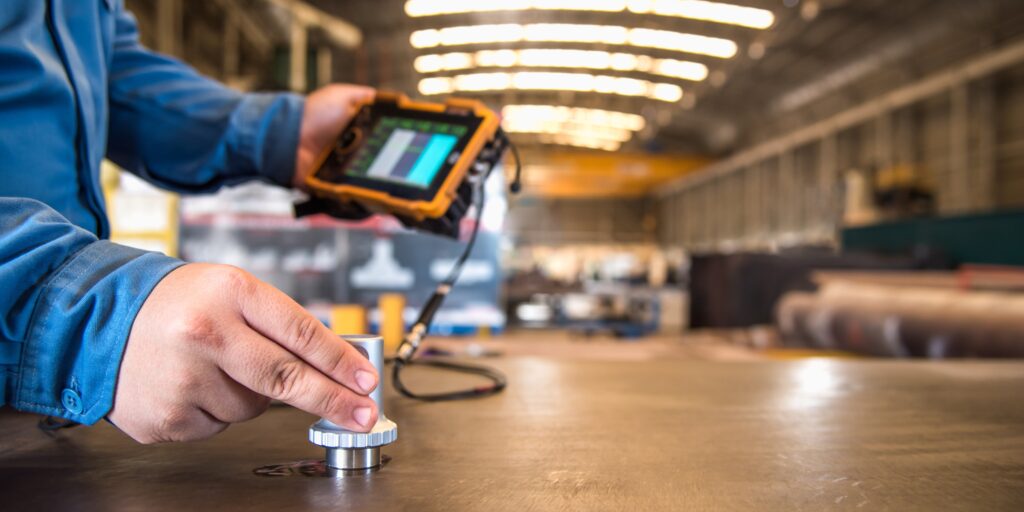
Guide
What Is Material Testing? An In-Depth Guide
Material testing is the process of assessing the properties, performance, and durability of materials used in industrial applications.
→ Jump to material testing equipment for sale and rent.
Alternate names for material testing include:
- Mechanical testing
- Materials analysis
- Materials evaluation
- Quality assurance testing
- Physical properties testing
The primary purpose of material testing is to ensure that materials meet the rigorous quality standards for heavy industries like construction, aerospace, and manufacturing.
It helps identify weaknesses or defects before materials are integrated into products or structures, helping ensure safety, reliability, and performance.
In this guide to material testing we’ll share the top material testing equipment for sale, what material testing is and how it works, and a lot more.
Top Material Testing Equipment for Sale & Rent [New for 2024]
Want to buy or rent material testing equipment? Here are the top options on the market.
1. Fischer FMP 30 Feritscope
The Fischer FMP 30 Feritscope is a precise device designed for measuring the ferrite content in austenitic and duplex steel.
The FMP 30 Feritscope provides accurate, non-destructive testing for components subjected to corrosion and high temperatures, such as those found in the chemical, petrochemical, and power generation industries. Its portability and ease of use make it an ideal tool for both lab and field measurements.
- Measurement capabilities. Accurate ferrite measurement in austenitic and duplex steel
- Key features. Portable design, precise readings, and user-friendly interface
- Top applications. Petrochemical, chemical processing, power generation
- Display. Easy-to-read digital screen
Learn more about the Fischer FMP 30 Feritscope.
2. Fischer FMP 30 Deltascope
The Fischer FMP 30 Deltascope is a highly accurate device for measuring coating thickness on non-magnetic substrates.
The FMP 30 Deltascope utilizes the magnetic induction method, making it ideal for industries like automotive, aerospace, and manufacturing. The instrument’s portability and precision allow for reliable, non-destructive testing in both lab and field environments.
- Measurement capabilities. Accurate measurements on non-magnetic substrates
- Key features. Portable, user-friendly interface, precise readings
- Applications. Automotive, aerospace, manufacturing
- Display. Easy-to-read digital screen
Learn more about the Fischer FMP 30 Deltascope.
3. PosiTector 6000 Coating Thickness Gage
The PosiTector 6000 is a versatile and precise device designed for measuring coating thickness on various substrates, including metals.
Utilizing both magnetic and eddy current principles, it is ideal for applications in industries such as automotive, aerospace, and manufacturing. This durable instrument offers fast, accurate measurements and is equipped with a user-friendly interface for efficient field or lab use.
