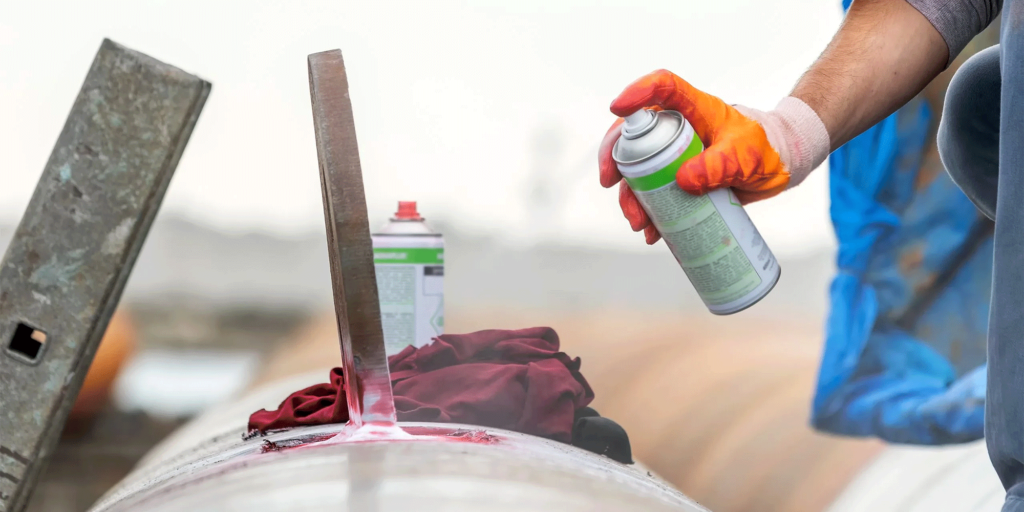
Ressources / Guide / Dye Penetrant Testing: An In-Depth Guide [New for 2025]
Guide
Dye Penetrant Testing: An In-Depth Guide [New for 2025]
Le ressuage est une méthode de CND qui utilise un colorant ou un liquide appliqué sur les surfaces pour identifier les défauts de rupture dans les matériaux non poreux.
Les expressions alternatives pour DPT incluent :
- Contrôle par ressuage (DPI)
- Ressuage (LPT)
- Contrôle par ressuage (LPI)
- Ressuage (PT)
- Ressuage fluorescent (FPT)
Le ressuage est particulièrement efficace pour identifier les types de défauts suivants à la surface de matériaux tels que les métaux, les céramiques et les plastiques :
- Formations de fissures et trous
- Pores et trous d'épingle/porosité de surface
- Fuites
- Autres discontinuités
Les principales industries qui utilisent le DPT sont l'aérospatiale, l'automobile, l'industrie manufacturière et la construction (nous couvrons les principales applications des essais acoustiques ci-dessous).
Cet article présente une vue d'ensemble approfondie du ressuage, en explorant les outils et les techniques utilisés, les différents types de méthodes de ressuage et les scénarios dans lesquels cette méthode est la plus bénéfique.
Vous avez un sujet spécifique en tête ? Utilisez le menu de droite pour naviguer dans ce guide.
Qu'est-ce que le ressuage ?
Le ressuage consiste à appliquer un liquide pénétrant à la surface d'un matériau, à le laisser s'infiltrer dans les fissures ou les défauts, puis à utiliser un révélateur pour ramener le pénétrant à la surface, où il devient visible dans des conditions d'éclairage appropriées.
Grâce à cette approche, les inspecteurs peuvent identifier des problèmes potentiels à la surface du matériau, ce qui les aide à repérer la présence de défauts qui pourraient nécessiter une maintenance.
Principes du ressuage
Le principe fondamental de la DPT est basé sur la capillarité, dans laquelle un liquide pénétrant est aspiré dans les défauts qui brisent la surface.
Voici les principales étapes du DPT :
1. Préparation de la surface
Inspectors thoroughly clean the surface of the material you plan to test to remove any contaminants such as dirt, grease, or paint that could interfere with the penetrant’s ability to enter defects.
2. Application du pénétrant
Les inspecteurs appliquent le liquide pénétrant à la surface du matériau, généralement par pulvérisation, au pinceau ou par immersion. Après l'application, ils le laissent reposer sur la surface pendant une durée déterminée, appelée temps de séjour, afin de s'assurer qu'il pénètre tous les défauts.
3. Élimination de l'excès de pénétrant
Après le temps de séjour, les inspecteurs enlèvent soigneusement l'excès de pénétrant de la surface, ne laissant que le pénétrant qui s'est infiltré dans les défauts.
