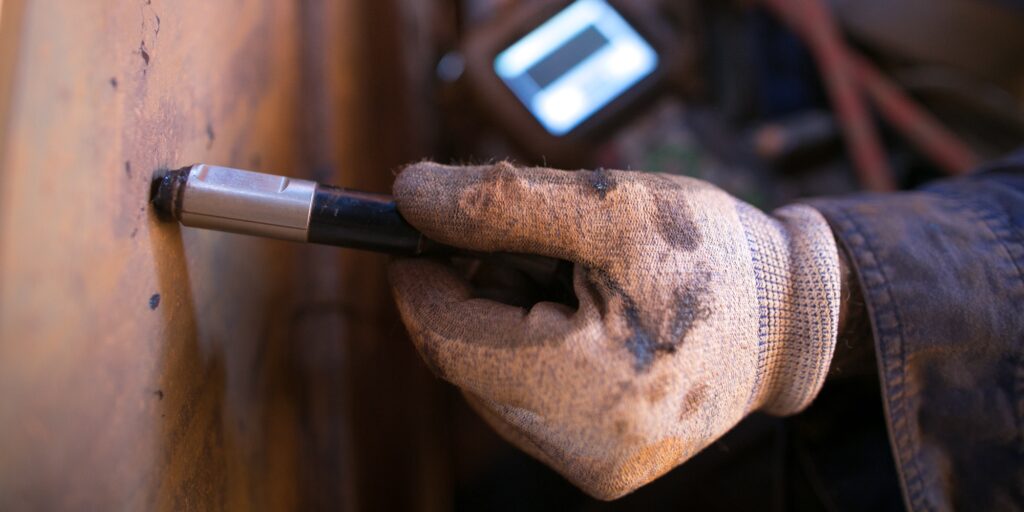
Guide
Ultrasonic Thickness Gauges: Top Options on the Market & More
Ultrasonic thickness gauges use high-frequency sound waves to measure the thickness of materials. Inspectors use them in the field for quality control, maintenance, and safety inspections.
→ Jump to ultrasonic thickness gauges for rent and sale.
The versatility of ultrasonic thickness gauges makes them useful for a wide range of professionals. In storage tank inspections, inspectors can use them to measure thick materials, while in pipe inspections, inspectors can use a gauge with a smaller probe to measure the pipe wall’s thickness.
Ultrasonic thickness gauges are also commonly called:
- Ultrasonic thickness measuring instruments
- Ultrasonic thickness testers
- Thickness testers
- Ultrasonic metal thickness gauges
- Ultrasonic wall thickness gauges
These thickness testers are an important NDT tool, providing accurate and reliable measurements without damaging the test object. Their ability to take thickness measurements without harming the object being tested makes them ideal for assessing material integrity, identifying corrosion, and ensuring quality control in various applications.
Common applications for ultrasonic thickness gauges include:
- Inspecting pipelines and piping systems for corrosion and wear
- Measuring the thickness of storage tanks and pressure vessels
- Checking the integrity of structural steel and welds
- Assessing material thickness in manufacturing processes
- Measuring the thickness of ship hulls, aircraft components, and other transportation equipment
In this guide to ultrasonic thickness testers we’ll cover the top options on the market, how inspectors use them, tips on maintenance, and more. Use the menu on the right to jump round, or keep reading for the full guide.
Ultrasonic Thickness Gauges for Rent & Sale [New for 2025]
Looking to rent or buy an ultrasonic thickness tester?
Here are the top models on the market right now.
1. Cygnus 1 Ultrasonic Thickness Gauge
The Cygnus 1 is a rugged and reliable ultrasonic thickness gauge designed for accurate measurements in harsh environments.
Its durable construction and easy-to-use interface make it ideal for a variety of industrial applications.
- Key features. Durable, reliable, easy to use
- Applications. Intrinsically safe ultrasonic inspections, NDT in harsh environments, measuring metal thickness.
- Assets. Storage tanks, distillation columns, ship hulls, vessels, and more.
Learn more about the Cygnus 1.
2. Echo 9 Ultrasonic Thickness Gauge
The Echo 9 is a versatile ultrasonic thickness gauge, offering high accuracy and a user-friendly interface.
This device is designed for precision thickness measurements in various industrial settings.
- Key features. High accuracy, user-friendly, versatile applications.
- Applications. Corrosion testing, measuring thickness in metals and materials, proof indications found with eddy current or magnetic flux leakage (MFL).
- Assets. For use in assets like ship hulls, storage tanks, pipelines, cooling towers, and more.
3. GE DMS 2 Ultrasonic Thickness Gauge
The GE DMS 2 is an advanced ultrasonic thickness gauge, providing a wide range of features for complex inspection needs, including data logging and A-scan functionality.
- Key features. Data logging, A-scan, advanced inspection capabilities.
- Applications. Measuring thickness in metals and materials, non-invasive inspections for structural integrity, corrosion testing.
- Assets. Distillation columns, cooling towers, bridges, ship hulls, and more.
Learn more about the GE DMS 2.