- Measurement capabilities. Accurate on both ferrous and non-ferrous substrates
- Key features. Durable design, fast readings, and a large display
- Applications. Automotive, aerospace, manufacturing
Learn more about the PosiTector 6000.
What Is Material Testing?
Material testing is a process of evaluating the physical, mechanical, and chemical properties of materials to determine their suitability for specific applications.
It involves measuring the characteristics and behavior of substances like metals, ceramics, plastics, and composites under various conditions.
The main goals of material testing are:
- To assess material quality and performance
- To ensure compliance with design specifications and standards
- To predict material behavior in real-world applications
- To support research and development of new materials
Why Is Material Testing Important?
Material testing plays a crucial role in ensuring the safety, reliability, and performance of materials.
Companies across a range of industries can use material testing to identify potential flaws or weaknesses before they cause critical failures—potentially helping save lives, while also increasing the longevity of critical assets.
Moreover, material testing ensures compliance with industry standards and regulations, reducing the risk of project delays and legal issues. Tests like tensile and hardness testing provide important insights into how materials will perform under stress, offering peace of mind and ensuring long-term durability.
Material Testing in Civil Engineering
Material testing in civil engineering is crucial for evaluating the performance and durability of materials used in large projects like bridges, roads, and buildings.
This testing ensures that materials like concrete, steel, and asphalt meet safety and quality standards.
Common material tests in civil engineering include:
- Compressive strength testing for concrete to ensure it can bear loads
- Soil testing to assess the suitability of the ground for construction.
These tests help engineers make informed decisions about material selection and construction methods, ensuring structural integrity and long-term performance.
Material Testing in Construction
Construction material testing is essential for ensuring that materials like concrete, steel, and asphalt meet safety and quality standards in building projects.
This process involves several types of material testing, including:
- Compressive strength testing for concrete
- Tensile testing for steel
- Durability tests for asphalt
Each test evaluates how these materials will perform under stress, helping to prevent structural failures.
Types of Material Testing
There are several types of material testing used to assess the properties and performance of materials in various industries.
These methods ensure the quality, strength, and durability of materials before they are implemented in critical applications such as construction, aerospace, and manufacturing.
Let’s take a look at the most common material testing methods.
1. Non-Destructive Testing (NDT)
Non-destructive testing allows for the evaluation of materials without damaging them. Methods like ultrasonic testing, radiography, and magnetic particle testing are examples of NDT.
This approach is critical in material testing in civil engineering and aerospace, where components must be inspected for internal flaws without compromising their usability.
Learn more about non-destructive testing.
2. Destructive Testing
Destructive testing involves subjecting a material to stress until it fails to evaluate its strength and durability.
Examples include tensile testing, impact testing, and fatigue testing. This method is commonly used in construction material testing to ensure the integrity of materials like steel and concrete.
Learn more about destructive testing.
3. Hardness Testing
Hardness testing measures a material’s resistance to indentation or scratching.
Common methods include Rockwell, Brinell, and Vickers hardness testing. Hardness tests are crucial for determining the wear resistance of materials used in manufacturing and construction.
Learn more about hardness testing.
4. Tensile Testing
Tensile testing evaluates a material’s ability to withstand tension. A specimen is pulled until it breaks, and the results help determine its strength and ductility.
This is one of the most common raw material testing methods used in industries like automotive and construction to assess materials such as metals and plastics.
5. Fatigue Testing
Fatigue testing determines how a material behaves under repeated cycles of stress.
This method is essential for predicting the lifespan of components that undergo constant loading, such as bridges, pipelines, and aerospace parts.
Material Testing Examples
Material testing is used across various industries to ensure product safety and performance.
Below are two real-world material testing examples.
Construction Material Testing Example
Use case: Concrete Testing for a Slab Foundation
Material testing in construction is essential for ensuring the integrity and safety of structures.
In this example, we’ll focus on concrete testing for a concrete slab foundation.
Project Overview
In a residential construction project, a contractor is preparing to pour a concrete slab foundation. To ensure the quality and strength of the concrete, several tests will be conducted both before and after the pouring process.
Pre-Pour Testing
Concrete Mix Design Verification
Objective: Ensure that the concrete mix meets specified requirements.
Process: The contractor collaborates with a materials engineer to design a mix that includes the right proportions of cement, aggregates, water, and additives. A trial batch may be created to confirm workability and strength.
