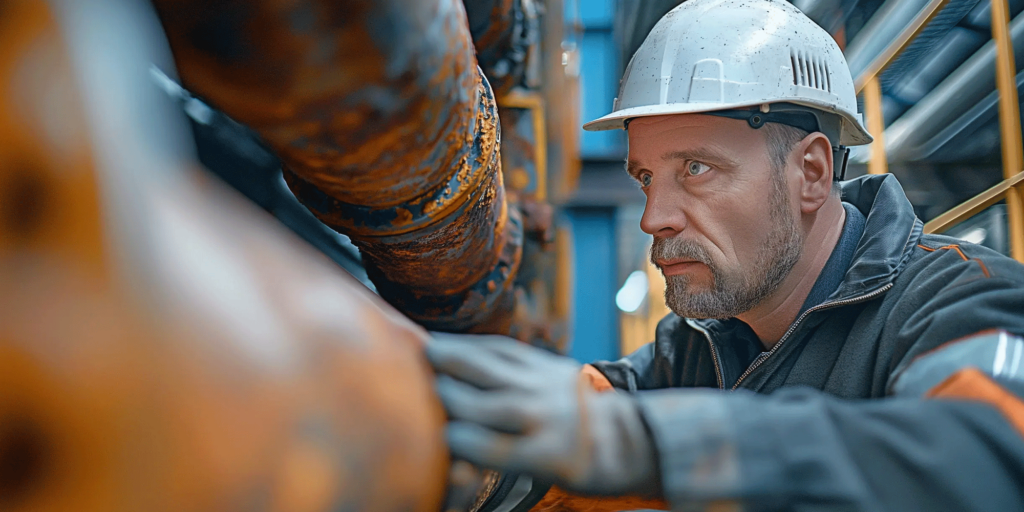
Guide
Visual Inspection: An In-Depth Guide [New for 2024]
Visual inspection is a fundamental NDT method that involves using the naked eye or visual aids to examine materials, components, or systems for any defects or irregularities.
Visual inspections are one of the most commonly used inspection methods across all industries throughout the world. The appeal of visual inspections is that they’re simple, cost-effective, and they can quickly identify issues that could compromise the integrity of critical assets.
Although visual inspections are simple and can be done with either the naked eye or specialized tools, like inspection cameras or drones, they do require specialized training.
Alternate phrases for VI include:
- Visual testing (VT)
- Visual control (VC)
- Visual analysis (VA)
Visual inspections are particularly effective for identifying and evaluating defects during inspections, including:
- Visible defects like cracks, dents, scratches, corrosion, or discoloration
- Anomalies
- Inconsistencies on the surface of objects
Every sector that does inspections uses visual inspection, including industries as diverse as construction, oil and gas, and aerospace (we cover top applications for visual inspections below).
This comprehensive guide delves into the world of visual inspection, exploring its techniques, tools, and diverse applications. We’ll also cover best practices for conducting effective visual inspections and highlight advanced technologies enhancing this traditional method.
Have a specific topic in mind? Use the menu to the right to jump around within this guide.
What Is a Visual Inspection?
Visual inspection is the process of conducting an inspection by sight. It can be done with:
- The unaided, naked eye
- Simple visual aids like magnifying glasses, rope, and mirrors
- Sophisticated visual aids like progressional-grade cameras, drones and boroscopes
Visual inspection is one of the oldest and most widely used methods of non-destructive testing. Although simple in its approach, they’re still one of the most effective techniques inspectors can employ.
Principles of Visual Inspection
The fundamental principle of visual inspection is based on the detection of surface anomalies through direct observation.
Here are the key steps involved in visual inspection:
1. Surface Preparation
Inspectors clean the surface of the material or asset they’re going to inspect to remove any contaminants such as dirt, grease, or paint that could obscure defects.
