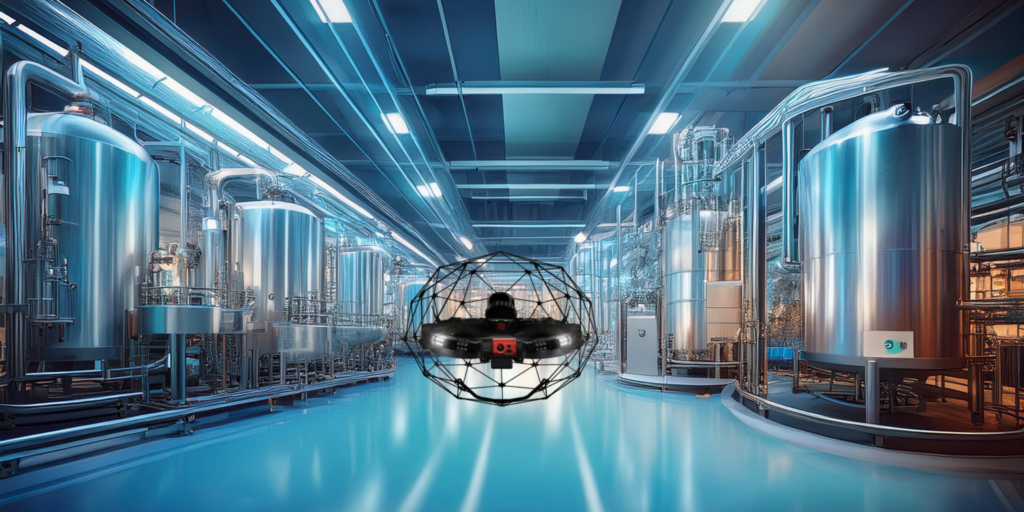
Article
How the Pharmaceutical Industry Is Using Drones to Improve Inspections and Cleaning Protocols
Regular maintenance is essential to pharmaceutical operations. This maintenance helps ensure that plant assets remain in good working order.
It also helps ensure that no contaminants enter the equipment, which is an essential concern for manufacturing pharmaceuticals.
Maintenance management in the pharmaceutical industry follows three general steps:
1. Collect inspection data—collecting data, like photographs or video, showing the condition of assets.
2. Analyze inspection data —review the data collected to make maintenance determinations, including whether defects should be monitored or repaired.
3. Perform maintenance work—actual repair work to fix defects or other mitigating steps to help stop a defect identified in an asset from getting worse.
Traditionally, the first step—inspection data collection—has largely been made in person, by an inspector physically inspecting assets with their naked eye.
Whether the inspection is of the inside of an asset, like a tank or pressure vessel, or of the outside of an asset, like piping or pipe racks, inspectors will wear the appropriate PPE and collect all the visual inspection data they need by looking at the asset following a prescribed method, as well as taking photos or videos reflecting its condition.
These traditional methods for collecting inspection data in the pharmaceutical industry come with dangers to the inspector, including confined space entry and work at height on scaffolding or ropes.
New inspection drones and other robotics solutions are helping pharmaceutical companies improve their inspections by allowing inspectors to collect all the data they need remotely.
The same methods are also being used to support Riboflavin testing (also called Spray Shadow testing), which will be explained in more detail below.
Let’s take a closer look.
How Drones Are Improving Inspections in the Pharmaceutical Industry
Here’s how inspectors and maintenance managers in the pharmaceutical industry are using drones and drone-related software to improve their work.