Slump Test (ASTM C143)
Objective: Assess the workability of the fresh concrete mix.
Process:
- A slump cone is filled with freshly mixed concrete in three layers, each compacted with a rod.
- The cone is lifted, and the vertical distance the concrete slumps is measured.
- A slump of 3-4 inches is typically desired for a slab foundation, indicating good workability without excessive water.
Air Content Test (ASTM C231)
Objective: Determine if the air content in the concrete mix meets specifications, particularly important in freeze-thaw environments.
Process: Using a pressure method, air content is measured to ensure it falls within acceptable limits (usually around 5-7% for most mixes).
During Pouring
Density Testing
Objective: Measure the density of freshly poured concrete.
Process: A known volume container is filled with concrete from the pour. The weight is recorded to calculate density. This helps ensure that the mix is consistent with design specifications.
Post-Pour Testing
Compressive Strength Testing (ASTM C39)
Objective: Verify that the concrete achieves the required compressive strength.
Process:
- Four cylindrical samples (6 inches in diameter, 12 inches tall) are cast from the same batch of concrete.
- Two cylinders are tested at 7 days and two at 28 days using a hydraulic press to determine how much load they can withstand before failure.
- For instance, if the required compressive strength is 4,000 psi, results below this threshold indicate potential issues with the mix or curing process.
Flexural Strength Testing (ASTM C78)
Objective: Assess how well the concrete can resist bending forces.
Process: Concrete beams are tested by applying load until failure occurs. This test helps evaluate how well the slab will perform under load conditions.
Drilled Core Testing (ASTM C42)
Objective: Conduct a more accurate assessment of in-situ concrete strength.
Process:
- After curing, cores are drilled from various locations in the slab.
- These cores are then tested for compressive strength in a laboratory setting to confirm that the slab meets structural requirements.
Conclusion
Through this detailed example of material testing for a concrete slab foundation, it becomes clear that rigorous testing protocols are crucial for ensuring that construction materials meet safety and performance standards.
Each step—from pre-pour testing like slump and air content tests to post-pour compressive strength and flexural tests—plays an integral role in validating that the structure will perform as intended over its lifespan.
This systematic approach not only enhances safety but also helps prevent costly repairs or failures in the future.
Civil Engineering Material Testing Example
Use case: Soil Testing for a Highway Construction Project
Project Overview
A state transportation department is planning to construct a new highway segment. Before construction begins, it is essential to assess the soil properties at the site to ensure it can support the roadway and withstand traffic loads over time.
Pre-Testing Preparation
Site Investigation
Engineers conduct a preliminary site investigation to identify soil types and conditions. Samples are collected from various depths using drilling rigs and test pits.
Sample Collection
Soil samples are taken from different locations along the proposed highway alignment. Each sample is labeled and preserved for laboratory analysis.
Testing Methods
1. Field Testing
Standard Penetration Test (SPT) (ASTM D1586)
Objective: Determine soil density and strength.
Process:
- A split-barrel sampler is driven into the ground at specified intervals using a hammer.
- The number of blows required to drive the sampler a certain distance (usually 12 inches) is recorded.
In-Situ Density Test (Sand Cone Method) (ASTM D1556)
Objective: Measure the moisture content and density of the soil in place.
Process: A hole is excavated in the soil, and the volume of displaced sand is measured using a calibrated cone. The weight of the sand used to fill the hole provides density measurements, critical for assessing compaction.
2. Laboratory Testing
Atterberg Limits Test (ASTM D4318)
Objective: Determine the plasticity characteristics of fine-grained soils.
Process: The liquid limit (LL) and plastic limit (PL) are determined by measuring moisture content at which soil changes from plastic to liquid state.
Compaction Test (Proctor Test) (ASTM D698)
Objective: Establish optimal moisture content for maximum dry density.
Process: Soil samples are compacted in a mold at varying moisture contents. The maximum dry density is determined by measuring weight and volume.
California Bearing Ratio (CBR) Test (ASTM D1883)
Objective: Evaluate subgrade strength for road design.
Process: A cylindrical plunger is pressed into a compacted soil sample, and the pressure required to achieve a specified penetration is measured.
Post-Testing Analysis
Data Compilation
All test results are compiled into a comprehensive report detailing soil properties, including moisture content, density, plasticity, and bearing capacity.
Design Recommendations
Based on test results, engineers make recommendations for foundation design, including necessary reinforcement or stabilization methods if weak soils are identified.