2. Lighting Review/Set Up (As Needed)
Inspectors review the lighting to make sure the surface is well-illuminated, allowing for the clear visibility of any defects. Lighting for visual inspections may include the use of natural light, artificial light sources, or specialized lighting equipment such as UV lamps for fluorescent inspections.
3. Observation
The inspector examines the surface for any signs of defects, such as cracks, dents, scratches, corrosion, or discoloration. As we’ve covered, this can be done with the naked eye or with the aid of optical instruments to enhance visibility and detail.
4. Documentation
The inspector documents any defects identified during the inspection, including their location, size, and nature. Then they or members of the maintenance team use this information to assess the severity of the defects and determine necessary corrective actions, as needed based on the findings of the inspection.
Advantages of Visual Inspection
- Simplicity. Visual inspection is straightforward and easy to perform, requiring minimal equipment and setup. It can be quickly deployed in various settings, making it a convenient choice for many applications.
- Cost-effective. Since visual inspection relies primarily on the human eye and basic optical tools, it is one of the most cost-effective NDT methods available.
- Immediate results. Defects and anomalies can be identified and documented in real-time, allowing for prompt decision-making and corrective actions.
- Versatility. Visual inspection can be applied to a wide range of materials, components, and assets, making it a versatile method for ensuring quality and safety.
Limitations of Visual Inspection
- Surface-only detection. Visual inspection is limited to detecting surface defects and can’t identify subsurface or internal flaws that may be present in the material.
- Subjectivity. The effectiveness of visual inspection can be influenced by the inspector’s experience, skill, and judgment. Inconsistent results can occur due to human factors.
- Limited sensitivity. Small or subtle defects may be difficult to detect without the aid of magnification or enhanced lighting, potentially leading to missed defects.
- Environmental conditions. The accuracy of visual inspection can be affected by environmental conditions such as poor lighting, glare, or obstructed views.
The Three Types of Visual Inspections
There are three types of visual inspection—direct, which is the most common; remote, which is enabled by ground-based robots and drones; and automated, which is computer-aided testing, measurement and analysis.
Keep reading to learn more about each type of inspection.
1. Direct Visual Inspection (DVI)
Direct visual inspection involves an inspector physically observing the object with their eyes or using basic tools to enhance their view. The simplicity and immediacy of direct visual inspection make it a cost-effective and essential method for initial evaluations and routine checks.
Common tools used in direct visual inspection include magnifying glasses, mirrors, flashlights, and measuring devices.
Examples:
- In the construction industry, inspectors might use a magnifying glass to closely examine welds for cracks or imperfections.
- In manufacturing, direct visual inspection is often employed on assembly lines to check for surface defects or improper assembly of parts.
2. Remote Visual Inspection (RVI)
Remote visual inspection (RVI) uses devices like crawlers, drones, borescopes,or endoscopes to collect visual data remotely in areas that are difficult or dangerous to access, like the inside of an industrial boiler or a narrow pipe.
RVI allows for detailed examination while ensuring the safety of inspectors, making it a critical method for maintaining the integrity of hard-to-reach components.
RVI is particularly useful in inspecting confined spaces, hazardous environments, and complex structures.
Examples:
- In the aerospace industry, borescopes are used to inspect the internal components of engines without disassembly.
- In the oil and gas industry, drones equipped with high-resolution cameras are employed to inspect pipelines and offshore platforms.
3. Automated Visual Inspection (AVI)
Automated visual inspection employs advanced technologies such as machine vision systems, AI, and robotics to carry out inspections with high precision and efficiency.
These systems use cameras and sensors to capture images and data, which are then analyzed by software to detect defects, measure dimensions, and ensure compliance with specifications.
The main benefits of automated visual inspection include increasing speed and accuracy, reducing human error, and allowing for real-time quality control in high-volume production environments.
Examples:
- In the automotive industry, automated visual inspection systems are used on assembly lines to check for defects in car body panels, ensuring uniform quality.
- In electronics manufacturing, these systems inspect printed circuit boards (PCBs) for soldering errors and component placement accuracy.
