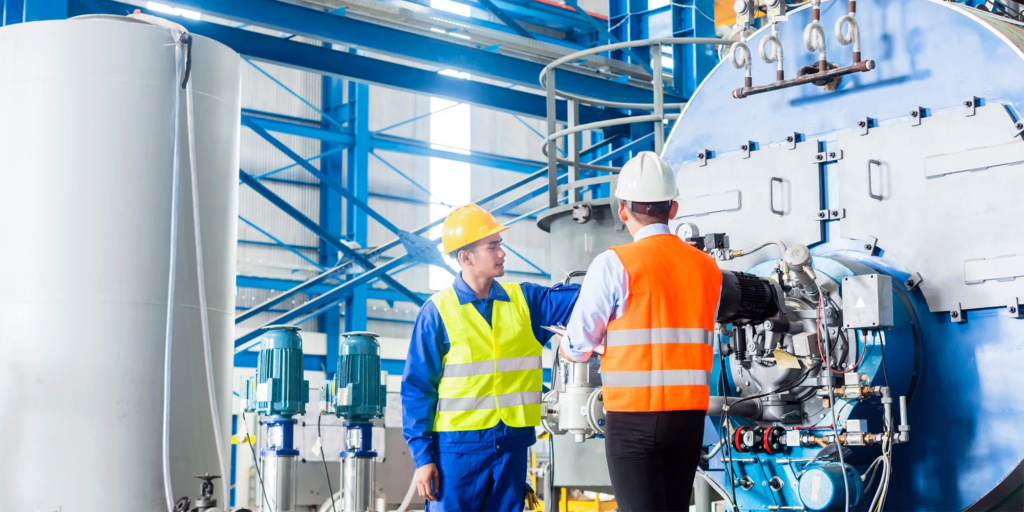
Guide
Acoustic Emission Testing: An In-Depth Guide [New for 2025]
Acoustic Emission Testing (AET) is an NDT method that monitors the release of energy in the form of transient elastic waves—also known as acoustic emissions—from materials under stress in order to detect flaws in them for inspection purposes.
Alternate phrases for AET include:
- Acoustic testing
- Acoustic monitoring
- Acoustic analysis
- Acoustic signal detection
- Acoustic emission analysis
Acoustic emission testing is particularly effective for identifying and evaluating defects during inspections, including:
- Crack formations
- Corrosion
- Fiber breakage in composites
AET is used extensively in industries where maintaining the integrity and safety of critical components is essential, including aerospace, civil engineering, power generation, and manufacturing (we cover top applications for acoustic testing by industry below).
This article provides an in-depth overview of acoustic emission testing, exploring the tools and techniques used, the various types of AET methods, and the inspection scenarios where it’s most useful.
Have a specific topic in mind? Use the menu to the right to jump around within this guide.
What Is Acoustic Emission Testing?
Acoustic emission testing detects and analyzes the high-frequency acoustic waves emitted by materials when they undergo deformation or stress.
Acoustic emissions are generated by various defects, including crack formation, plastic deformation, and phase transformations, providing valuable information about the integrity and behavior of the material under load.
This information is crucial for identifying defects in assets, helping inspectors find potential issues before they develop into severe problems.
And its usefulness isn’t limited to just a few industries. The list of materials for which AET can be used includes metal, concrete, or ceramics, alloys, composites, and many others, so almost any industry can benefit from its ability to detect the early stages of defect formation and monitor damage progression in real-time.
