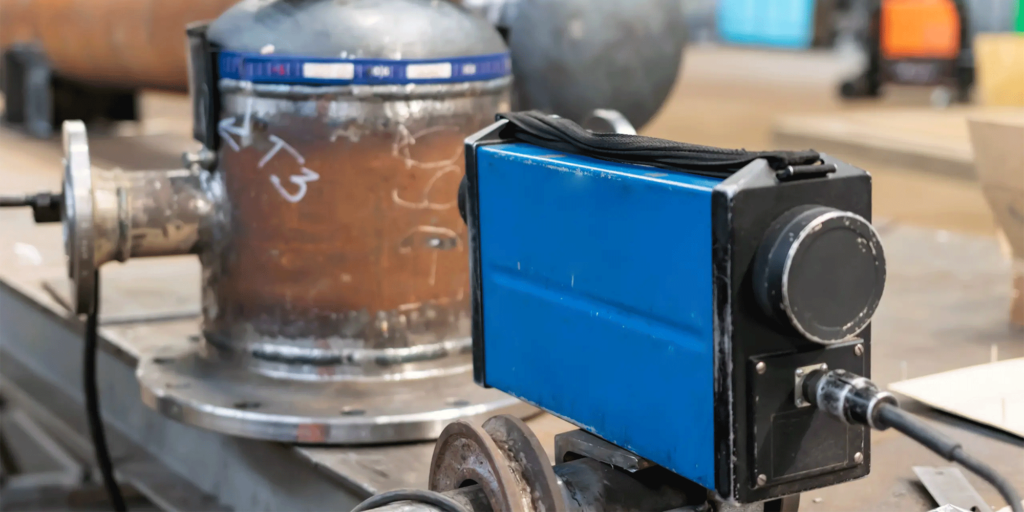
Guide
Industrial Radiography: An In-Depth Guide [New for 2025]
Industrial Radiography is an NDT method that uses X-rays or gamma rays to inspect the internal structure of materials and components, allowing inspectors to find defects hidden from the naked eye.
Alternate phrases for industrial radiography include:
- Radiographic testing (RT)
- X-ray inspection
- Radiographic examination
- Radiographic inspection
- Radiographic analysis
Industrial radiography is particularly effective for identifying and evaluating hidden flaws during inspections, including:
- Crack formations. Detects internal cracks in metals, plastics, and composites that are not visible to the naked eye, ensuring structural integrity.
- Corrosion. Identifies areas of corrosion within pipelines, tanks, and other critical components, allowing for timely maintenance and repair.
- Void detection. Reveals voids, inclusions, and other internal defects in castings and welds that could compromise the strength and reliability of the material.
- Weld quality. Evaluates the quality of welds by detecting imperfections such as porosity, lack of fusion, and slag inclusions.
- Thickness measurement. Measures the thickness of materials and components, verifying that they meet specified tolerances and safety standards.
- Internal assemblies. Inspects the internal structure of complex assemblies and machinery to ensure proper construction and function.
This article delves into the fundamentals of industrial radiography, exploring the tools and techniques inspectors use to do it, the different types of industrial radiography, and the scenarios where this method is most beneficial.
Have a specific topic in mind? Use the menu to the right to jump around within this guide.
What Is Industrial Radiography?
In industrial radiography, inspectors use ionizing radiation from X-rays or gamma rays to examine the internal structure of materials and components.
Doing this can reveal hidden flaws, measure thickness, and ensure the integrity of various structures without causing any damage.
Principles of Industrial Radiography
The fundamental principle of industrial radiography involves passing ionizing radiation through a material and capturing the resulting image on a radiographic film or digital detector.
The density and composition of the material affect how much radiation passes through it, creating a contrast image that highlights internal features and potential defects.
Industrial radiography relies on two types of radiation:
- X-rays. Produced by X-ray tubes, these rays are suitable for inspecting thinner or less dense materials. X-rays have high energy levels and can penetrate materials to varying depths, making them ideal for detecting surface and subsurface defects.
- Gamma rays. Generated by radioactive isotopes such as Iridium-192 or Cobalt-60, gamma rays have higher penetrating power than X-rays, making them suitable for inspecting thicker or denser materials. Gamma radiography is often used in field applications where portability is a concern.