Conclusion
Through this detailed example of soil testing for highway construction, it becomes clear that rigorous testing protocols are essential for ensuring that the ground can adequately support infrastructure.
Each step—ranging from field tests like SPT and density tests to laboratory analyses such as Atterberg limits and CBR tests—plays a vital role in validating that the soil will perform reliably under load conditions.
This systematic approach not only enhances safety but also contributes to the longevity and durability of transportation structures.
Material Testing Services & Jobs
Material testing services provided by labs and inspection companies help businesses ensure the quality, strength, and durability of materials.
Below, we’ll take a look at the services provided by each one, then share some information on jobs in material testing.
Lab Material Testing Services
Material testing laboratories offer a wide range of services to evaluate the properties and performance of various materials.
Below we’ll cover some of the most common types of material testing services provided by labs.
1. Mechanical Testing
- Tensile testing. Measures the strength and ductility of materials by applying a uniaxial load until failure.
- Compression testing. Evaluates how materials behave under compressive loads.
- Flexural testing. Assesses the bending strength of materials, often used for beams and slabs.
- Fatigue testing. Determines the durability of materials under cyclic loading.
- Hardness testing. Measures the resistance of a material to deformation or indentation.
2. Non-Destructive Testing (NDT)
- Ultrasonic Testing (UT). Uses high-frequency sound waves to detect internal flaws in materials.
- Magnetic Particle Testing (MT). Identifies surface and near-surface discontinuities in ferromagnetic materials.
- Radiographic Testing (RT). Utilizes X-rays or gamma rays to visualize internal structures and defects.
- Dye Penetrant Inspection. Reveals surface-breaking defects using a dye that penetrates into cracks.
3. Chemical Testing
- Chemical Composition Analysis. Determines the elemental makeup of metals and alloys.
- Corrosion Testing. Evaluates material performance in corrosive environments, including accelerated aging tests.
- Contaminant Analysis. Identifies and quantifies unwanted substances in materials.
4. Thermal Testing
- Thermal Conductivity Testing. Measures how well a material conducts heat.
- Differential Scanning Calorimetry (DSC). Analyzes thermal transitions such as melting and crystallization temperatures.
- Thermogravimetric Analysis (TGA). Assesses weight changes in a material as it is heated.
5. Soil and Geotechnical Testing
- Atterberg Limits Test. Determines the plasticity characteristics of fine-grained soils.
- Standard Penetration Test (SPT). Evaluates soil density and strength in situ.
- California Bearing Ratio (CBR) Test. Assesses subgrade strength for road design.
6. Dimensional Inspection
- Coordinate Measuring Machine (CMM) Inspection. Verifies dimensional accuracy of machined components against specifications.
- Visual Inspection. Basic checks for surface defects and conformity to specifications.
7. Specialized Material Testing
- Composite Material Testing. Evaluates properties specific to composite materials, including tensile strength and impact resistance.
- Plastic and Rubber Testing. Assesses mechanical properties, chemical resistance, and thermal stability of polymers.
8. Calibration Services
- Calibration of measuring instruments to ensure accuracy and compliance with standards.
Inspection Companies Material Testing Services
Inspection companies typically offer a range of material testing services.
The specific types and scope of these services can vary based on the company’s focus, expertise, and industry requirements.
Below we’ll cover the most common types of material testing services that inspection companies offer.
Concrete Testing
- Services Include: Compressive strength testing, flexural strength testing, slump tests, air content measurement, and temperature checks.
- Purpose: To ensure that concrete meets specified standards for construction projects.
Soil Testing
- Services Include: Atterberg limits tests, compaction tests (Proctor tests), California Bearing Ratio (CBR) tests, and in-situ density tests.
- Purpose: To evaluate soil properties for foundation design and stability.
Asphalt and Bituminous Testing
- Services Include: Density testing, mix design analysis, extraction tests, and gradation tests.
- Purpose: To assess the quality and performance of asphalt materials used in road construction.
Aggregate Testing
- Services Include: Gradation analysis, specific gravity tests, and crushing value tests.
- Purpose: To determine the suitability of aggregates for use in concrete and asphalt mixtures.
Structural Steel Testing
- Services Include: Tensile testing, weld inspections, and non-destructive testing methods like ultrasonic or magnetic particle testing.
- Purpose: To ensure that steel components meet safety and performance standards.
