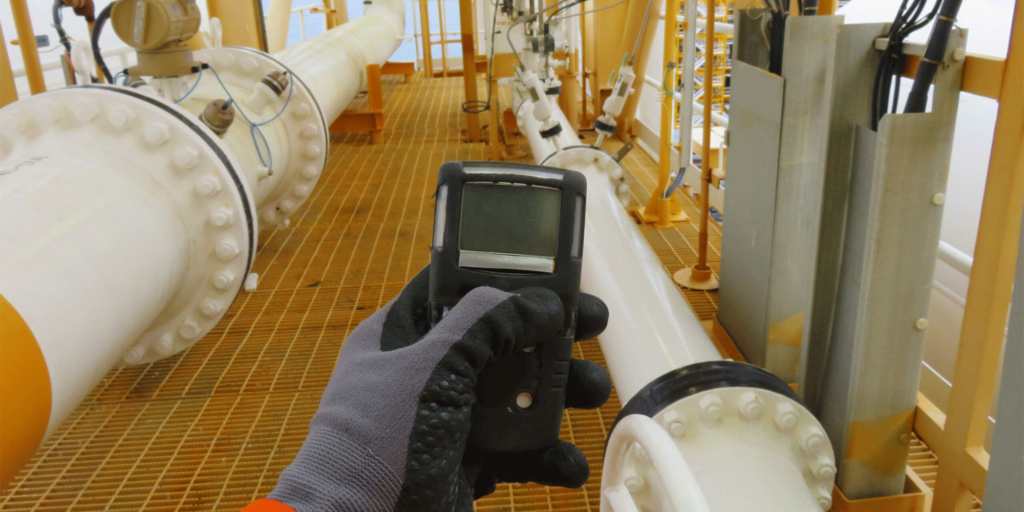
Article
How Toxic Air Monitoring is Used in the Oil & Gas Industry
Toxic air monitoring is essential in the oil and gas industry for ensuring worker safety, environmental protection, and operational efficiency.
By detecting harmful airborne contaminants, toxic air monitors play a critical role in maintaining safe working conditions and preventing health hazards.
This guide explores the types of toxic air monitors used, common contaminants detected, their applications, and the benefits they provide.
What Is Toxic Air Monitoring?
Toxic air monitoring involves the use of specialized equipment to detect and measure the concentration of hazardous substances in the air. These monitors can identify various toxic gasses and volatile organic compounds (VOCs) that pose significant risks to human health and safety.
[Related read: What Is the Hierarchy of Control?]
The primary purpose of toxic air monitoring is to ensure that air quality remains within safe limits, protecting both workers and the environment.
How Toxic Air Monitors Are Used in the Oil & Gas Industry
In the oil and gas industry, toxic air monitors are indispensable tools for ensuring the safety of workers, protecting the environment, and maintaining operational efficiency. They are used extensively across various stages of oil and gas exploration, production, refining, and transportation.
Here’s how toxic air monitors are used in different applications within the industry:
- Drilling Rigs. Toxic air monitors detect harmful gasses like hydrogen sulfide (H₂S) and benzene during drilling operations. Early detection of these gasses is crucial for preventing health hazards and ensuring the safety of workers on the rig.
- Production Facilities. Continuous monitoring of toxic air contaminants in production areas helps detect leaks and prevent accidental releases. This ensures that production processes remain safe and efficient, protecting workers and equipment from exposure to harmful substances.
- Refineries. In refineries, toxic air monitoring systems are essential for detecting a variety of hazardous gasses, including VOCs and hydrogen sulfide. These systems ensure safe processing operations by providing real-time alerts to prevent potential hazards and exposure to toxic substances.
- Pipeline Monitoring. Toxic air monitors are used to detect leaks of hazardous gasses along pipelines, preventing explosions and environmental contamination. Monitoring pipelines helps maintain the integrity of the transportation infrastructure and ensures the safety of surrounding areas.