4. Demande du développeur
Les inspecteurs appliquent un révélateur à la surface pour faire sortir le pénétrant des défauts et créer une indication visible. Le révélateur agit comme un buvard, attirant le pénétrant à la surface et l'étalant pour former une marque visible.
5. Contrôle
Les inspecteurs examinent la surface dans des conditions d'éclairage appropriées (lumière visible ou lumière ultraviolette pour les pénétrants fluorescents) afin d'identifier et d'évaluer les indications de défauts.
6. Post-nettoyage
Après l'inspection, les inspecteurs nettoient le matériau, en retirant le révélateur et tout pénétrant restant de la surface et en remettant la surface du matériau dans son état d'origine.
Avantages du ressuage
- Haute sensibilité. La DPT est très sensible aux petits défauts de rupture de surface, ce qui la rend efficace pour détecter les fissures minuscules et autres discontinuités.
- Polyvalence. Peut être utilisé sur une large gamme de matériaux non poreux, y compris les métaux, les céramiques, les plastiques et les composites.
- Rentabilité. Généralement moins coûteux que les autres méthodes de CND, ce qui en fait un choix économique pour de nombreuses applications.
- Facilité d'utilisation. Relativement simple et ne nécessitant pas d'équipement complexe, il permet des inspections rapides et faciles.
Limites du ressuage
- Préparation de la surface. Une bonne préparation de la surface est nécessaire pour éliminer les contaminants qui pourraient empêcher le pénétrant de pénétrer dans les défauts.
- Détection en surface uniquement. Efficace uniquement pour détecter les défauts de rupture en surface, il ne permet pas d'identifier les défauts souterrains.
- Restrictions matérielles. Ne convient pas aux matériaux poreux, car le pénétrant s'infiltre dans l'ensemble du matériau et pas seulement dans les défauts.
- Préoccupations environnementales et sanitaires. L'utilisation de produits chimiques dans le pénétrant et le révélateur nécessite une manipulation et une élimination appropriées pour garantir la sécurité de l'environnement et de la santé.
Outils de ressuage
Le ressuage implique l'utilisation de divers outils et matériaux, parmi lesquels les inspecteurs peuvent faire des choix différents en fonction de leurs besoins et de leurs préférences quant à la manière d'effectuer le contrôle.
Vous trouverez ci-dessous les types d'outils de ressuage les plus courants. Nous avons classé ces outils en cinq catégories, avec des types spécifiques pour chacune d'entre elles (certaines catégories n'ont qu'un seul type).
1. Pénétrants
I. Pénétrants visibles sont des pénétrants visibles dans des conditions normales d'éclairage, généralement colorés en rouge pour une meilleure visibilité.
- Comment ils fonctionnent. Le pénétrant est appliqué sur la surface et on le laisse agir, s'infiltrant dans tous les défauts qui brisent la surface. L'excès de pénétrant est ensuite éliminé et un révélateur est appliqué pour révéler les défauts.
- Applications. Convient aux inspections générales dans des environnements bien éclairés, lorsqu'une sensibilité élevée n'est pas nécessaire.
II. Pénétrants fluorescents sont des pénétrants qui deviennent fluorescents sous l'effet de la lumière ultraviolette (UV), offrant un contraste élevé pour l'identification des irrégularités.
- Comment ils fonctionnent. Les inspecteurs appliquent le pénétrant sur la surface et le laissent agir. Après avoir enlevé l'excès de pénétrant, ils appliquent un révélateur et inspectent la surface sous une lumière UV, qui fait briller le pénétrant dans les défauts.
- Applications. Préféré pour les inspections à haute sensibilité et dans les environnements à faible luminosité, comme dans l'aérospatiale et l'industrie automobile.
2. Nettoyeurs
I. Dans le contexte du DPT, les nettoyeurs comprennent solvants ou détergents utilisés pour nettoyer la surface d'un matériau avant et après l'application du pénétrant.
- Comment ils fonctionnent. Les nettoyants éliminent les contaminants tels que la saleté, la graisse, l'huile et la peinture qui pourraient entraver la capacité du pénétrant à pénétrer dans les défauts et la visibilité des indications.
- Applications. Essentiel pour une bonne préparation de la surface et un nettoyage post-inspection dans tous les processus DPT.
3. Développeurs
I. Développeurs de poudre sèche sont des poudres finement divisées que les inspecteurs appliquent à la surface des matériaux après avoir enlevé l'excès de pénétrant.
- Comment ils fonctionnent. La poudre attire le pénétrant hors des défauts et l'étale, formant une indication visible.
