imaging and Acoustic Emission Testing
- Active vs. passive. Acoustic imaging actively generates sound waves, while acoustic emission testing passively listens for emissions from the material itself.
- Visualization. Acoustic imaging produces visual representations of sound, whereas acoustic emission testing typically analyzes waveforms and data without creating images.
- Applications. Acoustic imaging is often used for leak detection and sound source localization, while acoustic emission testing is primarily used for structural health monitoring and defect detection in materials under stress.
Industries That Use Acoustic Imaging
Acoustic imaging has become a critical tool in industries such as oil and gas, power generation, and manufacturing.
An acoustic imager can detect a range of issues that are hard to identify through traditional inspection methods, such as gas leaks, mechanical failures, and blockages.
Below are the top industries that use acoustic imaging, with use cases listed for each one.
1. Oil and Gas Industry
The oil and gas industry frequently uses acoustic imaging to detect gas leaks in pipelines and storage facilities. Since the industry handles highly flammable gases like methane and propane, early detection is critical for preventing hazardous incidents.
Oil and Gas Industry Use Cases
- Detecting gas leaks in pipelines to prevent explosions
- Monitoring storage tanks for pressure and leak issues
- Inspecting offshore drilling equipment for mechanical faults
- Assessing valves and connections for potential leaks
2. Power Generation Industry
In power plants, acoustic imaging is used to monitor turbines, boilers, and heat exchangers for leaks or mechanical failures. Early detection of sound anomalies helps maintain operational efficiency and safety.
Power Generation Industry Use Cases
- Identifying steam leaks in high-pressure boilers
- Monitoring turbines for unusual vibrations or sounds
- Detecting gas leaks in heat exchangers
- Assessing cooling systems for abnormal noises
3. Manufacturing Industry
The manufacturing sector uses acoustic imaging to detect air leaks in pneumatic systems and identify mechanical issues in machinery. These systems help ensure product quality and prevent costly downtime.
Manufacturing Industry Use Cases
- Locating air leaks in compressed air systems
- Identifying mechanical faults in production equipment
- Monitoring conveyor systems for unusual sounds
- Inspecting bearings and gears for early signs of wear
4. Aerospace Industry
In aerospace, acoustic imaging is vital for monitoring aircraft components such as engines and turbines. Detecting abnormal vibrations and leaks helps ensure the safety and reliability of the aircraft.
Aerospace Industry Use Cases
- Monitoring jet engines for abnormal vibrations
- Detecting airframe leaks during routine inspections
- Assessing landing gear for mechanical issues
- Inspecting fuel lines for potential leaks
5. Automotive Industry
The automotive industry uses acoustic imaging to detect leaks in air conditioning systems, exhaust pipes, and brake lines. It also helps identify mechanical issues in engines and transmissions.
Automotive Industry Use Cases
- Detecting exhaust leaks in vehicle systems
- Inspecting air conditioning systems for refrigerant leaks
- Identifying mechanical issues in engine components
- Monitoring brake lines for potential fluid leaks
6. Chemical Processing Industry
In the chemical processing industry, acoustic imaging is used to detect leaks in pressurized vessels, piping systems, and valves. This helps prevent hazardous chemical spills and ensures safety in plant operations.
Chemical Processing Industry Use Cases
- Identifying gas leaks in chemical storage tanks
- Monitoring piping systems for pressure-related issues
- Detecting leaks in safety valves and pressure relief systems
- Inspecting reactors for abnormal sound patterns
7. Food and Beverage Industry
The food and beverage industry uses acoustic imaging to detect leaks in pressurized systems, such as carbonation tanks and bottling lines. This ensures product quality and minimizes waste.
Food and Beverage Industry Use Cases
- Inspecting bottling lines for carbonation leaks
- Monitoring refrigeration systems for gas leaks
- Detecting air leaks in packaging equipment
- Assessing pasteurization equipment for steam leaks
8. Pharmaceutical Industry
In the pharmaceutical industry, acoustic imaging is employed to detect leaks in cleanroom environments, compressed air systems, and sterilization equipment, helping maintain product quality and safety.
Pharmaceutical Industry Use Cases
- Detecting leaks in cleanroom air filtration systems
- Monitoring sterilization equipment for pressure-related issues
- Inspecting compressed air lines for leaks
- Identifying leaks in liquid filling machines
Acoustic Imaging vs. Other Inspection Methods
Acoustic imaging offers distinct advantages over other non-destructive testing (NDT) methods like infrared thermography and ultrasonic testing.
One of the primary benefits of an acoustic camera is its ability to detect sound emissions from leaks, mechanical wear, or friction in environments where visual inspections may be insufficient.
Comparison with Infrared Thermography
While infrared thermography detects temperature variations, it may struggle in detecting gas leaks or mechanical issues that don’t produce significant heat.
An acoustic imaging camera can identify sound waves emitted from leaks or friction in real-time, making it better suited for environments where temperature data is less useful.
Comparison with Ultrasonic Testing
Ultrasonic testing relies on sending sound waves into materials and analyzing the echoes to detect internal defects.
However, it often requires physical contact with the surface being tested. In contrast, the best acoustic imaging cameras can detect sound from a distance, making them more versatile for real-time, non-contact inspections of pipelines, machinery, and other equipment.
Where Acoustic Imaging Excels
Acoustic imaging excels in detecting gas leaks, mechanical wear, and issues in high-noise or high-pressure environments where other methods may fail.
By using an acoustic imager, inspectors can locate problems quickly without interrupting operations, making it an invaluable tool for industries like oil and gas, power generation, and manufacturing.
How to Choose the Right Acoustic Imager
Looking for an acoustic imager?