Visual Inspection Tools
There are several different types of tools that inspectors use to support their work in visual inspections.
To organize all these tools, we’ve arranged them into four different categories. Keep reading to see all the tools.
- Manual Tools—Direct Visual Inspection Tools
- Cameras, Imaging Devices & Optical Instruments—Direct Visual Inspection Tools
- Robotics—Remote Visual Inspection Tools
- Automated Systems—Automated Inspection Tools
1. Manual Tools—Direct Visual Inspection Tools
I. Magnifying Glasses
- How they work. By enlarging the image of the object being inspected, magnifying glasses allow inspectors to see fine details and small defects that might not be visible to the naked eye.
- Applications. Commonly used in the manufacturing and electronics industries to examine small components and assemblies.
II. Mirrors
- How they work. Placed at an angle, mirrors allow inspectors to see around corners and into confined spaces.
- Applications. Widely used in the automotive and aerospace industries for inspecting hard-to-reach areas, such as engine components and undercarriages.
III. Flashlights
- How they work. Flashlights provide additional light to enhance visibility, especially in dark or poorly lit environments.
- Applications. Essential for all types of inspections, particularly in construction and industrial settings.
IV. Handheld UV lights—ultraviolet lights used to detect fluorescent dyes or markers.
- How they work. When used with fluorescent penetrants or magnetic particles, UV lights cause these substances to glow, revealing cracks and other surface defects.
- Applications. Widely used in non-destructive testing (NDT) methods such as dye penetrant and magnetic particle inspections.
2. Cameras, Imaging Devices & Optical Instruments—Direct Visual Inspection Tools
I. Digital cameras—high-resolution cameras used to capture detailed images and videos.
- How they work. Cameras can be handheld or mounted on tripods, capturing images that can be analyzed on-site or off-site.
- Applications. Used across various industries to document inspection findings and for further analysis.
II. Thermal imaging cameras—cameras that detect infrared radiation and produce thermal images.
- How they work. These cameras visualize temperature differences, highlighting areas of heat loss, insulation failure, or overheating components.
- Applications. Used in building inspections, electrical inspections, and predictive maintenance.
III. Borescopes and endoscopes—flexible or rigid tubes with an optical system and a light source.
- How they work. Borescopes and endoscopes are inserted into narrow or hard-to-reach spaces, providing a live feed of the internal view on a display monitor.
- Applications. Extensively used in aerospace for engine inspections, and in the oil and gas industry for pipeline inspections.
IV. Microscopes—optical instruments that provide high magnification of small objects.
- How they work. Microscopes use lenses to magnify small details, often beyond the capability of magnifying glasses.
- Applications. Common in the electronics and medical device industries for inspecting micro-components and materials.
3. Robotics & Drones—Remote Visual Inspection Tools
I. Drones—flying robotics solutions equipped with high-resolution cameras (also called UAVs/uncrewed aerial vehicles).
- How they work. Drones fly over large areas, capturing detailed images and videos from various angles.
- Applications. Essential for inspecting large structures like bridges, wind turbines, and offshore platforms.
II. Robotic crawlers—robots made to navigate pipes, walls, or tanks to collect visual inspection data or other types of inspection data.
- How they work. Crawler robots can enter narrow pipes, climb walls, or traverse tanks, allowing inspectors to collect data remotely without the need to enter dangerous confined spaces.
- Applications. Robotic crawlers are used across a range of industries where collecting inspection data remotely is called for, including infrastructure, power generation, and maritime operations.
III. Walking “dog” robots—Robots like the Boston Dynamics Spot that can collect inspection data remotely.
- How they work. Similar to a crawler robot, a “dog” robot collects inspection data remotely but can move more quickly and nimbly than a crawler, which is usually limited to one plane of motion.
- Applications. Robotic dogs are being used in several scenarios that call for RVI, including power generation, oil and gas, and environmental monitoring.