- Applications. Convient pour une utilisation sur des surfaces rugueuses et dans des conditions où les révélateurs liquides ne sont pas pratiques.
II. Développeurs humides sont des développeurs en suspension dans un support liquide, disponibles dans des formulations à base d'eau ou de solvant.
- Comment ils fonctionnent. Le révélateur est pulvérisé ou brossé sur la surface, où il contribue à faire sortir le pénétrant des défauts et à créer une indication visible.
- Applications. Idéal pour les surfaces lisses et les inspections détaillées, il permet une meilleure mobilité et visibilité des particules.
III. Réviseurs humides non aqueux sont des développeurs en suspension dans un solvant, souvent utilisés sous forme d'aérosol.
- Comment ils fonctionnent. Les inspecteurs pulvérisent le révélateur sur la surface, où il s'évapore, laissant une fine pellicule qui attire le pénétrant et forme une indication visible.
- Applications. Utilisé pour les inspections sur le terrain et dans les situations où un séchage rapide est nécessaire.
4. Matériel d'éclairage
I. Sources de lumière visible sont des équipements d'éclairage standard utilisés pour inspecter les indications formées par les pénétrants visibles.
- Comment ils fonctionnent. Un éclairage adéquat garantit que les indications sont clairement visibles pour l'inspecteur.
- Applications. Indispensable pour les inspections utilisant des pénétrants visibles dans des environnements bien éclairés.
II. Sources de lumière ultraviolette (UV) sont des lampes UV utilisées pour éclairer les indications de ressuage fluorescentes.
- Comment ils fonctionnent. La lumière UV fait briller le pénétrant fluorescent, ce qui rend les indications très visibles.
- Applications. Indispensable pour les inspections à haute sensibilité utilisant des pénétrants fluorescents, en particulier dans les environnements à faible luminosité.
5. Outils d'application
I. Flacons pulvérisateurs et aérosols sont des récipients utilisés pour appliquer des pénétrants, des révélateurs et des nettoyants à la surface du matériau.
- Comment ils fonctionnent. Ces outils garantissent une application uniforme et contrôlée des matériaux d'essai.
- Applications. Couramment utilisé pour une application rapide et efficace en laboratoire et sur le terrain.
II. Brosses et cuves d'immersion sont des outils utilisés pour appliquer des pénétrants et des révélateurs, en particulier dans des environnements contrôlés.
- Comment ils fonctionnent. Les brosses permettent une application précise, tandis que les cuves d'immersion sont utilisées pour plonger les pièces dans le pénétrant.
- Applications. Convient aux inspections détaillées et aux opérations de test à grande échelle.
Types de ressuage
Le ressuage englobe plusieurs techniques, chacune adaptée à des besoins et des applications d'inspection spécifiques. Ces méthodes varient en fonction du type de pénétrant utilisé et de la méthode d'application.
Voici les principaux types de ressuage :
1. Ressuage visible
Méthode qui utilise des pénétrants visibles (non fluorescents) pour détecter les défauts de rupture de la surface.
- Comment cela fonctionne-t-il ?. L'inspecteur applique le pénétrant sur la surface, le laisse agir, puis l'enlève. Un révélateur est appliqué pour faire sortir le pénétrant des défauts, créant ainsi des indications visibles dans des conditions d'éclairage normales.
- Applications. Il convient pour les inspections générales ne nécessitant pas une sensibilité élevée et dans des environnements bien éclairés, telles que la maintenance de routine et le contrôle de la qualité dans l'industrie manufacturière.
2. Ressuage fluorescent
Méthode utilisant des pénétrants fluorescents pour détecter les défauts de rupture de surface, fournissant des indications à fort contraste sous la lumière ultraviolette (UV).
- Comment cela fonctionne-t-il ?. Les inspecteurs appliquent le pénétrant fluorescent sur la surface, le laissent reposer, puis l'enlèvent. Ils appliquent ensuite un révélateur pour faire sortir le pénétrant des défauts. Après ces étapes, ils inspectent la surface sous une lumière UV, qui fait briller le pénétrant dans les défauts, rendant les indications très visibles.
- Applications. Préféré pour les inspections à haute sensibilité et dans les environnements à faible luminosité, comme dans l'aérospatiale, l'automobile et les composants structurels critiques où la détection des moindres défauts est cruciale.
3. Ressuage lavable à l'eau
Type de contrôle par ressuage où l'excès de pénétrant peut être éliminé de la surface à l'aide d'eau.