4. Olympus 38DL PLUS Ultrasonic Thickness Gauge
The Olympus 38DL PLUS is a sophisticated ultrasonic thickness gauge, offering comprehensive measurement capabilities with advanced features like data logging and through-paint measurement options.
- Key features. Data logging, through-paint measurement, advanced features
- Uses. Portable tool for non-destructive material testing, digital ultrasonic thickness gauge for metal surfaces, corrosion monitoring in industrial environments.
- Assets. Pipelines, storage tanks, distillation columns, cooling towers, and more.
Learn more about the Olympus 38DL PLUS.
Drones with Ultrasonic Thickness Gauges
Here are two of the only drones in the world that carry an ultrasonic thickness tester.
Elios 3 with UT Payload
Ideal for: Inspecting indoor industrial assets like pipelines, tanks, and pressure vessels in confined spaces, eliminating the need for physical access or scaffolding.
Drone Highlights
- Made for indoor inspections. Specifically designed for indoor confined spaces and challenging environments.
- Collision tolerance. Unique cage design allows for safe contact and navigation in complex spaces.
- Stabilized flight. Provides stable and accurate positioning for precise measurements.
- High-resolution Video: Offers real-time visual feedback in addition to UT data.
Ultrasonic Thickness Sensor Highlights:
- Integrated UT system. Seamless integration of the UT sensor with the drone’s systems.
- Precise measurements. Delivers accurate thickness measurements in hard-to-reach areas.
- Contact-based measurement. Uses a contact transducer for reliable data acquisition.
- Data logging. Ability to record and store measurement data for analysis and reporting.
Voliro T with Ultrasonic NDT Payload
Ideal for: Inspecting large outdoor structures, infrastructure, and complex geometries such as pipelines, storage tanks, bridges, and ship hulls. Can be used in scenarios that require complex maneuvering and the collection of precise UT data on diverse surfaces.
Drone Highlights:
- Versatile multidirectional flight. Capable of 360-degree flight and maneuvering in all directions.
- Advanced stability. Precision control allows for accurate positioning and consistent contact with inspection surfaces.
- Robust design. Built for demanding industrial applications and harsh environments.
- High payload Capacity. Supports a variety of NDT payloads and sensors.
Ultrasonic Thickness Sensor Highlights:
- Advanced UT technology. High-frequency ultrasonic transducers for detailed material thickness data.
- Flexible contact application. Designed for reliable coupling on various surfaces.
- Real-time monitoring. Provides live data for immediate analysis and decision-making.
- Data integration. Compatible with various software platforms for data storage and analysis.
5 Types of Ultrasonic Thickness Gauges
Ultrasonic thickness gauges come in various types, each designed to meet specific inspection needs.
Understanding the differences between these types can help you choose the right gauge for your application.
1. Basic Ultrasonic Thickness Gauges
Basic ultrasonic thickness gauges are designed for simple, quick thickness measurements.
They typically feature a digital display that shows the current thickness reading. These gauges are often used for routine inspections where basic measurements are sufficient.
- Key features. Simple operation, direct thickness readings, often compact and portable.
- Ideal use cases. Quick checks, general thickness measurements, routine inspections.
2. Data-Logging Ultrasonic Thickness Gauges
Data-logging ultrasonic thickness gauges provide the basic functionality of standard gauges, but also include internal memory for saving measurement data, and typically allow for data export to computers.
Being able to save data on the gauge is convenient for inspectors in the field, and for those inspections that require thorough documentation and data analysis, since it lets you easily archive your data for future review.
- Key features. Internal memory for data storage, data export capabilities, can save hundreds or thousands of measurements.
- Ideal use cases. Inspections that require detailed reporting, audits, quality control processes.
3. Advanced Ultrasonic Thickness Gauges with A-Scan
Advanced ultrasonic thickness gauges with A-scan capabilities provide a graphical representation of the ultrasonic signal.
This can provide additional insights into the material’s structure, such as identifying echoes from layers, corrosion, or other anomalies.
Note: A-scan is beneficial when a high-level view of the material is needed.
- Key features. Graphical A-scan display, enhanced analysis capabilities, more detailed material characterization.
- Ideal use cases. Detailed material analysis, complex inspections, identification of defects.
4. Advanced Ultrasonic Thickness Gauges with B-Scan
B-scan functionality provides a cross-sectional view of the material, created by moving the probe along a line. It’s especially useful for mapping corrosion or material thinning over an area.
These gauges are typically more advanced and offer more detailed inspection results.
- Key features. B-scan cross-sectional view, mapping of material variations, corrosion mapping.
- Ideal use cases. Corrosion mapping, material thinning analysis, detailed area assessments.
5. Coating Thickness Gauges
Some ultrasonic thickness gauges are specifically designed to measure the thickness of coatings on various substrates. These tools are called coating thickness gauges, and they’re important for quality control in various manufacturing and maintenance settings.
Coating thickness gauges typically feature special probes that can differentiate between the coating and substrate layers.
- Key features. Ability to measure coating thickness, special probes for coating measurement, often come with specific standards for coating analysis.
- Ideal use cases. Measuring paint thickness, coating analysis, quality control for coated parts.
Key Features of Ultrasonic Thickness Gauges
In this section we cover the main features of a good thickness tester.