Here are the key steps involved in industrial radiography for either type of radiation:
1. Preparation and Setup
- Selection of radiographic source. Choose the appropriate radiographic source (X-ray or gamma ray) based on the material thickness, density, and inspection requirements.
- Positioning the object. Place the object to be inspected between the radiographic source and the detector (film or digital sensor). Ensure that the object is properly aligned to capture the desired area.
2. Exposure
- Radiation emission. Activate the radiographic source to emit radiation. X-ray machines generate X-rays, while gamma ray sources such as iridium-192 or cobalt-60 emit gamma rays.
- Penetration of radiation. The emitted radiation penetrates the object. Different materials and defects within the object will absorb or attenuate the radiation to varying degrees.
3. Detection and Imaging
- Capture of radiation. The detector (radiographic film or digital sensor) captures the radiation that passes through the object. The amount of radiation reaching the detector varies based on the material’s density and the presence of defects.
- Image formation. The variations in radiation intensity are recorded by the detector, forming an image that reveals the internal structure of the object. Areas with higher density or defects appear as darker or lighter regions on the image.
4. Development and Processing (for Film Radiography)
- Film development. If using radiographic film, process the film in a darkroom to develop the image. This involves chemical processing to reveal the captured radiographic image.
- Digital processing. For digital radiography, the captured data is processed by software to create a digital image that can be analyzed on a computer.
5. Interpretation and Analysis
- Image evaluation. Inspectors analyze the radiographic image to identify and characterize defects such as cracks, voids, inclusions, and corrosion. The contrast and clarity of the image help in determining the type, size, and location of defects.
- Documentation. Document the findings, including the location and severity of defects, and prepare a report detailing the inspection results.
Advantages of Industrial Radiography
- Non-destructive. Like other NDT methods, industrial radiography does not alter or damage the material being inspected, allowing for repeated testing and continued use of the inspected item.
- High penetration. Both X-rays and gamma rays can penetrate deeply into materials, providing detailed images of internal structures that are not accessible through other inspection methods.
- Versatility. Industrial radiography can be used on a wide range of materials, including metals, composites, ceramics, and plastics, making it a versatile tool for various industries.
- Detailed imaging. The technique provides high-resolution images that can reveal even the smallest defects, such as cracks, voids, and inclusions, ensuring thorough inspection and quality control.
Limitations of Industrial Radiography
- Safety concerns. The use of ionizing radiation requires stringent safety measures to protect operators and the environment from exposure. Proper training and regulatory compliance are essential.
- Cost and time. Radiographic inspections can be more expensive and time-consuming than other NDT methods, especially when high-resolution imaging or large-scale inspections are required.
- Access limitations. To obtain clear images, there must be access to both sides of the material, which can be challenging in certain applications.
Industrial Radiography Tools
Industrial radiography relies on a variety of specialized tools and equipment to generate, control, and detect ionizing radiation. These tools are essential for performing accurate and reliable inspections.
Below is a categorized list of industrial radiography tools, along with relevant details about each type.
1. Radiation Sources
I. X-ray Tubes are devices that produce X-rays by accelerating electrons and colliding them with a metal target.
- How they work. The interaction of high-speed electrons with the target material generates X-rays, which are directed towards the material being inspected.
- Applications. Suitable for inspecting thinner or less dense materials, such as welds in piping and thin metal sheets.
II. Gamma Ray Sources are radioactive isotopes, such as Iridium-192 or Cobalt-60, that emit gamma rays.
- How they work. The isotopes naturally emit gamma radiation, which is directed towards the material being inspected. The high energy of gamma rays allows for the inspection of thicker or denser materials.
- Applications. Ideal for field applications and inspecting thicker materials, such as large metal castings and heavy machinery components.
2. Detection and Imaging Devices
I. Radiographic Film is traditional photographic film that captures the image formed by the transmitted radiation.
- How it works. When exposed to radiation, the film darkens in proportion to the amount of radiation received, creating a contrast image that reveals internal structures and defects.\
- Applications. Used in both X-ray and gamma ray radiography for high-resolution imaging.
