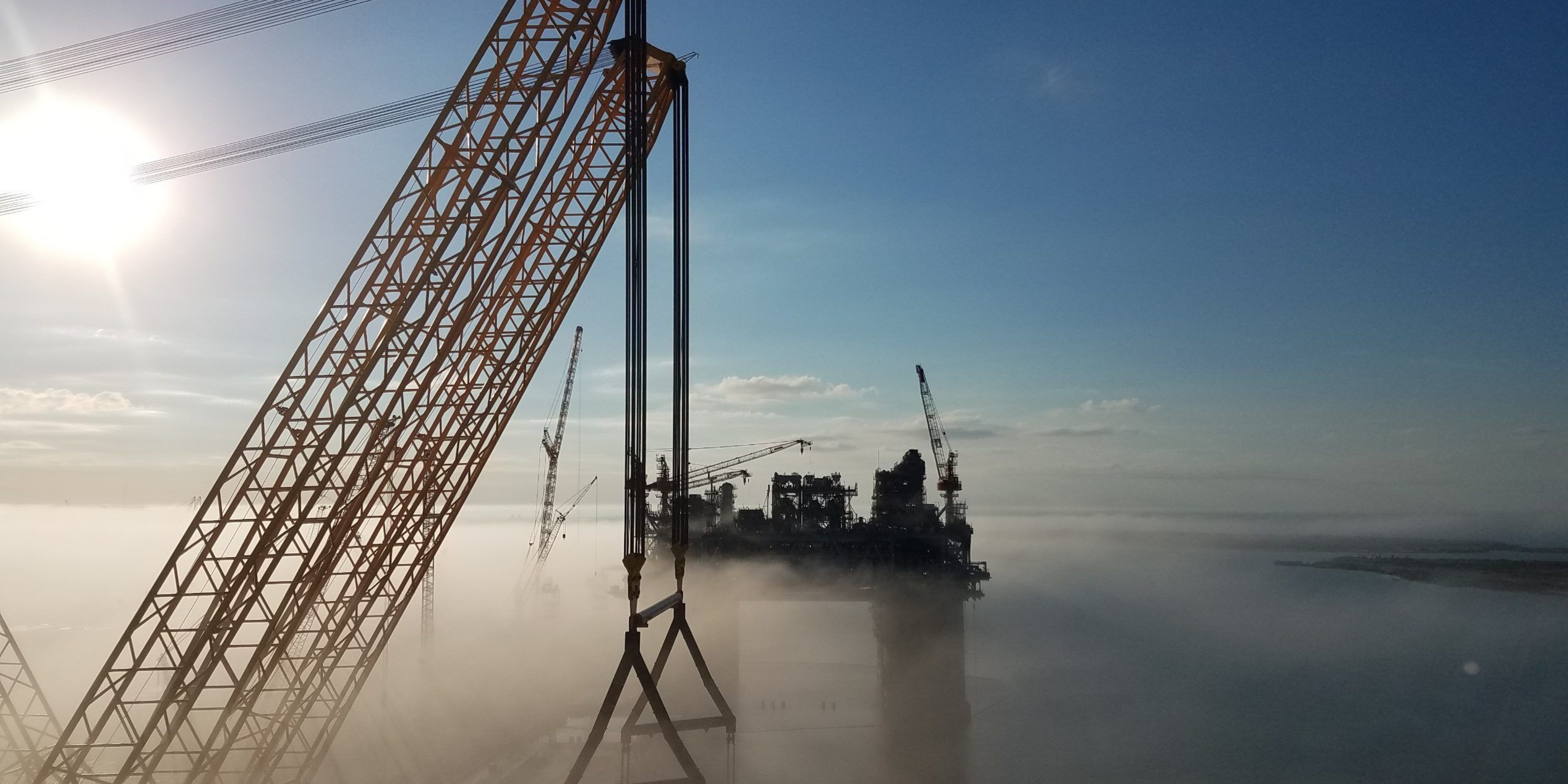
Resources / Case Study / CAN USA Reduces Time for Offshore Drilling & Production Facility Inspections by 60% with the Elios 3
Case Study
CAN USA Reduces Time for Offshore Drilling & Production Facility Inspections by 60% with the Elios 3
MFE’s client CAN USA realized major improvements to safety and savings by using the Elios 3 in offshore drilling and production facility inspections for one of the biggest oil companies in the world.
Benefits
Faster Inspections
Reduced time for inspection from 33 to 13 days, representing a time reduction of 60%.
Improved Safety
Able to avoid the need for confined space entry and rope access by using the drone for remote data collection.
Less Personnel Required
Reduced the number of people needed for the inspection from three to two, making for a reduction in crew size of 30%.
Higher Quality of Inspection
The Elios 3’s collision tolerant design allowed inspectors to fly less than two feet from the inspected surface, providing high-quality inspection data.
Introduction
More and more, oil and gas companies are turning to drones to improve their inspections.
But adoption isn’t always easy. For this case study, we’re going to highlight the benefits CAN USA has realized by incorporating drones into inspections on offshore drilling and production facilities owned by one of the biggest oil companies in the world.