- Storage Tanks. Monitoring the area around storage tanks for toxic gas leaks is crucial to prevent fire hazards and ensure containment. Toxic air monitors help maintain the safety and integrity of storage facilities, protecting both workers and the environment.
- Confined Space Entry. Portable and personal toxic air monitors are essential for ensuring the safety of workers entering confined spaces such as tanks, vessels, and underground storage areas. These monitors provide real-time monitoring of air quality, ensuring safe working conditions in hazardous environments.
- Maintenance & Spot-Checks. During maintenance activities, portable toxic air monitors are used for spot-checks to ensure that air quality remains within safe limits. This is particularly important in areas where concentrations of toxic gasses might fluctuate due to maintenance work.
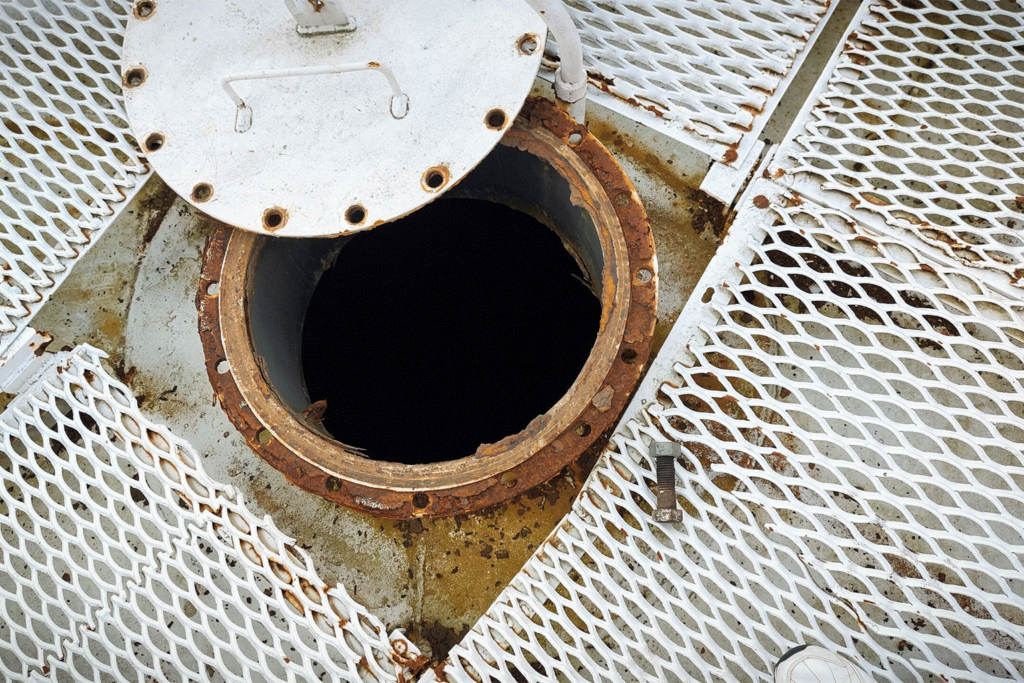
Key Benefits of Using Toxic Air Monitors in the Oil & Gas Industry
Toxic air monitors offer numerous benefits in the oil and gas industry, contributing significantly to safety, operational efficiency, regulatory compliance, and environmental protection. Here are the key advantages of using toxic air monitors in this sector:
- Enhanced Safety. Early detection of hazardous airborne contaminants helps prevent accidents and protects workers from exposure to toxic and combustible gasses.
- Operational Efficiency. Continuous monitoring allows for the early identification of leaks and issues, reducing downtime and maintenance costs, and ensuring smooth operations.
- Regulatory Compliance. Toxic air monitors ensure adherence to safety regulations and standards set by agencies such as OSHA and EPA, helping companies avoid fines and legal issues.
- Environmental Protection. Detecting and controlling toxic air contaminants helps prevent the release of harmful substances into the environment, protecting air quality and ecosystems.