II. Digital Radiography Detectors are electronic devices that capture digital images of the transmitted radiation.
- How they work. Digital detectors convert the incoming radiation into electronic signals, which are processed to create digital images. These images can be enhanced, stored, and analyzed using computer software.
- Applications. Increasingly replacing traditional film due to faster processing times, better image quality, and easier data storage and sharing.
III. Computed Radiography (CR) Plates are imaging plates coated with photostimulable phosphors that capture the radiographic image.
- How they work. After exposure to radiation, the plates are scanned with a laser to produce a digital image. The plates can be reused, making CR a cost-effective alternative to traditional film.
- Applications. Used in various industries for detailed imaging and digital storage capabilities.
3. Exposure Control Equipment
I. Collimators are devices that shape and direct the radiation beam, reducing scatter and improving image quality.
- How they work. Collimators are placed in front of the radiation source to narrow the beam to the desired size and shape.
- Applications. Used in both X-ray and gamma ray radiography to focus the radiation on the area of interest, enhancing image clarity.
II. Shielding and Safety Equipment are protective barriers and devices that minimize radiation exposure to operators and the environment.
- How they work. Lead aprons, gloves, and barriers absorb and block radiation, while remote controls and automated systems allow operators to conduct inspections from a safe distance.
- Applications. Essential for ensuring safety during radiographic inspections, complying with regulatory standards, and protecting personnel from harmful radiation.
4. Image Processing and Analysis Software
I. Radiographic Image Analysis Software is computer software designed to enhance, analyze, and interpret radiographic images.
- How it works. These programs offer tools for adjusting contrast, measuring dimensions, identifying defects, and generating detailed inspection reports.
- Applications. Used to improve the accuracy and efficiency of radiographic inspections, enabling better decision-making and documentation.
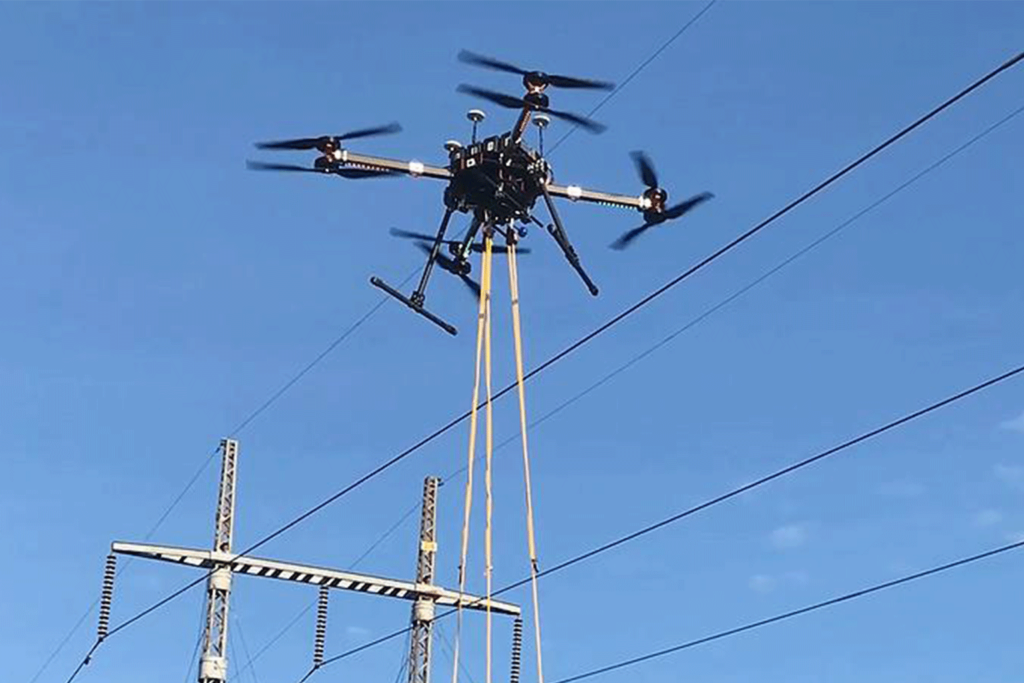
Types of Industrial Radiography
Industrial radiography encompasses several techniques, each tailored to specific inspection needs and applications. These methods vary in their approach and the type of radiation used.