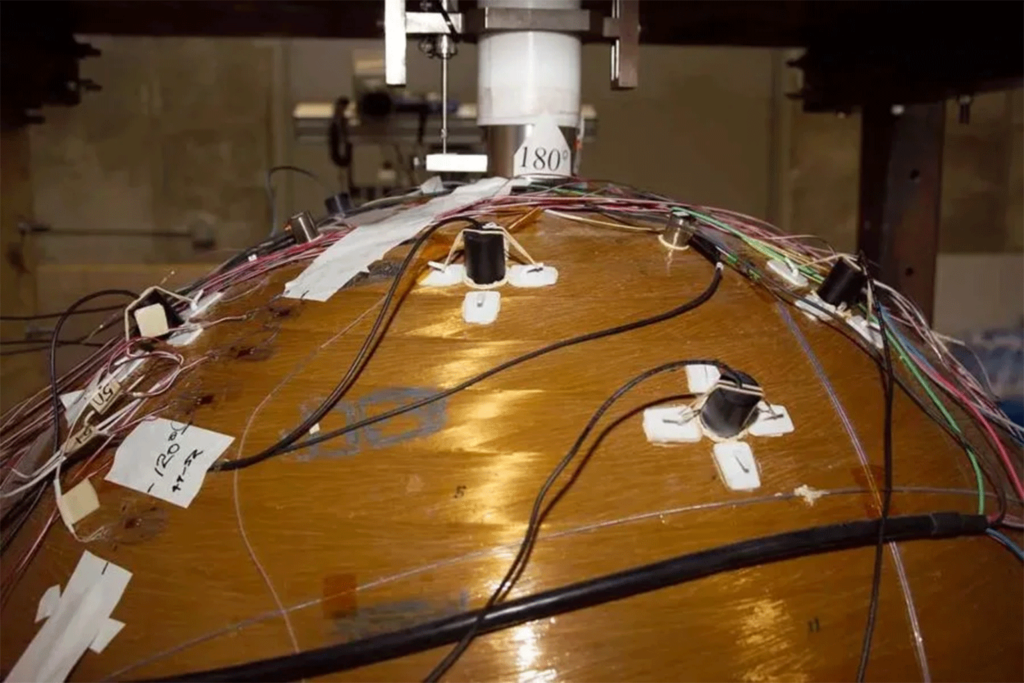
Principles of Acoustic Emissions Testing
The fundamental principle of AET is based on the detection and analysis of transient elastic waves produced by the rapid release of energy from localized sources within a material.
Put simply, inspectors monitor acoustic waves in a material then analyze them to identify anomalies, indicating the possible presence of a flaw. These waves could be present on their own (i.e., passive acoustic testing, which requires no intervention) or could be introduced by stressing a material (i.e., active acoustic testing, which requires an intervention from the inspector to create acoustic waves).
Below is a short step-by-step for acoustic emission testing, following the active model. (Note that for passive acoustic testing the process would start at step three, when inspectors use sensors to begin detecting acoustic.)
1. Stress Application
Inspectors stress the material they’re inspecting using means like mechanical loading or thermal cycling.
2. Wave Generation
As the material undergoes stress it deforms, emitting acoustic waves due to processes like crack initiation, crack growth, fiber breakage, or corrosion.
3. Wave Detection
Inspectors attach sensors, typically piezoelectric transducers, to the material’s surface to detect acoustic waves. These sensors convert mechanical waves into electrical signals, which can be interpreted to identify the presence of defects.
4. Signal Processing
Inspectors amplify the converted electrical signals, filtering and processing them to extract meaningful information—i.e., where is there a potential defect? and what is the nature of the defect?—about the source and characteristics of the acoustic emissions.
5. Data Analysis
Inspectors process the data then analyze it to identify the type, location, and severity of defects, allowing them to conduct real-time monitoring and assessments of the material’s condition.
Advantages of Acoustic Emissions Testing
- Real-time monitoring. AET provides continuous, real-time monitoring of materials and structures, enabling early detection of defects and damage progression.
- Sensitivity. AET is highly sensitive to the initiation and growth of defects, often detecting flaws that are not visible using other NDT methods.
- Non-invasive. The technique is non-invasive and doesn’t require contact with the internal structure of the material, making it suitable for a wide range of applications.
- Broad applicability. AET can be used for several types of materials, including metals, composites, ceramics, and polymers.
Limitations of Acoustic Emissions Testing
- Complex interpretation. You need special training to do AET—the interpretation of acoustic emission signals requires skilled operators with extensive training and experience.
- Environmental noise. Background noise and environmental factors can interfere with the detection of acoustic emissions, potentially impacting the accuracy of the test. (As noted above, this method is highly sensitive!)
- Limited range. The effectiveness of AET decreases with distance from the source of the acoustic emission, requiring strategic placement of sensors for comprehensive coverage.