4. Automated Systems—Automated Visual Inspection Tools
I. Automated optical inspection (AOI) systems—computerized systems that use cameras and software algorithms to inspect parts and assemblies.
- How they work. AOI systems capture images and analyze them for defects using predefined criteria, often in real-time.
- Applications. Widely used in electronics manufacturing for inspecting printed circuit boards (PCBs) and other small components.
When Is Visual Inspection Required?
Visual inspection is especially useful in situations where quick, cost-effective, and straightforward assessment is necessary—here are the top scenarios that call for visual inspections.
1. Initial Quality Control
Visual inspection is essential during the initial stages of manufacturing and production to verify the quality of raw materials and finished products. It helps inspectors to identify surface defects, dimensional inaccuracies, and workmanship issues early in the process.
Application examples:
- Inspecting raw materials such as metals, plastics, and composites for surface flaws.
- Checking the assembly and fit of components in automotive and aerospace manufacturing.
- Ensuring the quality of consumer goods before packaging and distribution.
2. Routine Maintenance and In-Service Inspections
Regular visual inspections are critical for maintaining the safety and functionality of equipment and structures. These inspections help in detecting wear, corrosion, and other forms of degradation that could lead to failure.
Application examples:
- Monitoring the condition of pipelines, storage tanks, and pressure vessels in the oil and gas industry.
- Inspecting structural components of bridges, buildings, and other infrastructures for signs of damage or deterioration.
- Checking aircraft and automotive components for wear, cracks, and other defects during scheduled maintenance.
3. Pre- and Post-Operation Checks
Visual inspection is often required before and after operations to ensure that equipment and systems are in good working condition and to verify that no damage has occurred during use.
Application examples:
- Inspecting heavy machinery and equipment before and after operation in construction and mining.
- Checking industrial machinery and systems before startup and after shutdown to detect any potential issues.
- Conducting pre-flight and post-flight inspections of aircraft to ensure safety.
4. Regulatory Compliance and Safety Audits
Visual inspections are mandated by various industry standards and regulations to ensure compliance and maintain safety. These inspections are often part of regular audits and certification processes.
Application examples:
- Ensuring compliance with safety standards and regulations in the manufacturing, construction, and transportation industries.
- Conducting safety audits of industrial facilities and workplaces to identify hazards and ensure a safe working environment.
- Verifying the condition and safety of pressure vessels, boilers, and other critical equipment in accordance with regulatory requirements.
5. Failure Analysis and Investigations
When a component or system fails, visual inspection is the first step in the failure analysis process. It can help inspectors to find the root cause of the failure by examining surface conditions and collecting evidence.
Application examples:
- Investigating the cause of structural failures in buildings, bridges, and other infrastructures.
- Analyzing failed components in the aerospace and automotive industries to identify manufacturing or material defects.
- Examining industrial equipment and machinery after failure to determine the cause and prevent future occurrences.
Visual Inspection Applications by Industry
The Top 7 Industries that Rely on Visual Inspections + Specific Applications They Use
As we’ve covered, visual inspection is one of—if not the most—fundamental NDT methods used in a myriad of industries.
But which industries rely on it the most? And how specifically do they use it?
Here are the top seven industries that use visual inspection, with specific applications covered for each one.
1. Oil and Gas
The oil and gas industry uses visual inspection to maintain the integrity of critical infrastructure and ensure safe operations.
- Pipeline inspections. Inspectors examine pipelines visually for signs of corrosion, leaks, and mechanical damage. Remote visual inspection tools, such as drones and robotic crawlers, often help inspectors access hard-to-reach areas for remote visual data collection.
- Equipment monitoring. Inspectors conduct visual inspections on equipment such as storage tanks, pressure vessels, and drilling rigs to detect signs of wear, corrosion, and other defects that could lead to failures and environmental hazards.