Using drones, CAN USA helped the company improve safety in inspections by avoiding the need for inspectors to work at height and inside confined spaces to collect inspection data. Drones have also helped CAN USA save the company time and realize significant savings in its inspections.
Yet the drone program wasn’t an overnight success. It took time, strong leadership, and investment in getting the right drones and the right training to develop the program.
Keep reading to learn how CAN USA did it.
Customer Needs
CAN USA is one of the leading inspection service providers in the US.
Like many inspection companies, CAN USA has historically relied on rope access to inspect elevated assets on offshore drilling and production facilities, including monorail beams, bridge crane runway systems, and pipe racks. In the same way, it has relied on confined space entry for internal inspections inside assets like ballast or storage tanks.
But the company knew drones could make these inspections better. Drones held the promise of speeding up the inspection process while also improving safety, potentially eliminating the need for inspectors to work at height or in confined spaces.
“MFE Inspection Solutions helps us source the best inspection technology on the market, including drones, so we can focus on providing the best inspection services to our clients.”
Richard Turner, UAV/Robotics Program Manager for CAN USA
To make this vision a reality, CAN USA began to build a drone program that could meet the needs of one of its biggest clients, a US-based oil company that is one of the largest in the world.
Solution
Richard Turner is the UAV/Robotics Program Manager for CAN USA, inheriting the team from David Martin an ASNT L3 who specializes in NDE Inspection, led the effort to build its drone program into the successful operation it is today.
In doing so, he leaned on his own inspection experience as well as the NDE background of Martin and brought in additional aviation experience like James Hurst a commercial fixed wing pilot to approach the challenges both from an inspection and aviation perspective.
In that work, they focused on three key areas:
- Getting the right drone for the job
- Training to perfection
- Promoting internally
Let’s take a close look at each one.
1. Getting the Right Drone for the Job
Not just any drone will do. A key part of CAN USA’s success with its drone program came in identifying the right drone technology for the types of inspections they planned to do.
For offshore oil and gas operations, the right drone was Flyability’s Elios 3.
The Elios 3 is designed specifically for operations in confined spaces. It’s built with a protective cage around it so that it can be collision tolerant, making it ideal for the internal inspections needed on offshore drilling and production facilities.
“The Elios 3 is a great drone for these offshore drilling and production inspections. It flies reliably and lets us get the data we need, both in internal and external environments.”
Richard Turner, UAV/Robotics Program Manager for CAN USA
After research and testing, CAN USA found that the Elios 3 could also be used to inspect external assets like monorail beams and bridge crane runway systems, since it could fly quite close to them without fear of hurting the drone.
This close flying allowed CAN USA’s team to get less than two feet from the object being inspected, a distance that qualified the inspection as a “close inspection,” making it more accurate and of a higher quality than one done farther away.
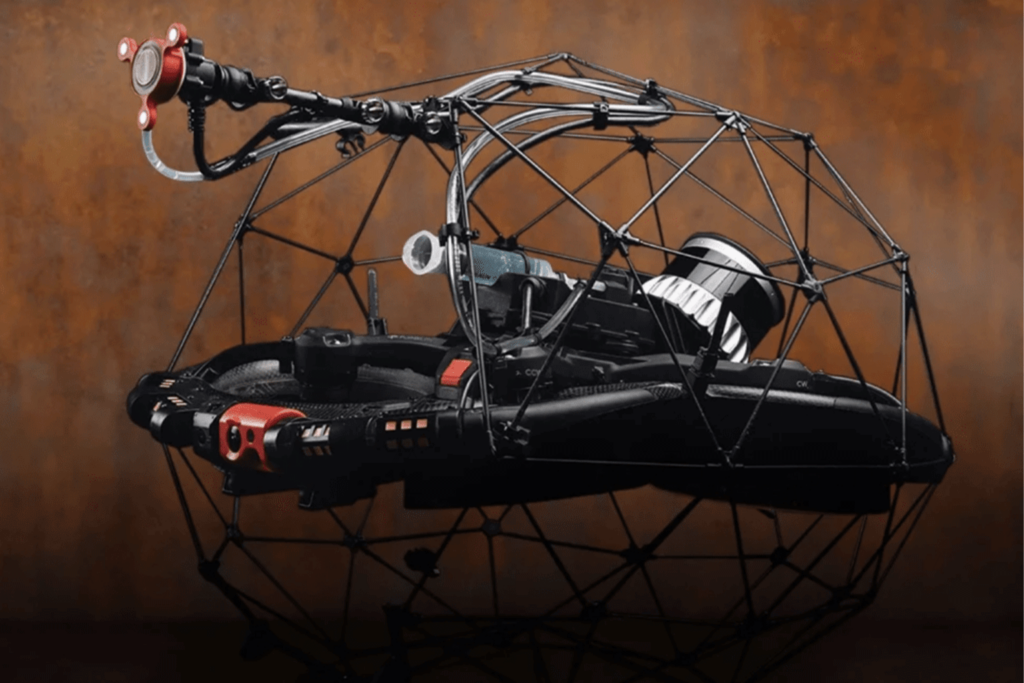
2. Training to Perfection
Offshore drilling and production facilities can be dangerous, chaotic environments.