- Comment cela fonctionne-t-il ?. Les inspecteurs appliquent le pénétrant lavable à l'eau sur la surface et le laissent agir. Après le temps de séjour, ils éliminent l'excès de pénétrant par un rinçage à l'eau, appliquent un révélateur pour faire sortir le pénétrant des défauts, créant ainsi des indications visibles, et effectuent leur inspection.
- Applications. Convient aux inspections où la facilité d'enlèvement est importante, couramment utilisé dans les opérations de fabrication et de maintenance.
4. Ressuage post-émulsifiable
Méthode utilisant un pénétrant post-émulsifiable, qui nécessite un émulsifiant pour rendre l'excès de pénétrant lavable à l'eau.
- Comment cela fonctionne-t-il ?. Les inspecteurs appliquent le pénétrant et le laissent agir. Ils appliquent ensuite un émulsifiant sur la surface, convertissant le pénétrant en une forme lavable à l'eau. Après avoir rincé le pénétrant émulsifié, ils appliquent un révélateur pour mettre en évidence les défauts et effectuent leur inspection.
- Applications. Idéal pour les inspections de haute sensibilité où l'élimination contrôlée du ou des pénétrants est nécessaire, comme dans l'aérospatiale et la mécanique de précision.
5. Ressuage par solvant amovible
Méthode dans laquelle l'excès de pénétrant est éliminé à l'aide d'un solvant nettoyant.
- Comment cela fonctionne-t-il ?. Les inspecteurs appliquent le pénétrant à solvant sur la surface et le laissent agir. Ils éliminent ensuite l'excès de pénétrant à l'aide d'un solvant nettoyant, appliquent un révélateur pour faire sortir le pénétrant des défauts et créer des indications visibles, puis effectuent l'inspection.
- Applications. Convient aux inspections sur le terrain et aux situations où l'eau n'est pas facilement disponible, couramment utilisé pour l'entretien et l'inspection de grandes structures.
Choix des pénétrants, des décapants et des révélateurs pour le ressuage
La sélection des bons pénétrants, décapants et révélateurs est un élément crucial du contrôle par ressuage.
Chaque composant joue un rôle essentiel dans la révélation des défauts de rupture de surface dans les matériaux non poreux.
Cette section présente les options disponibles pour chaque composant et fournit des conseils pour faire les meilleurs choix en fonction de vos besoins spécifiques en matière de tests.
1. Choix des pénétrants
Les pénétrants sont des liquides qui s'infiltrent dans les défauts de surface.
Leur application est la première étape du processus de ressuage. Ils sont disponibles en plusieurs formulations et peuvent être classés en fonction de leur visibilité et de leur sensibilité.
Voici les principales options de ressuage :
I. Pénétrants visibles (contraste de couleur)
Les pénétrants visibles sont généralement rouges et offrent une grande visibilité sur le fond blanc du révélateur.
- Applications. Convient aux inspections générales ne nécessitant pas une grande sensibilité. Couramment utilisé pour les inspections sur le terrain et les contrôles de maintenance.
- Avantages. Facile à appliquer et à interpréter sans nécessiter d'équipement spécial.
II. Pénétrants fluorescents
Ces pénétrants brillent sous la lumière ultraviolette (UV), ce qui leur confère une grande sensibilité et une bonne visibilité des défauts.
- Applications. Idéal pour les inspections à haute sensibilité dans des secteurs tels que les infrastructures critiques, l'aérospatiale et l'industrie automobile, où la détection de défauts très fins est essentielle.
- Avantages. Offre des capacités supérieures de détection des défauts, en particulier dans des conditions de faible luminosité.
Considérations supplémentaires sur les pénétrants : Niveaux de sensibilité
Les niveaux de sensibilité des options de ressuage vont du niveau 1 (faible sensibilité) au niveau 4 (ultra-haute sensibilité), chaque niveau indiquant la capacité du pénétrant à détecter des défauts de plus en plus fins.
Des niveaux de sensibilité plus élevés sont utilisés pour les inspections critiques nécessitant la détection de défauts très petits et subtils, tels que ceux des composants aérospatiaux.
- Niveau 1 (faible sensibilité). Pour la détection de défauts importants et facilement visibles.
- Niveau 2 (sensibilité moyenne). Inspections à des fins générales .
- Niveau 3 (sensibilité élevée). Pour les inspections critiques nécessitant la détection de défauts fins.
- Niveau 4 (ultra-haute sensibilité). Utilisé dans les applications où la plus grande sensibilité est nécessaire, comme les composants aérospatiaux.
2. Le choix des déménageurs
Les dissolvants sont utilisés pour nettoyer l'excès de pénétrant de la surface avant d'appliquer le révélateur.