- Material dependency. The type of material you’re using for acoustic testing matters—quality of results can vary depending on the material properties and the type of defects you’re monitoring.
Acoustic Emission Testing vs. Ultrasonic Testing
Acoustic Emission Testing (AET) and Ultrasonic Testing (UT) are both valuable non-destructive testing (NDT) methods used to assess the integrity of materials and structures.
Despite their similarities, these techniques differ significantly in their principles, applications, and advantages. Understanding these differences helps in selecting the appropriate method for your specific inspection needs.
Acoustic Emission Testing (AET)
- How it works. AET monitors the release of transient elastic waves (acoustic emissions) generated by the rapid release of energy from localized sources within a material under stress. Sensors placed on the material’s surface detect these emissions, which are then analyzed to locate and characterize defects such as cracks and delaminations.
- Detection mechanism. AET can be passive or active, either relying on the material itself to generate signals when it experiences stress or introducing stress, which then leads to changes in acoustic waves, allowing inspectors to identify issues like material deformation or crack propagation.
Ultrasonic Testing (UT)
- How it works. UT uses high-frequency sound waves that are introduced into the material via a transducer. These sound waves travel through the material and reflect off internal features such as flaws or boundaries. The reflected waves are detected by the transducer or another sensor, and the amplitude of the echoes and other data are analyzed to determine the location, size, and nature of internal defects.
- Detection mechanism. UT is active, requiring an external source to generate ultrasonic waves that are then transmitted into the material.
Choosing Between AET and UT
The choice between Acoustic Emission Testing and Ultrasonic Testing depends on the specific requirements of the inspection task.
- AET is ideal for real-time monitoring and detecting active damage, making it suitable for long-term structural health monitoring.
- UT, on the other hand, is preferred for detailed flaw detection, thickness measurements, and applications where precise quantitative data is required.
Acoustic Emission Testing Tools
Inspectors use a huge range of specialized tools and equipment for acoustic monitoring.
These tools are designed to detect, amplify, and analyze the acoustic waves generated by materials under stress.
Below are the most common types of acoustic emission testing tools. We’ve organized these tools into seven categories, with specific types listed for each one (some categories only have one type).
1. AET Sensors
I. Piezoelectric transducers are AET sensors that convert mechanical waves into electrical signals.
- How they work. When an acoustic wave reaches the piezoelectric transducer, it generates an electrical signal proportional to the wave’s amplitude and frequency.
- Applications. These sensors are widely used in AET for detecting a wide range of acoustic emissions from various materials and structures.
II. Fiber optic sensors are AET sensors that use optical fibers to detect acoustic emissions.
- How they work. Acoustic waves cause slight changes in the optical fiber’s properties, which are detected and converted into electrical signals.
- Applications. Used in environments where electromagnetic interference might affect piezoelectric sensors, such as in high-voltage areas or where radio frequency interference is present.
2. Preamplifiers
I. Preamplifiers are devices that amplify the weak signals generated by the sensors before they are processed.
- How they work. Preamplifiers increase the amplitude of the signals to a level suitable for further processing and analysis without adding significant noise.
- Applications. Essential for ensuring that the detected acoustic emissions are strong enough to be accurately analyzed, especially in large or noisy environments.
3. Data Acquisition Systems
I. Data Acquisition Systems collect and digitize the electrical signals from the sensors.
- How they work. These systems convert the analog signals from the sensors into digital data that can be processed by computers. They often include features like filtering, sampling, and multiplexing.
- Applications. Used to gather and store data from multiple sensors simultaneously, allowing for comprehensive analysis of acoustic emissions across large structures.
4. Signal Processing Software
I. Signal processing software is software designed to analyze the digitized acoustic emission signals.
- How it works. The software filters noise, extracts features, and performs signal analysis to identify the source and characteristics of acoustic emissions. It may also use algorithms for event detection, pattern recognition, and data visualization.
- Applications. Essential for interpreting the complex data generated during AET, providing insights into defect location, type, and severity.
5. Waveguides
I. Waveguides are devices that transmit acoustic waves from hard-to-reach areas to sensors.
- How they work. Waveguides channel the acoustic emissions from the source to the sensor, ensuring that signals from inaccessible or harsh environments can still be detected.