To ensure success, Turner focused on doing extensive training on shore so that his pilots would be well prepared by the time they actually arrived at a facility to do an inspection. The training also served as a proof of concept, demonstrating that the drones could actually do the work.
To carry out this training, CAN USA set up a controlled test environment where its drone pilots could fly a mission focused on overhead monorail beams. Pilots used the Elios 3 there, following the checklist they would if they were doing the same inspection using rope access.
Each pilot flew the mission over 100 times—and the training paid off. When they started, the pilots couldn’t get all the inspection data they needed in the time allowed by a single battery. But after all of that practice, they could do two inspections on a single battery.
3. Promoting Internally
To build the team of drone pilots, CAN USA didn’t hire new, external people.
Instead, they turned to people who already worked as rope access experts, inspectors, or rescue personnel, and had them learn how to fly.
Doing this accomplished two things:
- It gave current employees a new skill, so that rather than worrying about drones replacing them, they could now be the ones flying the drone.
- It compounded skill sets, so that the pilot flying the drone also had expertise in doing inspections, and would know both what the drone could do and what the goals of the inspection were.
The end result was a team of expert drone pilots who were also experts in inspections on offshore drilling and production facilities.
“When your pilot is also an inspector, you get exactly what you need. This means you get the data you need a lot faster, since the inspector’s not having to explain the inspection side of things to the pilot, and the pilot isn’t having to explain the limitations of the aircraft to the inspector.”
Richard Turner, UAV/Robotics Program Manager for CAN USA
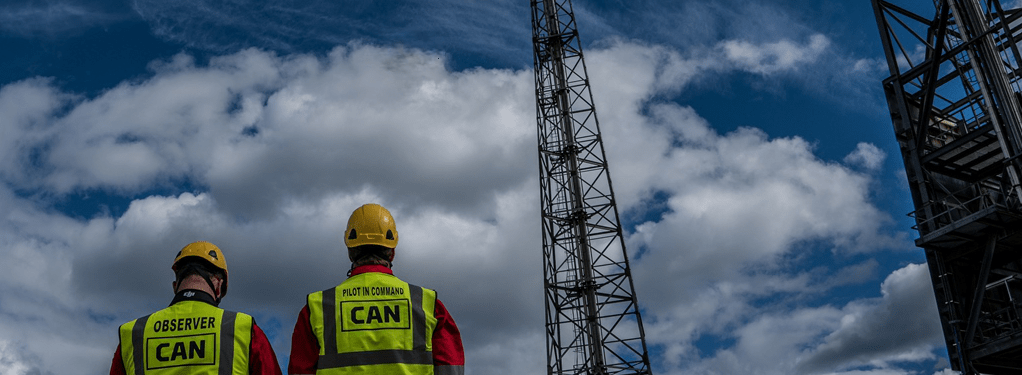
Results
Turner’s careful work on the CAN USA drone program has paid off.
Now, his team has gone far beyond initial testing and is regularly using drones for their inspections on offshore drilling and production facilities.
In a given year they perform dozens of inspections on these facilities for the major oil company, and they have streamlined the process so that it is a routine, predictable effort for everyone involved.
There are many kinds of inspections that CAN USA now does on these facilities using drones, including monorail beams, cranes, and storage tanks.
What Are the Specific Benefits of the Elios 3?
To highlight the benefits of using the Elios 3, CAN USA did a study comparing a guideline tensioner inspection done on an offshore drilling and production facility using traditional rope access to one done with the Elios 3.
Here’s what they found:
- Faster inspections. Doing the inspection using rope access took 33 work days. Using the drone took just 13 work days, representing a time reduction of 60%. The Elios 3’s onboard LiDAR sensor provided real time 3D mapping using SLAM, enhancing situational awareness and making the inspections even faster.
- Higher quality of inspection. The Elios 3’s unique collision-tolerant design let it get up close to the tensioners, allowing it to collect high-quality visual data for a “close” inspection.
- Improved safety. Using the Elios 3 to collect inspection data remotely allowed the team to eliminate the need for work at height using rope access, making the inspection process safer.
- Less personnel required. The rope access approach required three people—two climbers and one rescue personnel. Using the drone reduced the size of the team to just one climber and one rescue personnel, making for a 30% reduction in crew size for the inspection.
What’s Next?
The CAN USA drone program currently has three Elios 3s, with eight pilots qualified to fly them. To ensure their drone pilots receive the proper training, Turner has helped create certifications for each drone its pilots fly, including one for the Elios 3.
He says people are still thinking of new ways to use the Elios 3 for inspections all the time, and his team is always available to test these ideas out.
Continuing to build off the strong foundation of CAN USA’s drone program, Turner looks forward to discovering new use cases for the Elios 3, further implementing CAN USA’s verified approach to drone inspections in new ways and new environments.
Share