Le choix du décapant dépend du type de pénétrant utilisé et du matériau inspecté.
Voici les principales options d'élimination :
I. Dissolvants à base de solvant
Les décapants à base de solvant sont utilisés pour nettoyer les pénétrants visibles et fluorescents.
- Applications. Convient à la plupart des matériaux et des environnements. Couramment utilisé sur le terrain et en laboratoire.
- Avantages. Efficace pour éliminer le colorant pénétrant sans laisser de résidu, ce qui permet d'obtenir des indications claires.
II. Décapants lavables à l'eau
Ces décapants permettent d'éliminer le pénétrant avec de l'eau.
- Applications. Idéal pour une utilisation avec des pénétrants lavables à l'eau dans des environnements où l'eau est facilement disponible.
- Avantages. Processus de retrait simple et rapide, respectueux de l'environnement.
III. Dissolvants post-émulsifiables
Ils nécessitent l'application d'un émulsifiant avant que le pénétrant puisse être lavé à l'eau.
- Applications. Utilisé avec des pénétrants post-émulsifiables pour contrôler le processus d'enlèvement et améliorer la sensibilité.
- Avantages. Permet de mieux contrôler le processus d'enlèvement, ce qui permet des inspections plus précises.
3. Choix des développeurs
Les révélateurs permettent d'extraire le pénétrant piégé dans les défauts vers la surface, créant ainsi une indication visible des irrégularités d'une surface. Ils se présentent sous plusieurs formes, chacune offrant des avantages uniques.
Voici les principales options qui s'offrent aux développeurs :
I. Développeurs de poudre sèche
Poudre fine appliquée sur la surface d'essai pour absorber le pénétrant.
- Applications. Utilisé couramment pour les inspections où un minimum de salissure est souhaitable.
- Avantages. Application simple, adaptée à la plupart des environnements, en particulier aux inspections sur le terrain.
II. Développeurs suspendus à l'eau
Poudres en suspension dans l'eau, créant une boue qui est appliquée sur la surface d'essai.
- Applications. Idéal pour les grandes surfaces et lorsque de l'eau est disponible.
- Avantages. Il assure une couverture uniforme et est facile à retirer après l'inspection.
III. Développeurs solubles dans l'eau
Se dissout dans l'eau pour former une solution claire appliquée sur la surface à tester.
- Applications. Convient aux environnements contrôlés tels que les laboratoires.
- Avantages. Application et retrait faciles, résidus minimes.
IV. Développeurs humides non aqueux
Suspensions de révélateurs dans des solvants, pulvérisées sur la surface à tester.
- Applications. Applications. Utilisé lorsque les révélateurs à base d'eau ne conviennent pas.
- Avantages. Séchage rapide, haute sensibilité, convient aux pièces petites et complexes.
4. Considérations supplémentaires pour le choix des pénétrants, des décapants et des révélateurs
Voici quelques autres points importants à garder à l'esprit lors du choix des pénétrants, des décapants et des révélateurs pour le ressuage :
- Compatibilité. S'assurer que le pénétrant, le décapant et le révélateur choisis sont compatibles entre eux et avec le matériau testé. Se référer aux recommandations du fabricant et aux normes industrielles pour obtenir des conseils.
- Environnement. Tenez compte de l'environnement d'essai (terrain ou laboratoire) et des ressources disponibles (approvisionnement en eau, lumière UV) lors de la sélection de ces produits.
- Santé et sécurité. Évaluer les implications des produits pour la santé et la sécurité, notamment en termes d'inflammabilité, de toxicité et de nécessité d'un équipement de protection.
- Normes industrielles. Respecter les normes et réglementations industrielles pertinentes (par exemple, ASTM E1417/E1417M) afin de garantir la sécurité, la conformité et la fiabilité des résultats des tests.
Quand l'essai par ressuage est-il nécessaire ?
Le ressuage est une méthode d'inspection essentielle dans plusieurs scénarios industriels pour garantir la qualité, la sécurité et la fiabilité des matériaux et des composants.
Voici les principales situations qui nécessitent un contrôle par ressuage :
1. Contrôle et assurance de la qualité dans la fabrication
- Processus de production. Au cours de la fabrication, le DPT est utilisé pour vérifier que les matériaux et les composants répondent aux normes de qualité spécifiées. Il s'agit de détecter les défauts de surface tels que les fissures, les pores et les inclusions afin de garantir l'intégrité du produit final.
- Contrôle des matériaux entrants. Le DPT est utilisé pour inspecter les matières premières avant qu'elles ne soient utilisées dans la production, afin de s'assurer qu'elles répondent aux spécifications requises et qu'elles sont exemptes de défauts de surface.