- Applications. Used in structures where direct sensor placement is not possible, such as inside pipes, tanks, or high-temperature environments.
6. Mounting Accessories
I. Mounting accessories are components like adhesives, clamps, and magnetic holders used to attach sensors to the material surface.
- How they work. These accessories ensure that sensors are securely and correctly positioned to detect acoustic emissions effectively.
- Applications. Critical for maintaining consistent sensor placement during long-term monitoring and ensuring accurate data collection.
7. Calibration Equipment
I. Calibration equipment are tools and reference materials used to calibrate sensors and data acquisition systems.
- How they work. Calibration equipment ensures that the AET system is accurately measuring acoustic emissions, often using known reference signals or materials with predetermined properties.
- Applications. Regular calibration is necessary to maintain the accuracy and reliability of AET inspections, especially in critical applications.
Types of Acoustic Emission Testing
Although the term “acoustic emission testing” generally refers to a way to do non-destructive testing, the truth is that there are a lot of different ways you can do it.
Each of these approaches is tailored to specific inspection needs and applications, with nuanced differences that depend on the type of stress applied to the material and the nature of the acoustic emissions detected.
Each type of acoustic testing offers unique advantages and is suited to different applications. And that’s why it’s so important to have an experienced AET operator doing this work, since they’ll be able to identify the best approach for the specific inspection, helping you get the best test results to inform your maintenance efforts.
Here are the main types of acoustic emissions testing:
1. Passive Acoustic Emissions Testing
No intervention is used—this method monitors acoustic emissions generated by the material under its normal operational conditions.
- How it works. Inspectors attach sensors to the material, and acoustic emissions are passively detected as the material undergoes natural stress and deformation.
- Applications. Commonly used for continuous monitoring of structures like bridges, pressure vessels, and pipelines to detect crack growth, corrosion, and other defects without interrupting their operation.
2. Active Acoustic Emissions Testing
Intervention is used—this method introduces stress to the material to induce acoustic emissions.
- How it works. The material is subjected to controlled mechanical, thermal, or pressure stress to stimulate the release of acoustic emissions, which are then detected by the sensors.
- Applications. Used in laboratory settings and during scheduled maintenance to evaluate a material’s response to stress and identify potential defects.
3. Burst Acoustic Emissions Testing
No intervention is used—monitoring sensors detect high-energy acoustic emissions caused by sudden events, such as crack formation or sudden fracture.
- How it works. Sensors detect brief, high-amplitude acoustic signals that occur when significant structural changes or failures happen.
- Applications. Ideal for monitoring critical structures where sudden failures could have catastrophic consequences, such as in aerospace components and high-pressure systems.
4. Continuous Acoustic Emissions Testing
No intervention is used—sensors conduct continuous monitoring of low-level acoustic emissions over an extended period.
- How it works. Sensors continuously collect data on acoustic emissions, which are analyzed to detect gradual changes or trends in the material’s behavior.
- Applications. Used for long-term health monitoring of infrastructures like bridges, dams, and large buildings to track the progression of defects and ensure structural integrity.
5. Modal Acoustic Emissions Testing
Intervention may or may not be used, since this method is about how the data is processed, not collected—combines acoustic testing data with modal analysis to study the dynamic response of materials to stress.
- How it works. Inspectors take acoustic emission data and correlate it with the material’s modal parameters (natural frequencies, mode shapes) to gain insights into the material’s dynamic behavior.
- Applications. Used in research and development to study the mechanical properties and failure mechanisms of advanced materials, like composites and alloys.
When Is Acoustic Emission Testing Required?
Acoustic Emission Testing (AET) is essential in several maintenance scenarios to ensure the quality, safety, and reliability of materials and structures.
Here are the main situations that call for acoustic emission testing:
1. Quality Control and Assurance in Manufacturing
- Production processes. During manufacturing, AET is used to monitor the integrity of materials and components, detecting defects such as cracks, delaminations, and inclusions. This ensures that only defect-free products reach the customer.
- Incoming material inspection. Inspecting raw materials before use in production, ensuring they meet the required specifications and are free from defects.