Here are the main types of industrial radiography:
1. X-ray Radiography
This method uses X-rays generated by X-ray tubes to inspect materials and components.
- How it works. X-rays penetrate the material and are absorbed at different rates depending on the material’s density and thickness. The transmitted rays are captured on a radiographic film or digital detector to create an image.
- Applications. X-ray radiography is commonly used for inspecting welds, detecting cracks in metal parts, and examining electronic components for defects.
2. Gamma Radiography
Gamma radiography utilizes gamma rays emitted by radioactive isotopes such as Iridium-192 or Cobalt-60.
- How it works. Gamma rays, which have high penetration power, pass through the material and expose a radiographic film or digital detector on the other side, forming an image based on the differential absorption.
- Applications. Ideal for field inspections and thick materials, gamma radiography is used in the oil and gas industry for pipeline inspections and in the construction industry for inspecting large concrete structures.
3. Computed Radiography (CR)
A digital imaging process that uses photostimulable phosphor plates to capture radiographic images.
- How it works. The CR plates are exposed to radiation and then scanned with a laser to produce a digital image. The plates can be reused, making this method cost-effective and environmentally friendly.
- Applications. CR is widely used in industrial settings where digital storage and image manipulation capabilities are advantageous, such as in manufacturing and aerospace inspections.
4. Digital Radiography (DR)
An advanced form of radiography that uses digital detectors to capture images directly, bypassing the need for film or intermediate scanning steps.
- How it works. Digital detectors convert the X-ray or gamma radiation into electronic signals, which are then processed to create high-resolution digital images.
- Applications. DR is used in industries that require fast turnaround times and high image quality, such as automotive, aerospace, and electronics manufacturing.
5. Real-Time Radiography (RTR)
A technique that allows for the continuous capture and display of radiographic images in real-time.
- How it works. Using digital detectors and high-speed processing, RTR systems provide live imaging, enabling immediate analysis and decision-making.
- Applications. RTR is employed in dynamic inspections where immediate feedback is crucial, such as in the inspection of moving parts, weld monitoring, and assembly line quality control.
6. Computed Tomography (CT)
An advanced radiographic technique that produces three-dimensional images by combining multiple two-dimensional X-ray images taken from different angles.
- How it works. CT scanners rotate around the object, capturing cross-sectional images that are reconstructed into a detailed 3D model using computer algorithms.
- Applications. CT is used for complex inspections requiring detailed internal views, such as in the aerospace industry for turbine blade inspection and in the medical device industry for detailed component analysis.
When Is Industrial Radiography Required?
Industrial radiography is essential in various scenarios to ensure the quality, safety, and reliability of materials and structures.
Here are key situations when industrial radiography is required:
1. Quality Control and Assurance
- Manufacturing processes. During production, industrial radiography is used to verify that materials and components meet specified quality standards, detecting internal defects like cracks, voids, and inclusions.
- Incoming material inspection. Radiography is employed to inspect raw materials before they are used in production, ensuring they meet the required specifications and are defect-free.
2. Weld Inspection
- Weld integrity. Radiography is crucial for inspecting welds to detect internal flaws such as lack of fusion, porosity, and cracks, ensuring the structural integrity of welded joints.
- Post-Weld Heat Treatment (PWHT). After heat treatment, welds are inspected using radiography to ensure no new defects have formed and that the welds maintain their integrity.
3. Structural Integrity Assessment
- Construction and infrastructure. Radiography is used to assess the structural integrity of buildings, bridges, and other infrastructure, detecting internal flaws and weaknesses that could compromise safety.
- Aerospace industry. In aerospace, radiography inspects critical components such as wings, fuselage, and engine parts to ensure they meet the high safety standards required for aviation.
4. Preventive Maintenance
- Scheduled inspections. Industrial radiography is part of routine maintenance schedules to monitor the condition of critical components and infrastructure, enabling early detection of potential issues and preventing unexpected failures.