During Data Collection
During data collection, inspectors are using drones like Flyability’s Elios 2 drone to go into hazardous confined spaces and collect high-quality visual data remotely, avoiding the need to enter those areas themselves
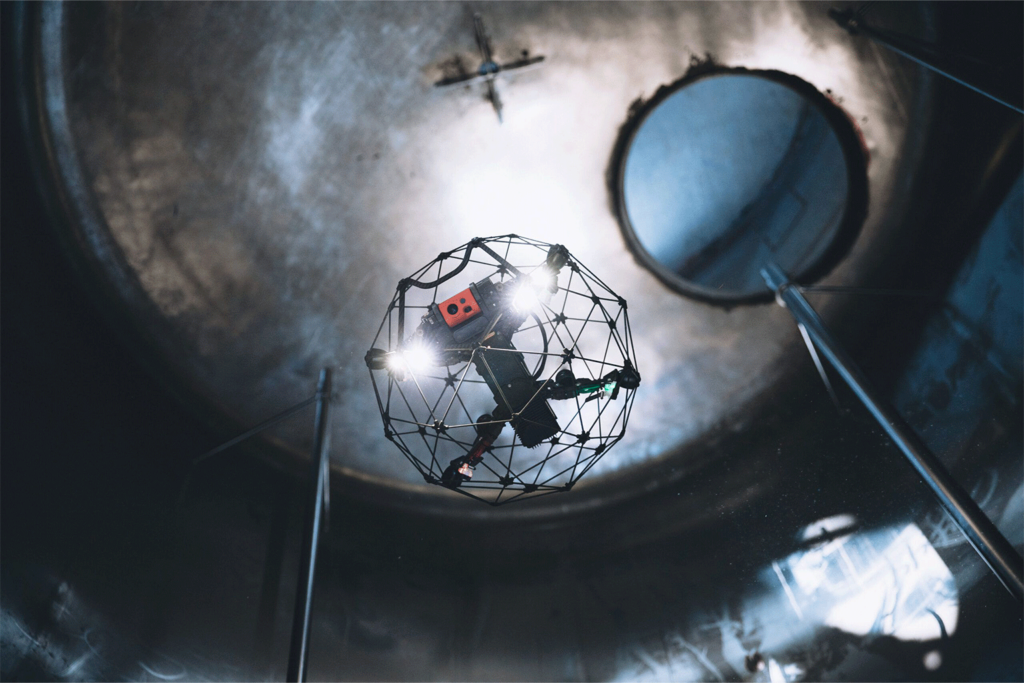
The Elios 2 is a caged indoor drone made specifically for operating in confined spaces. It was designed with collision tolerance features, allowing it to crash while in flight and continue flying unharmed.
In the pharmaceutical industry, the Elios 2 is being used for data collection inside:
- Pressure vessels, to collect visual data showing the condition of agitators, mag mixers, and baffles.
- Refrigeration containers
- Pipe racks and piping, to ensure they’re in good condition and that the ball valves are correctly positioned
- Storage tanks
- Manufacturing tanks
- Other internal areas as needed
After Data Collection
After data collection, inspectors can use new inspection-focused software to help identify defects and track their specific location within an asset.
There is an array of software that supports inspectors for reporting and defect monitoring, including AI-powered software that uses machine learning to detect defects on its own and software like Flyability’s Inspector 3.0, which can pinpoint the location of defects in a sparse point cloud, allowing inspectors to share the precise spot where a flaw is located within an asset.
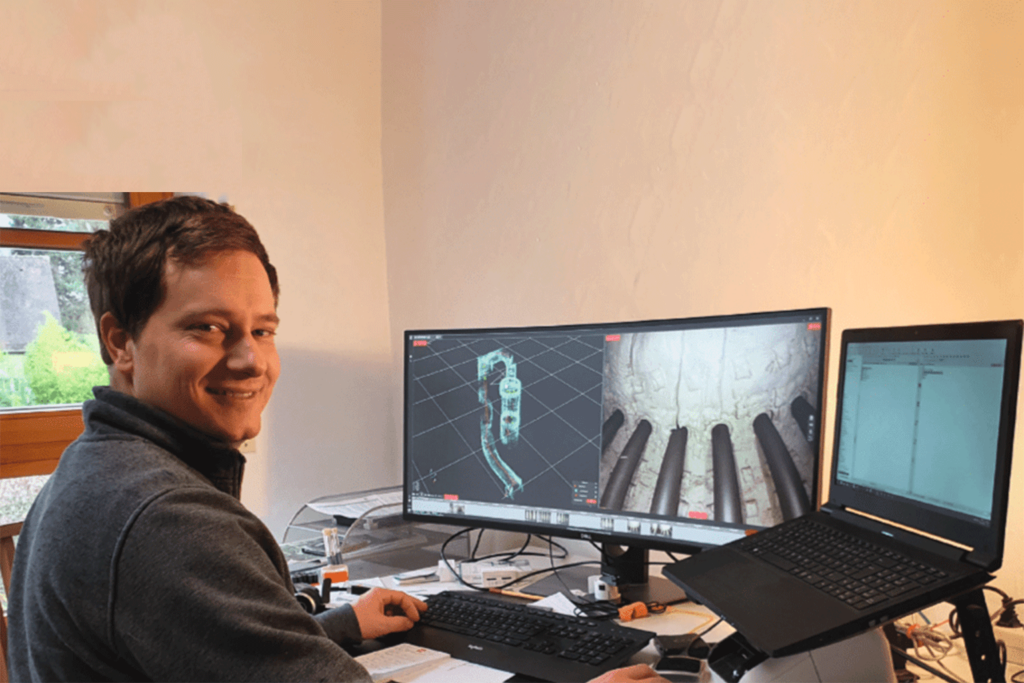
Inspection technology continues to develop, and new advances are leveraging new types of data.