What Types of Toxic Air Monitors Are Used in the Oil and Gas Industry?
In the oil and gas industry, various types of toxic air monitors are employed to ensure comprehensive safety monitoring and operational efficiency. Here’s an overview of the different toxic air monitors used and their specific applications:
- Fixed Toxic Air Monitors. Fixed toxic air monitors are permanently installed at strategic locations within facilities such as refineries, drilling rigs, and production sites. These devices continuously monitor for the presence of hazardous contaminants and provide real-time alerts, enabling quick responses to potential dangers.
- Portable Toxic Air Monitors. Portable toxic air monitors are handheld devices carried by personnel to detect concentrations of harmful gasses in various areas. They are used for spot-checks, confined space entry, and during maintenance activities. These monitors provide flexibility and mobility, allowing workers to ensure safety across different locations.
- Personal Toxic Air Monitors. Personal toxic air monitors are worn by individual workers, providing continuous monitoring of their immediate environment. These devices offer real-time alerts to the wearer if dangerous gas levels are detected, enhancing personal safety during operations.
- Remote Sensing Technologies. Methods such as satellite imaging and ground-based LiDAR (Light Detection and Ranging) systems are used for large-scale monitoring of air quality. These technologies provide comprehensive data on air pollution levels over extensive areas.
What are the Most Common Contaminants Detected by Toxic Air Monitors in the Oil & Gas Industry?
Toxic air monitors are essential for identifying and monitoring various hazardous airborne contaminants in the oil and gas industry.
Here are the most common contaminants detected by these devices and their significance:
- Hydrogen Sulfide (H₂S). A highly toxic and flammable gas with a characteristic rotten egg smell.
- Sources: Natural gas extraction, petroleum refining, and production facilities.
- Health Effects: Can cause irritation of the eyes, nose, and throat, headaches, dizziness, and in high concentrations, it can be fatal.
- Monitoring Importance: Continuous monitoring is critical due to its potential for causing severe health effects and its explosiveness.
- Volatile Organic Compounds (VOCs). A group of organic chemicals that easily become vapors or gases, including benzene, toluene, xylene, and ethylbenzene.
- Sources: Emissions from production and refining processes, storage tanks, and transportation of petroleum products.
- Health Effects: Can cause eye, nose, and throat irritation, headaches, loss of coordination, nausea, and damage to the liver, kidney, and central nervous system. Some VOCs are known to cause cancer.
- Monitoring Importance: Detecting and controlling VOC emissions helps ensure compliance with environmental regulations and protects worker health.
- Benzene (C₆H₆). A colorless or light yellow liquid at room temperature with a sweet odor, classified as a volatile organic compound (VOC).
- Sources: Present in crude oil, gasoline, and used in the production of plastics, resins, and synthetic fibers.
- Health Effects: Long-term exposure can cause bone marrow damage, blood disorders like leukemia, and other cancers. Short-term exposure can cause drowsiness, dizziness, rapid heart rate, headaches, tremors, confusion, and unconsciousness.
- Monitoring Importance: Continuous monitoring is essential due to its carcinogenic properties and the potential for long-term health impacts.
- Carbon Monoxide (CO). A colorless, odorless, and tasteless gas produced by incomplete combustion of carbon-containing fuels.
- Sources: Engine exhaust, flaring, and combustion processes in production facilities.
- Health Effects: Can cause headache, dizziness, weakness, nausea, vomiting, chest pain, and confusion. High levels can lead to loss of consciousness and death.
- Monitoring Importance: Essential for preventing CO poisoning, ensuring safe working environments, and avoiding health hazards associated with this toxic gas.
- Sulfur Dioxide (SO₂). A toxic gas with a pungent, irritating smell.
- Sources: Combustion of sulfur-containing fuels, oil refining, and gas processing facilities.