2. Structural Health Monitoring
- Infrastructure monitoring. AET is vital for the continuous monitoring of large infrastructure such as bridges, dams, and buildings. It helps in early detection of structural issues, such as crack growth and material degradation, ensuring the safety and longevity of these structures.
- Aerospace structures. In the aerospace industry, AET is used to monitor the structural integrity of aircraft components. This includes detecting fatigue cracks, delaminations in composite materials, and other critical defects that could compromise flight safety.
3. Pressure Vessel and Pipeline Monitoring
- Pressure vessel integrity. AET is crucial for monitoring the integrity of pressure vessels in industries such as oil and gas, chemical processing, and power generation. It helps in detecting leaks, crack growth, and other issues that could lead to catastrophic failures.
- Pipeline monitoring. Monitoring pipelines for defects such as corrosion, cracking, and third-party damage. Continuous monitoring helps prevent leaks and ruptures, ensuring the safe transportation of fluids and gasses.
4. Preventive Maintenance and Scheduled Inspections
- Routine maintenance. AET is part of regular maintenance schedules to monitor the condition of critical components and infrastructure. This helps in early detection of potential issues, preventing unexpected failures and downtime.
- Condition monitoring. Continuous or periodic AET inspections enable the monitoring of components under operational conditions, providing valuable data on their health and predicting their remaining service life.
5. Research and Development
- Material characterization. In research and development, AET helps characterize new materials, studying their properties and behavior under different conditions. This information is vital for developing advanced materials with enhanced performance.
- Prototype testing. AET is used to evaluate prototypes, identifying any flaws or weaknesses that need to be addressed before full-scale production.
6. Safety Compliance and Regulatory Requirements
- Regulatory standards. Many industries are subject to stringent safety regulations that mandate regular acoustic emissions testing. Compliance with these regulations ensures that components and structures meet safety standards, reducing the risk of accidents.
- Certification and accreditation. AET is often required for certification purposes, such as obtaining pressure vessel and pipeline certifications from regulatory bodies.
The Top 5 Industries that Rely on Acoustic Emission Testing + Specific Applications They Use
As we mentioned earlier, inspectors can use AET on a huge array of materials, including metals, concrete, ceramics, and many more.
This means it can be used in almost every industry you can imagine that relies on machinery or infrastructure made from these materials.
Here are the top five industries that use AET, with specific applications covered for each one.
1. Oil and Gas Industry
In the oil and gas industry, acoustic emissions testing is vital for maintaining the safety and reliability of pipelines and other downstream, midstream, and upstream infrastructure.
- Pipeline monitoring. AET is used to detect corrosion, cracking, and other defects in pipelines, ensuring their integrity and preventing leaks or ruptures that could lead to environmental disasters.
- Pressure vessel monitoring. AET monitors pressure vessels for signs of cracking, leakage, and other defects that could lead to catastrophic failures.
- Well integrity. Acoustic emissions testing helps assess the integrity of wells, detecting issues such as casing leaks, formation fractures, and cement bond failures.
2. Power Generation
In power generation, acoustic emissions testing is essential for maintaining the integrity of critical components in power plants.
- Steam generator monitoring. AET is used to monitor steam generators for signs of cracking, corrosion, and other defects that could affect their performance and safety.
- Turbine blade inspection. Detecting early signs of damage in turbine blades, such as cracks and material degradation, ensuring their efficient and safe operation.
- Transformer and generator monitoring. Monitoring transformers and generators for signs of internal defects, such as winding discharges and core delaminations, ensuring their reliability and performance.
3. Manufacturing Industry
In the manufacturing industry, acoustic emissions testing is crucial for ensuring product quality and reliability.
- Quality assurance. AET is used to inspect raw materials, intermediate products, and final assemblies for internal and surface defects such as cracks, voids, and inclusions. This ensures that only defect-free products reach the customer.
- Machined part inspection. Inspecting machined parts for defects, ensuring they meet design specifications and tolerances.
- Weld inspection. Detecting defects in welds, such as cracks and lack of fusion, ensuring the structural integrity of welded joints.