One of the most important innovations for using drones for inspections has been the addition of LiDAR sensors to drones and other robots, which allow inspectors in the pharmaceutical industry to collect data inside assets that can be turned into detailed 3D maps.
These 3D models can then be used to pinpoint the exact location of defects found in inspection data, allowing maintenance crews and inspectors to return to those spots for future monitoring.
They can also be used to track the changes within an entire pharmaceutical plant over time, creating a detailed digital twin of the plant as it was when it first opened that can be compared to future 3D models, providing a comprehensive history of the physical plant.
Drones outfitted with LiDAR are also leveraging new SLAM technology to create 3D models in real-time, while the drone is in flight. SLAM or simultaneous localization and mapping, refers to a method robots can use to position themselves in three-dimensional space in real-time without any further processing needed.
SLAM gives inspectors the benefits of immediate 3D modeling, without having to wait for long processing periods.
It also provides an accurate depiction of the conditions inside an asset while an inspector is flying through it, allowing them to improve the quality of the inspection data they collect before they begin their analysis.
Using Drones to Improve Cleaning Protocols
One additional use for drones like the Elios 2 in the pharmaceutical industry is to use them for Riboflavin testing, which is one way to ensure that manufacturing tanks are being cleaned properly.
During Riboflavin testing, pharmaceutical personnel have to enter a manufacturing tank twice:
- The first time is after the Riboflavin has been sprayed, to ensure that it covers the interior of the tank.
- The second time is after the Riboflavin has been cleaned off, to ensure that the cleaning process worked and left no Riboflavin behind.
These tests help pharmaceutical companies know that their cleaning protocols actually work, and they’re sufficient for maintaining tanks that are clean and free from contaminants. But using a person to enter these tanks is both hazardous and inefficient.
A drone like the Elios 2 can quickly fly into a tank for both confirming that Riboflavin has thoroughly covered the tank’s interior, and for confirming that the cleaning process worked and removed all the Riboflavin.