2. Inspection des soudures
- Intégrité de la soudure. Le ressuage est essentiel pour inspecter les soudures afin de détecter les défauts de surface tels que les fissures, l'absence de fusion et la porosité. Garantir l'intégrité des soudures est vital pour la sécurité structurelle des joints soudés.
- Inspection après soudage. After welding, DPT is used to inspect welded joints for any surface defects that may have formed during the welding process.
3. Maintenance préventive et inspections programmées
- Entretien courant. DPT is part of regular preventive maintenance schedules to monitor the condition of critical components and infrastructure. This helps in early detection of potential issues, preventing unexpected failures and downtime.
- Surveillance des conditions. Les inspections DPT continues ou périodiques permettent de surveiller les composants dans des conditions opérationnelles, de fournir des données précieuses sur leur état et de prévoir leur durée de vie restante.
4. Conformité à la sécurité et exigences réglementaires
- Normes réglementaires. De nombreuses industries sont soumises à des réglementations strictes en matière de sécurité qui imposent des contrôles réguliers par ressuage. Le respect de ces réglementations garantit que les composants et les structures répondent aux normes de sécurité, réduisant ainsi le risque d'accident.
- Certification et accréditation. Le DPT est souvent exigé à des fins de certification, par exemple pour l'obtention de certifications d'appareils à pression et de pipelines auprès d'organismes de réglementation.
5. Recherche et développement
- Caractérisation des matériaux. Dans le domaine de la recherche et du développement, le DPT aide à caractériser les nouveaux matériaux, en étudiant leurs propriétés et leur comportement dans différentes conditions. Ces informations sont essentielles pour développer des matériaux avancés aux performances accrues.
- Essais de prototypes. La DPT est utilisée pour évaluer les prototypes, en identifiant les défauts ou les faiblesses qui doivent être corrigés avant la production à grande échelle.
Les 5 principales industries qui font appel au ressuage + les applications spécifiques qu'elles utilisent
Le ressuage est une méthode d'essai non destructive polyvalente qui trouve des applications dans un large éventail d'industries.
Voici les cinq principaux secteurs d'activité qui utilisent la DPT, avec des applications spécifiques pour chacun d'entre eux.
1. Industrie du pétrole et du gaz
Dans l'industrie du pétrole et du gaz, le ressuage est essentiel pour maintenir la sécurité et la fiabilité des pipelines et autres infrastructures.
- Inspection des pipelines. Le DPT est utilisé pour détecter les défauts de rupture de surface dans les pipelines, afin d'assurer leur intégrité et de prévenir les accidents. fuites ou des ruptures qui pourraient entraîner des catastrophes environnementales.
- Inspections des appareils à pression. Contrôler les cuves sous pression pour détecter les signes de défauts de surface tels que les fissures et la corrosion, afin d'assurer la sécurité de leur fonctionnement.
- Inspection des tubes de forage et des tubages. Inspecter les tubes de forage et les tubages pour détecter les défauts de surface susceptibles de compromettre la sécurité et l'efficacité des opérations de forage.
2. Industrie de la production d'énergie
Dans le secteur de la production d'énergie, le ressuage est essentiel pour maintenir l'intégrité des composants critiques des centrales électriques.
- Inspection des pales de turbines. Le DPT est utilisé pour inspecter les pales de turbines afin de détecter les défauts de surface et de garantir leur fonctionnement efficace et sûr dans des conditions de stress et de température élevées.
- Inspections de chaudières et d'appareils à pression. Détecter les défauts de surface des chaudières et des appareils à pression, afin de garantir la sécurité de leur fonctionnement et de prévenir les défaillances inattendues.
- Inspection des générateurs et des transformateurs. Inspecter les composants critiques des générateurs et des transformateurs, afin de garantir leur fiabilité et leurs performances dans les systèmes de production d'énergie.
3. Industrie manufacturière
Dans l'industrie manufacturière, le ressuage est essentiel pour garantir la qualité et la fiabilité des produits.
- Assurance qualité. Le DPT est utilisé pour inspecter les matières premières, les produits intermédiaires et les assemblages finaux afin de détecter les défauts de surface tels que les fissures, les pores et les inclusions. Cela permet de s'assurer que seuls des produits exempts de défauts parviennent au client.
- Inspection des pièces usinées. Contrôler les pièces usinées pour détecter les défauts et s'assurer qu'elles respectent les spécifications et les tolérances de conception.