4. Civil Engineering and Infrastructure
In civil engineering, acoustic emissions testing plays a crucial role in ensuring the integrity and safety of large structures.
- Bridge monitoring. AET is used to continuously monitor bridges for signs of structural damage such as crack growth, corrosion, and material degradation. This monitoring helps maintain the safety and longevity of critical infrastructure.
- Dam safety. Monitoring the integrity of dams, detecting potential issues such as cracking and seepage that could lead to catastrophic failures.
- Building health monitoring. Monitoring high-rise buildings and other structures for signs of structural stress and damage, ensuring their safety and stability over time.
5. The Aerospace Industry
The aerospace industry relies heavily on acoustic emission testing to maintain the safety and performance of aircraft components.
- Aircraft structural monitoring. AET is used to monitor critical structural components such as wings, fuselage sections, and landing gear for defects like fatigue cracks and delaminations. Ensuring these components are free of flaws is vital for flight safety.
- Composite material inspection. AET is essential for inspecting composite materials used in aircraft construction, detecting issues such as fiber breakage, matrix cracking, and delamination.
- Engine components. AET helps monitor engine components, detecting early signs of damage or failure that could compromise engine performance and safety.
Best Practices for Acoustic Emission Testing
As we’ve covered, AET is incredibly sensitive. For that reason, it’s crucial to follow industry best practices to make sure you do it effectively and produce reliable results,
These guidelines can help maximize the accuracy of acoustic inspections and minimize potential risks associated with the testing process.
1. Proper Training and Certification
- Qualified personnel. Ensure that acoustic emissions testing is conducted by trained and certified technicians. Certification from recognized bodies such as the American Society for Nondestructive Testing (ASNT) or equivalent organizations is essential.
- Continuous education. Encourage ongoing education and training to keep technicians updated on the latest techniques, equipment, and industry standards. This can include workshops, seminars, and certification renewal courses.
2. Appropriate Equipment Selection
- Sensor selection. Choose the right type of sensors based on the material and type of inspection. Factors to consider include sensitivity, frequency response, and environmental compatibility.
- Instrumentation. Use appropriate data acquisition systems and preamplifiers that match the inspection requirements. Advanced instruments with multi-channel capabilities and digital interfaces can provide more detailed and accurate results.
- Calibration standards. Employ calibration standards and reference materials that match the expected acoustic emission characteristics. Regularly calibrate the equipment to maintain accuracy.
3. Surface Preparation
- Clean surfaces. Ensure that the surfaces where sensors are attached are clean and free from contaminants such as dirt, grease, and paint. Contaminants can impede the transmission of acoustic waves and affect the accuracy of the inspection.
- Smooth surfaces. Smooth out rough or uneven surfaces as much as possible to improve sensor coupling and signal quality.
4. Inspection Procedures
- Standard operating procedures (SOPs). Develop and adhere to detailed SOPs for each type of acoustic emissions inspection. SOPs ensure consistency, thoroughness, and compliance with regulatory requirements.
- Proper sensor placement. Strategically place sensors to ensure comprehensive coverage of the material or structure. Use waveguides if necessary to reach inaccessible areas.
- Signal interpretation. Technicians should be skilled in interpreting acoustic emissions signals to accurately identify and characterize defects. It’s essential that these operators can understand the nuances of signal waveforms, frequencies, and amplitudes.
5. Data Acquisition and Analysis
- Real-time monitoring. Use data acquisition systems that provide real-time monitoring and display of acoustic emissions signals, allowing for immediate detection and analysis of defects.
- Data recording. Record and store inspection data systematically. This helps in tracking the condition of components over time and provides valuable information for future inspections.
- Advanced software. Use advanced data analysis software that can enhance signal interpretation, generate detailed reports, and store inspection records efficiently.
6. Regular Equipment Maintenance
- Routine checks. Perform regular maintenance and routine checks on acoustic emissions testing equipment to ensure it is in good working condition. This includes inspecting sensors, preamplifiers, and data acquisition systems for wear and damage.
- Calibration. Regularly calibrate equipment according to manufacturer guidelines and industry standards to maintain accuracy and reliability.
- Software updates. Keep software for data acquisition and analysis up-to-date to take advantage of the latest