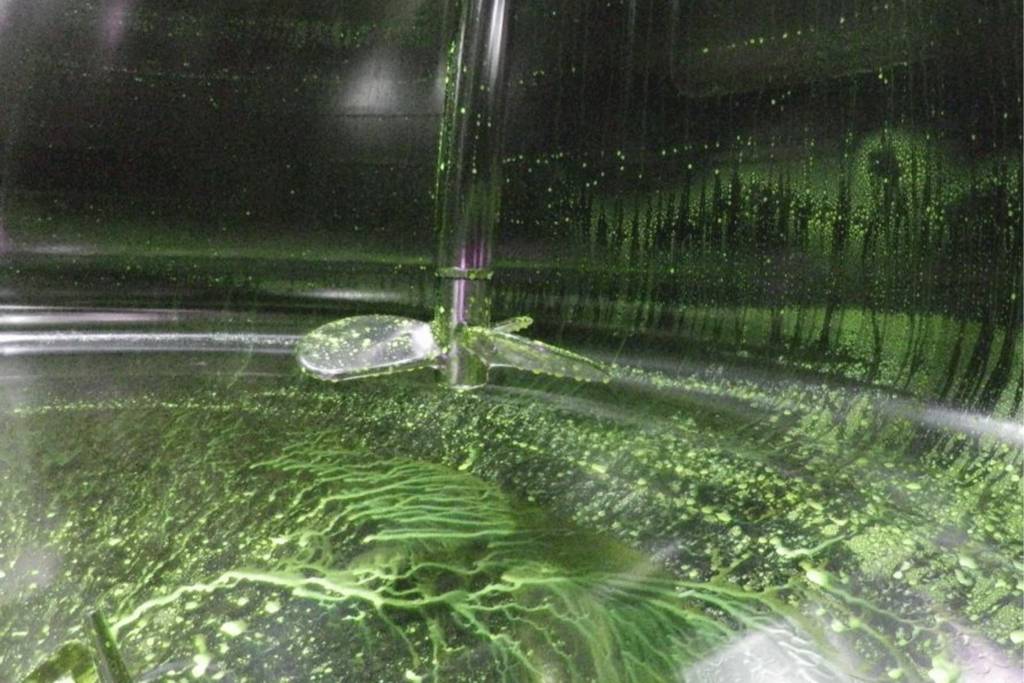
Using a drone for collecting data inside tanks during these cleaning protocol tests improves safety by eliminating the need for a person to enter them. It also improves savings and reduces downtimes for the tank.
At a pharmaceutical plant in Austria, plant personnel were able to save 60,000 Euros and reduce the time needed for five Riboflavin tests from 10 hours to just four by using the Elios 2 instead of the traditional method for reviewing tanks during the testing.
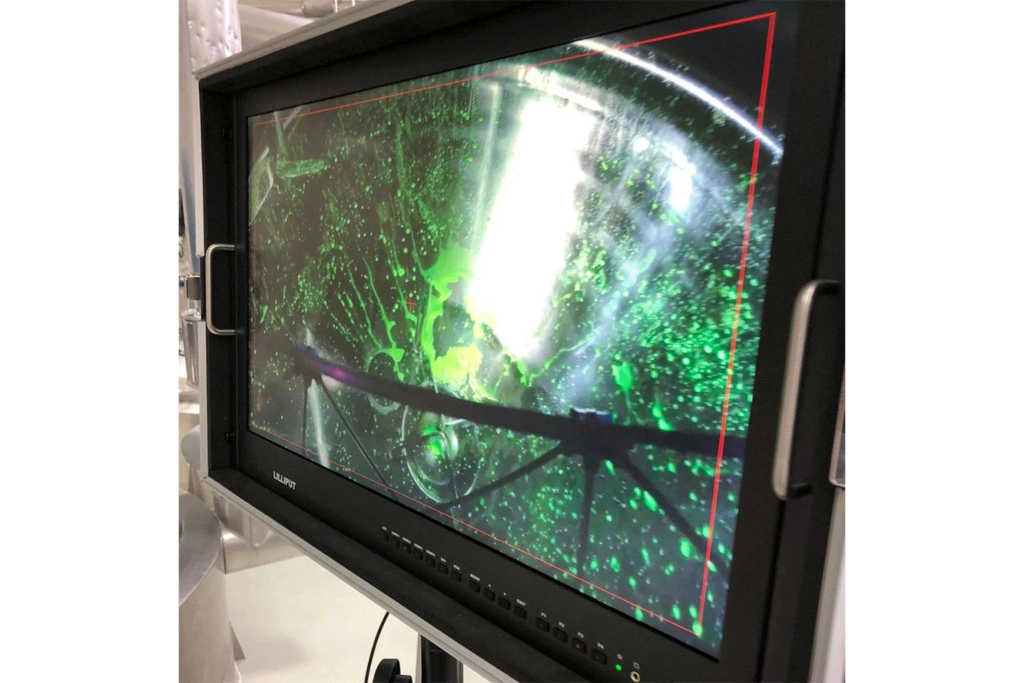