- Health Effects: Can cause respiratory problems, irritation of the eyes, and exacerbation of cardiovascular diseases. Long-term exposure can lead to lung diseases.
- Monitoring Importance: Monitoring is crucial for preventing respiratory health issues and environmental pollution, as SO₂ can contribute to acid rain formation.
- Nitrogen Dioxide (NO₂). A reddish-brown gas with a characteristic sharp, biting odor.
- Sources: Combustion processes, including engines, heating, and flaring.
- Health Effects: Can cause lung irritation, decrease lung function, and increase the risk of respiratory infections.
- Monitoring Importance: Important for protecting respiratory health and ensuring air quality compliance.
What Are the Major Air Pollutants Monitored and Regulated by the EPA?
The Environmental Protection Agency (EPA) monitors and regulates several key air pollutants to ensure air quality and protect public health.
These pollutants, known as criteria air pollutants, are regulated under the Clean Air Act due to their potential to cause harm to human health and the environment.
The EPA tracks these pollutants using the Air Quality Index (AQI), which provides a standardized way of reporting air quality.
The six criteria air pollutants monitored and regulated by the EPA are:
- Ground-Level Ozone (O₃): Formed when pollutants emitted by cars, power plants, industrial boilers, refineries, and other sources chemically react in the presence of sunlight. Ozone at ground level can cause respiratory problems and other health issues.
- Particulate Matter (PM10 and PM2.5): Consists of tiny particles suspended in the air, which can be inhaled and cause severe respiratory and cardiovascular problems. PM10 refers to particles with diameters of 10 micrometers or less, while PM2.5 refers to particles with diameters of 2.5 micrometers or less.
- Carbon Monoxide (CO): A colorless, odorless gas produced by burning fossil fuels. High levels of carbon monoxide can interfere with the body’s ability to transport oxygen, leading to various health issues, including cardiovascular problems.
- Sulfur Dioxide (SO₂): Emitted from fossil fuel combustion at power plants and other industrial processes. Sulfur dioxide can cause respiratory problems and contribute to the formation of acid rain, which can harm ecosystems.
- Nitrogen Dioxide (NO₂): Part of a group of highly reactive gasses known as nitrogen oxides (NOx), emitted from vehicles, power plants, and off-road equipment. Nitrogen dioxide can cause respiratory issues and contribute to the formation of ground-level ozone and fine particulate pollution.
- Lead (Pb): Historically common in gasoline and paint, lead emissions have significantly decreased due to regulatory efforts. However, lead still poses a risk in areas with industrial emissions and can cause severe health problems, particularly in children.
These pollutants are also monitored using the AQI, which includes ground-level ozone, particulate matter, carbon monoxide, sulfur dioxide, and nitrogen dioxide.
The AQI helps communicate how polluted the air currently is or how polluted it is forecasted to become, providing a standardized way of reporting air quality and helping people understand what actions they need to take to protect their health based on air quality levels.
MFE’s Oil & Gas Toxic Air Monitoring Picks
Selecting the right equipment for toxic air monitoring in the oil and gas industry is crucial for ensuring worker safety and operational efficiency.
Here are three top picks from MFE for reliable and efficient air quality monitoring: the RAE Systems ppbRAE 3000, the RAE Systems QRAE 3, and the Rae Systems MultiRAE Lite.
RAE Systems ppbRAE 3000
The RAE Systems ppbRAE 3000 is a highly sensitive portable photoionization detector (PID) used extensively in the oil and gas industry for detecting volatile organic compounds (VOCs) at parts per billion (ppb) levels.
Here are its key features and benefits:
- High Sensitivity Detection Levels. The ppbRAE 3000 can detect VOCs down to parts per billion (ppb) levels, making it extremely sensitive and ideal for detecting even the smallest leaks.
- Instant Feedback. Provides real-time data on VOC concentrations, allowing for immediate action in case of a leak or hazardous condition.
- Record Keeping. Capable of storing a large amount of data, which can be downloaded for analysis and record-keeping, ensuring compliance with regulatory requirements.