- Condition monitoring. Continuous or periodic radiographic inspections provide valuable data on the health of components under operational conditions, predicting their remaining service life.
5. Safety Compliance
- Regulatory requirements. Many industries are subject to stringent safety regulations that mandate regular radiographic inspections. Compliance with these regulations ensures components and structures meet safety standards, reducing the risk of accidents.
- Certification and accreditation. Radiography is often required for certification purposes, such as obtaining pressure vessel and pipeline certifications from regulatory bodies.
6. Research and Development
- Material characterization. In research and development, radiography helps characterize new materials, studying their properties and behavior under different conditions, which is vital for developing advanced materials with enhanced performance.
- Prototype testing. Radiography is used to evaluate prototypes, identifying any flaws or weaknesses that need to be addressed before full-scale production.
Industrial Radiography Applications by Industry
Industrial radiography finds applications across a wide range of industries, providing critical insights into the internal structures and integrity of materials and components.
Here are some key applications of industrial radiography, highlighting its versatility and importance:
Oil and Gas
In the oil and gas industry, industrial radiography is crucial for maintaining the integrity of pipelines, storage tanks, and other critical infrastructure.
- Pipeline inspections. Radiography is used to detect corrosion, cracks, and other defects in pipelines, ensuring their integrity and preventing leaks or ruptures that could lead to environmental disasters.
- Tank inspections. Storage tanks are inspected using radiography to detect wall thinning due to corrosion, preventing potential leaks and ensuring safe storage of hazardous materials.
- Weld quality control. Radiography is employed to inspect welds in pipelines and other infrastructure, ensuring they meet stringent quality standards and can withstand operational stresses.
Power Generation
In the power generation industry, industrial radiography is essential for maintaining the reliability and efficiency of power plants and related infrastructure.
- Turbine inspections. Radiography is used to inspect turbine blades and other components for cracks and other defects that could lead to failures and costly downtime.
- Boiler and pressure vessel inspections. Radiography helps in detecting corrosion, cracking, and other issues in boilers and pressure vessels, ensuring their safe operation.
- Nuclear power plants. Radiography is crucial for inspecting reactor components and other critical infrastructure in nuclear power plants, ensuring they meet stringent safety standards.
Manufacturing
In the manufacturing industry, industrial radiography is essential for ensuring product quality and reliability.
- Quality assurance. Radiography is used to inspect raw materials, intermediate products, and final assemblies for internal defects such as cracks, voids, and inclusions. This ensures that only defect-free products reach the customer.
- Weld inspections. Manufacturers use radiography to inspect welded joints in metal structures, pipelines, and pressure vessels. Detecting internal flaws like lack of fusion or porosity helps maintain the structural integrity and safety of welded products.
- Component verification. Radiography is employed to verify the internal geometry and integrity of complex components such as castings and forgings, ensuring they meet design specifications.
Aerospace
The aerospace industry relies heavily on industrial radiography to maintain the safety and performance of aircraft components.
- Aircraft structural inspections. Radiography is used to inspect critical structural components, including wings, fuselage sections, and engine parts, for internal defects. Ensuring these components are free of flaws is vital for flight safety.
- Composite material inspections. Aerospace manufacturers use radiography to inspect composite materials for delaminations, voids, and other defects that could compromise the performance of aircraft parts.
- Maintenance and overhaul. During routine maintenance and overhauls, radiography helps detect fatigue cracks, corrosion, and other damage in aircraft components, ensuring they remain airworthy.
Construction
The construction industry uses industrial radiography to ensure the safety and durability of buildings, bridges, and other infrastructure.
- Structural component inspections. Radiography is used to inspect concrete, steel, and other structural materials for internal defects that could compromise the safety and stability of buildings and bridges.
- Reinforcement verification. Radiography helps in detecting flaws in reinforcing bars (rebar) within concrete structures, ensuring the overall strength and durability of the construction.
- Weld inspections. Radiography is used to inspect welded joints in steel structures, ensuring they meet safety standards and can support the required loads.
Automotive
The automotive industry employs industrial radiography to ensure the quality and safety of vehicle components.