Here are the four key factors to consider in making your decision.
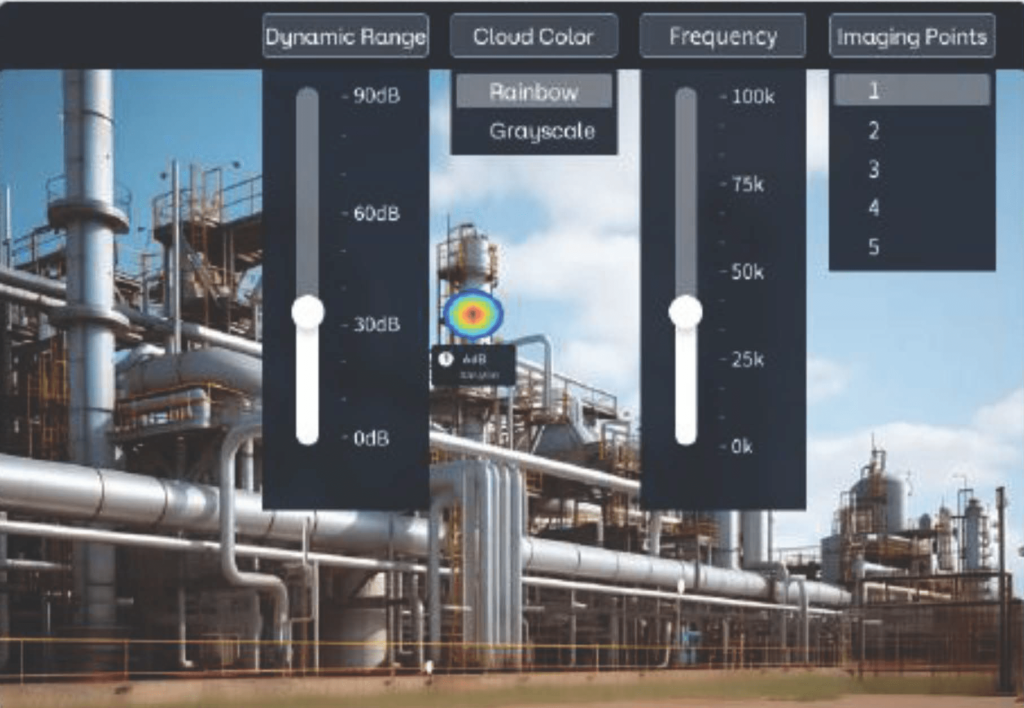
1. Detection Range
The detection range for your acoustic imager is crucial, particularly if you’re inspecting large or hard-to-reach areas.
The best acoustic imaging cameras offer a wide range, allowing you to detect issues from a distance, such as gas leaks or mechanical wear in high-pressure systems.
2. Resolution
High-resolution imaging ensures that the acoustic camera delivers clear and precise visuals, which is essential for detecting small defects. Look for models that provide detailed images to accurately assess potential issues.
3. Durability
Durability is important for industrial environments.
An acoustic imaging camera should withstand harsh conditions, such as extreme temperatures, dust, and vibration, ensuring long-term reliability in demanding settings.
4. Ease of Use
Consider the ease of operation when choosing an acoustic imager. A user-friendly interface, intuitive controls, and portability will improve efficiency, especially in fieldwork where quick diagnostics are needed.
Acoustic Imaging FAQ
Here are some of the most commonly asked questions about acoustic imaging.
What is an acoustic imager?
An acoustic imager is a device that captures sound waves emitted by mechanical components, leaks, or structural flaws and converts them into visual data for inspection purposes.
How does an acoustic imaging camera work?
An acoustic imaging camera detects sound waves, typically outside the range of human hearing, and processes these signals into visual images, often displayed on a screen, allowing inspectors to pinpoint the source of anomalies like leaks or friction.
What are the advantages of acoustic imaging?
Acoustic imaging is a non-invasive method that allows real-time detection of mechanical issues, gas leaks, or defects without interrupting operations. Its ability to function in noisy or complex environments makes it superior to other inspection methods in specific scenarios.
What industries use acoustic imaging?
Acoustic imaging is widely used in industries such as oil and gas, power generation, manufacturing, and aerospace for detecting leaks, monitoring equipment health, and ensuring safety in critical systems.
What is an acoustic camera?
An acoustic camera is a specialized device that visualizes sound waves, converting them into images to help identify issues like leaks, friction, or material stress in mechanical systems. It is commonly used for industrial inspections in high-risk environments.
Can acoustic imaging detect leaks that are inaudible to humans?
Yes, acoustic imaging can detect leaks that are outside the range of human hearing. It captures ultrasonic frequencies and converts them into visual data, enabling inspectors to identify leaks that would otherwise go undetected.
How accurate is acoustic imaging for industrial inspections?
Acoustic imaging is highly accurate for detecting leaks and mechanical faults in complex systems. The accuracy depends on factors like the resolution of the acoustic camera, the distance from the sound source, and environmental noise levels.
Is acoustic imaging useful in noisy environments?
Yes, acoustic imaging is effective in noisy environments because it focuses on specific sound frequencies and can filter out background noise. This capability allows inspectors to isolate the sound sources related to leaks or mechanical issues.
What are some limitations of acoustic imaging?
While acoustic imaging is highly effective, it can have limitations such as reduced accuracy in extremely loud environments, difficulty detecting very small leaks, and the need for specialized training to interpret the images accurately.
What maintenance is required for an acoustic camera?
Maintaining an acoustic camera typically involves regular calibration, cleaning the sensors, updating software, and ensuring the device’s battery is in good condition. Proper maintenance ensures the device remains accurate and reliable for inspections.