- Offshore platforms. In offshore oil and gas operations, visual inspections are essential for monitoring the condition of platforms and subsea structures. This includes inspecting welds, joints, and support structures for signs of fatigue and damage caused by harsh marine environments.
2. Power Generation
In the power generation industry, visual inspection is crucial for maintaining the reliability and efficiency of power plants and related infrastructure.
- Turbine inspections. Inspectors examine turbine blades and other critical components for signs of wear, cracks, and other defects. Early detection of such issues can prevent catastrophic failures and costly downtime.
- Boiler and pressure vessel inspections. Inspectors perform regular visual inspections on boilers and pressure vessels to identify signs of corrosion, scaling, and other issues that could impact their performance and safety.
- Transmission lines. Inspectors carry out visual inspections on transmission lines and towers to detect damage caused by weather, wear, and other factors. These inspections help maintain the integrity of the power distribution network and prevent outages.
3. Pharmaceutical and Food Industries
In industries like food and pharmaceuticals in which hygiene and safety are paramount, visual inspections play a key role in ensuring compliance with strict standards.
- Cleanroom inspections. In pharmaceutical manufacturing, visual inspections are conducted in cleanrooms to ensure that surfaces and equipment are free of contaminants. Doing this helps in maintaining the sterility of the production environment.
- Packaging inspections. In both pharmaceutical and food industries, visual inspections of packaging helps ensure products are correctly sealed and labeled, preventing contamination and ensuring compliance with regulations.
- Facility inspections. Regular visual inspections of facilities help in identifying potential sources of contamination, such as damaged surfaces, pest infestations, and hygiene issues. This proactive approach is essential for maintaining product safety and quality.
4. Manufacturing
In the manufacturing industry, visual inspection is integral to maintaining product quality and consistency. It’s used at various stages of the production process to ensure that components and finished products meet stringent standards.
- Quality control. Inspectors examine parts and products for surface defects such as cracks, scratches, and other imperfections. This helps in identifying defective items before they proceed to the next stage of production or reach the customer.
- Assembly line monitoring. Continuous visual inspection is employed to ensure that assembly lines operate smoothly, with components correctly positioned and assembled. Automated visual inspection systems are often used to enhance efficiency and accuracy in high-volume production environments.
- Compliance with standards. Manufacturers use visual inspection to verify that products comply with industry standards and regulations, reducing the risk of recalls and ensuring customer satisfaction.
5. Aerospace
The aerospace industry relies heavily on visual inspection to maintain the safety and reliability of aircraft. Given the high stakes involved, inspectors conduct these visual inspections meticulously and regularly.
- Aircraft maintenance. Visual inspections are part of routine maintenance checks to identify signs of wear, corrosion, and damage on aircraft surfaces, including the fuselage, wings, and engine components. These inspections help prevent potential failures that could lead to accidents.
- Pre-flight and post-flight checks. Pilots and ground crew conduct visual inspections before and after each flight to ensure that no damage or foreign objects are present. These quick checks are crucial for the immediate safety of the flight.
- Non-destructive testing (NDT) integration. Visual inspection often complements other NDT methods in the aerospace industry, providing a preliminary assessment before more advanced testing is conducted.
6. Construction
In the construction sector, visual inspection ensures the structural integrity and safety of buildings and infrastructure projects.
- Structural inspections. Inspectors examine structural elements such as beams, columns, and joints for signs of stress, cracking, and other damage. This helps in identifying issues that could compromise the stability of the structure.
- Quality assurance. During and after construction, visual inspections are conducted to ensure that materials and workmanship meet design specifications and building codes. This includes checking the alignment, fit, and finish of various components.
- Safety inspections. Regular visual inspections are conducted on construction sites to identify potential safety hazards, such as faulty scaffolding, exposed wiring, and inadequate protective measures. This proactive approach helps prevent accidents and ensure a safe working environment.
7. Automotive
The automotive industry uses visual inspection at various stages of the vehicle manufacturing and maintenance process to ensure safety and quality.