- Component inspections. Radiography is used to inspect engine blocks, suspension components, and other critical parts for internal defects, ensuring they meet safety and performance standards.
- Weld inspections. Radiography is employed to inspect welds in vehicle frames and body panels, ensuring they are free from defects and can withstand operational stresses.
- Material thickness measurement. Radiography helps in measuring the thickness of materials used in vehicle manufacturing, such as sheet metal, ensuring they meet design specifications and tolerances.
Medical Device Manufacturing
In the medical device industry, industrial radiography ensures the quality and safety of critical healthcare products.
- Component inspections. Radiography is used to inspect internal components of medical devices, such as implants and surgical instruments, for defects that could affect their performance and safety.
- Assembly verification. Manufacturers use radiography to verify the correct assembly of complex medical devices, ensuring they function as intended.
- Material integrity. Radiography helps ensure that materials used in medical devices meet the necessary quality standards and are free from internal defects.
Best Practices for Industrial Radiography
Here are the top best practices for industrial radiography to ensure its effectiveness and maintain safety while doing it.
1. Proper Training and Certification
- Qualified personnel. Ensure that radiographic inspections are conducted by trained and certified technicians. Certification from recognized bodies such as the American Society for Nondestructive Testing (ASNT) or equivalent organizations is essential.
- Continuous education. Encourage ongoing education and training to keep technicians updated on the latest techniques, equipment, and industry standards. This can include workshops, seminars, and certification renewal courses.
2. Appropriate Equipment Selection
- Radiation sources. Choose the right type of radiation source based on the material and type of inspection. Factors to consider include the thickness, density, and composition of the material.
- Detection devices. Use appropriate detection devices, such as digital radiography detectors or radiographic film, to capture high-quality images that accurately reflect the internal structure of the material.
- Collimators and filters. Employ collimators and filters to shape and control the radiation beam, reducing scatter and improving image quality.
3. Safety Protocols
- Radiation protection. Implement stringent safety measures to protect operators and the environment from radiation exposure. This includes using lead aprons, gloves, and barriers, as well as ensuring proper shielding of the radiation source.
- Safety training. Provide comprehensive safety training for all personnel involved in radiographic inspections, emphasizing the importance of following safety protocols and regulatory requirements.
- Radiation monitoring. Use dosimeters and other radiation monitoring devices to track exposure levels and ensure they remain within safe limits.
4. Inspection Procedures
- Standard operating procedures (SOPs). Develop and adhere to detailed SOPs for each type of radiographic inspection. SOPs ensure consistency, thoroughness, and compliance with regulatory requirements.
- Surface preparation. Ensure that surfaces to be inspected are clean and free from contaminants such as dirt, grease, and paint, which can affect the quality of the radiographic image.
- Proper positioning. Position the radiation source, material, and detector accurately to obtain clear and detailed images of the area of interest.
5. Image Processing and Analysis
- Image enhancement. Use image processing software to enhance the quality of radiographic images, adjusting contrast and brightness to highlight defects and internal features.
- Accurate interpretation. Ensure that technicians are skilled in interpreting radiographic images to accurately identify and characterize defects. This includes understanding the nuances of different types of defects and their impact on material integrity.
- Documentation and reporting. Maintain detailed records of radiographic inspections, including images, measurements, and descriptions of any detected defects. Generate clear and concise reports that are easy to understand for both technical and non-technical stakeholders.
6. Regular Equipment Maintenance
- Routine checks. Perform regular maintenance and routine checks on radiographic equipment to ensure it is in good working condition. This includes inspecting radiation sources, detectors, and other components for wear and damage.
- Calibration. Regularly calibrate equipment according to manufacturer guidelines and industry standards to maintain accuracy and reliability.
- Software updates. Keep software for digital radiography systems and image analysis up-to-date to take advantage of the latest features and improvements.
7. Compliance with Regulations
- Regulatory standards. Ensure compliance with all relevant regulatory standards and guidelines for the use of ionizing radiation in industrial radiography. This includes obtaining necessary licenses and permits.
- Inspections and audits. Conduct regular inspections and audits to verify compliance with safety protocols and regulatory requirements. Address any identified issues promptly to maintain a safe and compliant inspection environment.