Masonry Testing
- Services Include: Testing of concrete masonry units, mortar mix designs, and brick strength assessments.
- Purpose: To verify that masonry materials comply with building codes.
Specialized Inspections
- Services Include: Bolt and weld inspections, fireproofing inspections, vibration monitoring, and ground-penetrating radar surveys.
- Purpose: To address specific project requirements and ensure compliance with safety regulations.
Material Testing Jobs
Material testing jobs encompass a variety of roles across different industries, each focusing on evaluating the properties and performance of materials.
Here are some of the most common types of material testing jobs.
1. Materials Testing Technician
- Responsibilities: Conduct tests on construction materials like concrete, asphalt, and soil. Perform field and lab testing, prepare samples, and record results.
- Industries: Construction, civil engineering.
2. Quality Control Inspector
- Responsibilities: Inspect materials and products for compliance with specifications. Conduct tests to ensure quality standards are met and report findings.
- Industries: Manufacturing, automotive, aerospace.
3. Laboratory Technician
- Responsibilities: Work in a lab setting to perform chemical, mechanical, and physical tests on various materials. Analyze data and prepare reports.
- Industries: Pharmaceuticals, materials science, plastics.
4. Geotechnical Engineer
- Responsibilities: Analyze soil and rock samples to determine their properties for construction projects. Perform field tests like SPT and lab tests like Atterberg limits.
- Industries: Civil engineering, construction.
5. Metallurgical Engineer
- Responsibilities: Focus on the properties of metals and alloys. Conduct tensile, fatigue, and hardness tests to evaluate material performance.
- Industries: Aerospace, automotive, manufacturing.
6. Composite Materials Engineer
- Responsibilities: Test and analyze composite materials used in aerospace or automotive applications. Perform mechanical testing and assess durability under various conditions.
- Industries: Aerospace, automotive.
7. Non-Destructive Testing (NDT) Technician
- Responsibilities: Use techniques like ultrasonic or radiographic testing to detect flaws in materials without causing damage.
- Industries: Aerospace, construction, manufacturing.
8. Environmental Testing Specialist
- Responsibilities: Test materials for environmental compliance, including chemical composition and contamination levels.
- Industries: Environmental consulting, manufacturing.
9. Research Scientist (Materials Science)
- Responsibilities: Conduct research on new materials or improve existing ones through extensive testing and analysis.
- Industries: Academia, research institutions, advanced manufacturing.
10. Field Inspector
- Responsibilities: Oversee material testing on-site during construction projects to ensure compliance with specifications and safety standards.
- Industries: Construction, civil engineering.
What is material testing?
Material testing is the process of evaluating the properties, strength, and performance of materials to ensure they meet industry standards. It includes various testing methods such as tensile, hardness, and fatigue testing.
Why is material testing important?
Material testing is crucial for ensuring the safety, reliability, and durability of materials used in construction, manufacturing, and other industries. It helps prevent structural failures and ensures compliance with industry regulations.
What types of material testing are there?
There are several types of material testing, including destructive tests like tensile and compressive strength testing, and non-destructive tests like ultrasonic and radiographic testing.
What industries use material testing?
Material testing is used in industries such as construction, aerospace, automotive, and manufacturing to assess material integrity and performance before they are integrated into final products or structures.
How is material testing performed?
Material testing is performed using various methods, such as applying forces to a sample to assess mechanical properties (e.g., tensile, compressive strength) or using instruments to measure characteristics like hardness, chemical composition, or thermal stability.
What is the difference between destructive and non-destructive testing?
Destructive testing involves testing a material to failure, causing permanent damage, while non-destructive testing (NDT) evaluates material properties without causing any damage, allowing the material to be used afterward.
How does material testing contribute to quality control?
Material testing ensures that materials meet the specified standards and performance requirements, helping manufacturers maintain consistent quality in their products. It also identifies defects or variations that could impact product reliability.
What standards are used for material testing?
Material testing standards are set by organizations such as ASTM (American Society for Testing and Materials), ISO (International Organization for Standardization), and AASHTO (American Association of State Highway and Transportation Officials). These standards specify testing procedures, criteria, and requirements.
Can material testing predict material lifespan?
Yes, certain material testing methods, such as fatigue and creep testing, can help predict the lifespan of a material by evaluating how it responds to long-term stress, temperature, or other conditions. This data is used to estimate durability and maintenance schedules.