- Assembly line inspections. Automated visual inspection systems are used to check components and assemblies on the production line for defects such as misalignment, surface flaws, and missing parts. Doing this ensures that vehicles meet quality standards before they leave the factory.
- Maintenance and repair. During routine maintenance and repair work, mechanics perform visual inspections to identify issues such as fluid leaks, worn-out components, and other potential problems. This helps in maintaining the vehicle’s performance and safety.
- Pre-delivery inspections. Before delivering vehicles to customers, dealerships conduct thorough visual inspections to ensure that the vehicles are free of defects and meet the expected quality standards.
Best Practices for Effective Visual Inspection
Visual inspection, while straightforward, requires careful adherence to best practices to ensure accuracy, consistency, and reliability.
Here are key practices to enhance the effectiveness of your visual inspections:
1. Proper Training and Certification
- Qualified personnel. Ensure that visual inspections are conducted by trained and certified inspectors. Certification from recognized bodies such as the American Society for Nondestructive Testing (ASNT) or equivalent organizations is essential.
- Continuous education. Encourage ongoing education and training to keep inspectors updated on the latest techniques, equipment, and industry standards. This can include workshops, seminars, and certification renewal courses.
2. Appropriate Equipment Selection
- Inspection tools. Use appropriate tools such as magnifying glasses, borescopes, and mirrors to enhance the visual inspection process. High-quality tools improve the ability to detect small or hidden defects.
- Lighting. Ensure adequate lighting in the inspection area. Use portable or fixed lighting sources to illuminate hard-to-see areas, enhancing the visibility of defects.
- Documentation tools. Use cameras and video recording equipment to document inspection findings. Digital records help in tracking defects over time and facilitate communication between inspectors and stakeholders.
3. Surface Preparation
- Clean surfaces. Ensure that the surfaces being inspected are clean and free from contaminants such as dirt, grease, and paint. Contaminants can obscure defects and affect the accuracy of the inspection.
- Smooth surfaces. Smooth out rough or uneven surfaces as much as possible to improve the visibility of defects. Use appropriate cleaning and preparation techniques to achieve the best results.
4. Inspection Procedures
- Standard operating procedures (SOPs). Develop and adhere to detailed SOPs for each type of visual inspection. SOPs ensure consistency, thoroughness, and compliance with regulatory requirements.
- Systematic coverage. Follow a systematic approach to cover the entire inspection area. Divide large areas into manageable sections and inspect each section thoroughly to ensure comprehensive coverage.
- Proper documentation. Record all findings accurately and systematically. Use standardized forms and digital tools to document defects, including their location, size, and severity.
5. Data Analysis and Interpretation
- Expert interpretation. Ensure that inspection data is interpreted by experienced professionals who can accurately assess the significance of defects. Proper interpretation is crucial for making informed decisions based on inspection results.
- Comparative analysis. Compare current inspection data with historical records to identify changes and trends in material conditions. Doing this can help assess the progression of potential issues and provide key insights for maintenance planning.
6. Safety Considerations
- Protective gear. Inspectors should wear appropriate protective gear, such as safety glasses, gloves, and protective clothing, especially when working in hazardous environments.
- Safe access. Use appropriate access equipment such as ladders, scaffolding, and harnesses to safely reach inspection areas. Ensure that all access equipment is in good condition and used according to safety guidelines.
- Environmental safety. When conducting inspections in environmentally sensitive areas, follow protocols to minimize disturbance and protect natural habitats. Ensure compliance with environmental regulations and best practices.
7. Compliance with Regulations
- Regulatory standards. Comply with all relevant regulatory standards and guidelines for visual inspections. This includes obtaining necessary certifications and adhering to industry best practices.
- Inspections and audits. Conduct regular inspections and audits to verify compliance with safety protocols and regulatory requirements. Address any identified issues promptly to maintain a safe and compliant inspection environment.