- Inspections des revêtements de surface. Contrôler l'épaisseur et l'uniformité des revêtements de surface, en s'assurant qu'ils offrent une protection adéquate et qu'ils répondent aux normes de qualité.
4. Industrie aérospatiale
L'industrie aérospatiale s'appuie fortement sur le ressuage pour maintenir la sécurité et les performances des composants d'aéronefs.
- Inspections structurelles des aéronefs. Le DPT est utilisé pour inspecter les composants structurels critiques tels que les ailes, les sections de fuselage et le train d'atterrissage afin de détecter les défauts de surface tels que les fissures et la corrosion. S'assurer que ces composants sont exempts de défauts est vital pour la sécurité des vols.
- Composants du moteur. Contrôle des composants du moteur, détection des défauts de surface susceptibles de compromettre les performances et la sécurité du moteur.
- Inspection des matériaux composites. Inspecter les matériaux composites à la recherche de fissures superficielles et d'autres défauts susceptibles d'affecter leur intégrité et leurs performances.
5. Industrie automobile
L'industrie automobile utilise le ressuage pour garantir la qualité et la sécurité des composants des véhicules.
- Inspection des composants du moteur. Le DPT est utilisé pour inspecter les composants critiques des moteurs, tels que les culasses, les vilebrequins et les arbres à cames, afin de détecter les défauts de surface et de s'assurer qu'ils sont conformes aux normes de sécurité et de performance.
- Inspection des roues et des essieux. Détecter les fissures et autres défauts dans les roues et les essieux, afin de s'assurer qu'ils peuvent résister aux contraintes opérationnelles et maintenir la sécurité du véhicule.
- Inspection des soudures. Inspecter les soudures des châssis et des panneaux de carrosserie des véhicules, en s'assurant qu'elles sont exemptes de défauts et qu'elles peuvent résister aux contraintes opérationnelles.
Meilleures pratiques pour le ressuage
Pour garantir l'efficacité et la fiabilité du ressuage, il est essentiel de suivre les meilleures pratiques.
Ces lignes directrices permettent de maximiser la précision des contrôles par ressuage et de minimiser les risques associés au processus de contrôle.
1. Formation et certification adéquates
- Personnel qualifié. Veillez à ce que le contrôle par ressuage soit effectué par des techniciens formés et certifiés. Il est essentiel qu'ils soient certifiés par des organismes reconnus tels que l'American Society for Nondestructive Testing (ASNT) ou des organisations équivalentes. Un personnel correctement formé est plus à même de réaliser des inspections précises et d'interpréter correctement les résultats.
- Formation continue. Encourager l'éducation et la formation continues afin de tenir les techniciens DPT au courant des dernières techniques, des équipements et des normes industrielles. Il peut s'agir d'ateliers, de séminaires et de cours de renouvellement de la certification. Rester au courant des développements de l'industrie liés au ressuage permet de maintenir des normes élevées de qualité d'inspection.
2. Choix de l'équipement approprié
- Sélection des pénétrants. Choisissez le bon type de pénétrant (visible ou fluorescent, lavable à l'eau, post-émulsifiable ou solvantable) en fonction du matériau et du type d'inspection. Les facteurs à prendre en compte sont la sensibilité, la facilité d'enlèvement et les conditions environnementales. Le choix du pénétrant approprié garantit une détection optimale des défauts et une facilité d'utilisation.
- Sélection du nettoyeur. Utiliser des nettoyants appropriés pour éliminer les contaminants de la surface avant et après l'application du pénétrant. Un nettoyage efficace est essentiel pour obtenir des résultats d'essai précis, car il permet au pénétrant de pénétrer correctement dans les défauts.
- Sélection du développeur. Sélectionnez le type de révélateur approprié (poudre sèche, à base d'eau ou non aqueux) pour répondre à vos besoins spécifiques en matière d'inspection. Le bon révélateur permet de révéler les défauts en attirant le pénétrant et en l'étalant sur la surface pour une meilleure visibilité.
3. Préparation de la surface
- Nettoyer les surfaces. Nettoyez soigneusement la surface du matériau que vous inspectez afin d'éliminer tous les contaminants tels que la saleté, la graisse, l'huile et la peinture. Les contaminants peuvent empêcher le pénétrant de pénétrer dans les défauts et affecter la visibilité des indications. Un nettoyage adéquat garantit des résultats précis et fiables.
- Surfaces lisses. Veillez à ce que la surface soit lisse et exempte de tout revêtement susceptible d'entraver le processus d'inspection. Les surfaces lisses améliorent l'efficacité de l'application du pénétrant et du révélateur, ce qui permet d'obtenir des indications plus claires.