- Rugged Design. Built to withstand harsh industrial environments, making it suitable for use in the oil and gas industry.
- User-Friendly Interface. Simple to operate, with a large display and intuitive controls, ensuring that personnel can use it effectively with minimal training.
- Lightweight and Portable. Easy to carry and use in various locations, including remote and confined spaces.
RAE Systems QRAE 3
The RAE Systems QRAE 3 is a versatile, portable multi-gas detector used extensively in the oil and gas industry to ensure worker safety and operational efficiency.
Here are its key features and benefits:
- Multi-Gas Detection Capabilities. The QRAE 3 can simultaneously monitor up to four gasses, including oxygen (O₂), hydrogen sulfide (H₂S), carbon monoxide (CO), and combustible gasses (LEL).
- Flexibility. This makes it versatile for a wide range of applications in the oil and gas industry.
- Immediate Alerts. Provides real-time data and alarms if gas concentrations exceed safe levels, enabling quick response to hazardous conditions.
- Visual, Audible & Vibrating Alarms. Ensure that alerts are noticeable even in noisy or low-visibility environments.
- Data Recording. The device logs data for review and analysis, helping with compliance and reporting requirements.
- Wireless Communication. Some models offer wireless capabilities for remote monitoring and integration with central safety systems.
- Rugged Design. Built to withstand harsh industrial environments, ensuring reliable performance in tough conditions.
- Compact and Lightweight. Easy to carry and use, making it ideal for personal protection and portable monitoring.
- User-Friendly Interface. Simple operation with an intuitive interface, making it easy for workers to use with minimal training.
- Long Battery Life. Extended battery life ensures continuous operation during long shifts or extended use.
RAE Systems MultiRAE Lite
The RAE Systems MultiRAE Lite is a versatile and reliable multi-gas detector widely used in the oil and gas industry to ensure worker safety and operational efficiency.
Here are its key features and benefits:
- Multi-Gas Detection Capabilities. The MultiRAE Lite can simultaneously monitor up to five gasses, including oxygen (O₂), hydrogen sulfide (H₂S), carbon monoxide (CO), volatile organic compounds (VOCs), and combustible gasses (LEL).
- Multi-Gas Detection Capabilities. The MultiRAE Lite can simultaneously monitor up to five gasses, including oxygen (O₂), hydrogen sulfide (H₂S), carbon monoxide (CO), volatile organic compounds (VOCs), and combustible gasses (LEL).
- Versatility. Suitable for a broad spectrum of applications in the oil and gas sector. Immediate
- Alerts. Delivers real-time data and alarms if gas levels exceed safety thresholds, allowing for prompt action in hazardous situations.
- Visual, Audible & Vibrating Alarms. Ensure alerts are noticeable, even in noisy or low-visibility environments.
- Data Logging. Records data for subsequent review and analysis, aiding in compliance and reporting.
- Wireless Communication. Certain models feature wireless capabilities for remote monitoring and integration with central safety systems.
- Durable Design. Engineered to endure harsh industrial conditions, guaranteeing reliable performance.
- Compact & Lightweight. Easy to transport and use, making it perfect for personal safety and portable monitoring.
- User-Friendly Interface. Intuitive design allows for simple operation, requiring minimal training for workers.
- Extended Battery Life. Long-lasting battery ensures uninterrupted operation during lengthy shifts or extended use.
Final Thoughts on Toxic Air Monitoring in the Oil & Gas Industry
Toxic air monitors are indispensable tools in the oil and gas industry, providing critical safety and operational benefits by monitoring and detecting hazardous airborne contaminants.
Whether you are a service provider or asset owner, understanding the applications and benefits of toxic air monitors can lead to safer, more efficient, and compliant operations.
By integrating toxic air monitoring technology into daily operations, the oil and gas industry can achieve greater safety, efficiency, and environmental stewardship.