4. Procédures d'inspection
- Procédures opérationnelles standard (POS). Élaborer et respecter des modes opératoires normalisés détaillés pour chaque type de contrôle par ressuage. Les modes opératoires normalisés garantissent la cohérence, la rigueur et la conformité aux exigences réglementaires. Elles fournissent un guide étape par étape pour la réalisation des inspections, contribuant ainsi à maintenir des normes élevées.
- Application contrôlée. Appliquer le pénétrant uniformément sur la surface et laisser un temps d'attente suffisant pour que le pénétrant pénètre dans tous les défauts qui brisent la surface. Une application contrôlée et un temps de séjour approprié sont essentiels pour que le pénétrant pénètre efficacement dans tous les défauts.
- Élimination de l'excès de pénétrant. Retirer soigneusement l'excès de pénétrant de la surface sans perturber le pénétrant à l'intérieur des défauts. Cette étape est essentielle pour éviter les fausses indications et garantir des résultats précis.
- Demande du développeur. Appliquer le révélateur uniformément pour faire sortir le pénétrant des défauts et les rendre visibles pour l'inspection. Une application correcte du révélateur améliore la visibilité des défauts et facilite une interprétation précise.
5. Conditions d'inspection
- Un éclairage adéquat. Veillez à ce que les conditions d'éclairage soient appropriées pour l'inspection. Utilisez une lumière visible pour les inspections avec des pénétrants visibles et une lumière UV pour les inspections avec des pénétrants fluorescents. Un éclairage adéquat est essentiel pour détecter et interpréter avec précision les indications.
- Contrôle environnemental. Effectuez les inspections dans un environnement contrôlé afin d'éviter toute contamination et de garantir des résultats cohérents. La température, l'humidité et la propreté de la zone d'inspection peuvent affecter les résultats des tests.
6. Enregistrement et analyse des données
- Documentation systématique. Enregistrer et documenter systématiquement les données d'inspection, y compris l'emplacement, la taille et le type des défauts. Une documentation précise permet de suivre l'état des composants dans le temps et fournit des informations précieuses pour les inspections futures.
- Logiciel avancé. Utilisez des logiciels d'analyse de données avancés qui permettent d'améliorer l'interprétation des résultats, de générer des rapports détaillés et de stocker efficacement les dossiers d'inspection. Les outils numériques permettent de rationaliser le processus d'inspection et d'en améliorer la précision.
7. Entretien régulier des équipements
- Contrôles de routine. Effectuer l'entretien régulier et les contrôles de routine du matériel de ressuage pour s'assurer qu'il est en bon état de fonctionnement. Il s'agit notamment d'inspecter les flacons pulvérisateurs, les cuves d'immersion, les lampes UV et d'autres outils pour vérifier qu'ils ne sont pas usés ou endommagés.
- Calibrage. Étalonner régulièrement le matériel d'inspection conformément aux directives du fabricant et aux normes industrielles afin d'en préserver la précision et la fiabilité. L'étalonnage garantit que l'équipement fonctionne correctement et fournit des résultats cohérents.
8. Protocoles de sécurité
- Équipement de protection. Veillez à ce que les techniciens portent un équipement de protection approprié, tel que des gants, des lunettes de sécurité et des vêtements de protection, afin de les protéger contre l'exposition aux produits chimiques utilisés dans le pénétrant et le révélateur. Le matériel de protection permet d'éviter le contact avec la peau et l'inhalation de substances potentiellement nocives.
- Manipulation sûre des produits chimiques. Respectez les procédures de manipulation sûre des produits chimiques, y compris le stockage, l'utilisation et l'élimination appropriés. Une manipulation correcte minimise les risques pour la santé et l'impact sur l'environnement.
- Ventilation. Effectuez les inspections dans des zones bien ventilées afin d'éviter l'accumulation de vapeurs provenant des pénétrants, des révélateurs et des nettoyants. Une bonne ventilation réduit le risque d'inhalation de vapeurs dangereuses.
9. Respect des règlements
- Normes réglementaires. Veiller au respect de l'ensemble des normes et lignes directrices réglementaires applicables au ressuage. Il s'agit notamment d'obtenir les certifications nécessaires et d'adhérer aux meilleures pratiques du secteur. La conformité garantit que les inspections respectent les normes de sécurité et de qualité requises.
- Inspections et audits. Effectuer des inspections et des audits réguliers pour vérifier la conformité avec les protocoles de sécurité et les exigences réglementaires. Remédier rapidement à tout problème identifié afin de maintenir un environnement d'inspection sûr et conforme.