If you’re looking for one right now, or even if you just need a refresher, this section will give you an overview of the criteria to consider when hunting for an ultrasonic thickness gauge.
1. Measurement Range
The measurement range of a thickness gauge determines the minimum and maximum material thickness it can accurately measure.
Choose a gauge with a range that matches the expected thickness of your test materials. For example, some models are designed for thin materials and coatings, while others can measure much thicker materials.
2. Accuracy
The accuracy of a gauge indicates how close its measurements are to the actual thickness. High accuracy is essential for precise inspections. Look for models that offer a low measurement error for reliable results.
3. Probe Type
The type of probe affects the gauge’s ability to measure specific materials and geometries.
Common probe types include single element transducers for general use, and dual element transducers for measuring rough or corroded surfaces. The correct probe can also greatly improve accuracy and sensitivity for different applications.
4. Display
A clear and easy-to-read display is crucial for accurate and efficient inspections.
Look for models with high-resolution screens and backlight options for use in dark or challenging environments. Some gauges also offer color displays or waveform views.
5. Data Logging Capabilities
For inspections that require detailed documentation and analysis, data logging is a key feature.
Gauges with data logging allow users to save measurement data for later review and reporting. Some gauges may also offer connectivity for easy data transfer to computers.
6. Calibration
Proper calibration is key to the reliability of your measurements.
A gauge that has easy-to-use calibration options is an important feature to consider. Look for models that support on-site calibration with reference blocks.
7. Durability and Environmental Protection
Ultrasonic thickness gauges are often used in harsh industrial settings. Look for models with rugged housings that are resistant to dust, water, and impact.
These features directly affect the quality and efficiency of your inspections.
For instance, models with a wide measurement range are suitable for a variety of material thicknesses, while high-accuracy models are important when assessing thin coatings or critical welds.
Industrial Applications for Ultrasonic Thickness Gauges
Ultrasonic thickness gauges are incredibly versatile, and are commonly used across a range of industrial applications.
In quality control, thickness testers are helpful because they can take quick and accurate readings. Or in situations that call for detailed reporting, a UT gauge’s ability to log data is crucial.
Whatever the specific job, a good ultrasonic thickness gauge can provide you with the information you need to maintain material integrity and ensure the safety of your equipment.
Keep reading for some of the most common UT applications.
Pipe and Pipeline Inspections
Ultrasonic thickness gauges are extensively used to monitor pipe wall thickness and identify corrosion, erosion, and other forms of material degradation.
This is critical in industries like oil and gas, where pipeline integrity is paramount. Regular inspections help prevent leaks, ruptures, and costly downtime.
Storage Tank Inspections
Monitoring the thickness of storage tank walls and floors is essential for preventing structural failures.
Ultrasonic gauges provide a non-destructive way to measure the thickness of tank walls and identify corrosion and thinning, ensuring safe and reliable storage of materials.
Pressure Vessel Inspections
In industries like petrochemical and power generation, pressure vessels are used to contain high-pressure fluids and gases.
Regular thickness measurements are crucial for maintaining their integrity and ensuring safety, since thinner walls could lead to a critical failure.
Structural Steel Inspections
Ultrasonic gauges are used in construction and infrastructure to assess the thickness of steel structures, welds, and joints. This helps ensure the structural integrity of buildings, bridges, and other civil engineering projects.
Manufacturing Quality Control
Ultrasonic thickness gauges are essential for verifying material thicknesses in manufacturing processes. This helps ensure that materials meet design specifications and that manufactured parts conform to quality control standards.
Aerospace Component Inspection
In the aerospace industry, ultrasonic gauges are used to measure the thickness of aircraft components, such as fuselage panels, wing structures, and engine parts. These inspections are important for maintaining the safety and reliability of aircraft.
Ship Hull Inspection
Ultrasonic thickness measurements of ship hulls are important to detect corrosion, which is a major concern in maritime environments. Regular inspections help to prevent structural failures and ensure safe operation of vessels.
How to Use an Ultrasonic Thickness Gauge: A Step-by-Step Guide
Using an ultrasonic thickness gauge effectively requires careful preparation and execution.
This step-by-step walks you through the process for capturing accurate and reliable measurements with a thickness tester.
Step 1: Preparation
1. Inspect the gauge. Check the ultrasonic thickness gauge, including the probe, cable, and display, for any signs of damage or wear. Ensure all connections are secure and that the battery is fully charged or that the device is connected to a power source.
2. Select the appropriate probe. Choose the correct probe for the type of material you will be measuring. Single element probes are suitable for general use, while dual element probes work better on rough or corroded surfaces. Refer to your gauge’s manual for guidance.
3. Gather calibration standards. Obtain a set of calibration blocks or reference samples with known thicknesses. This will allow you to calibrate the gauge for accurate measurements of your target materials. Make sure to follow the gauge’s recommended calibration guidelines.
4. Prepare the measurement surface. Clean the area where you will be taking measurements, removing any dirt, grease, paint, or corrosion. A smooth and clean surface is essential for accurate ultrasonic readings. If needed, use a couplant to ensure proper acoustic coupling between the probe and the material.
Step 2: Calibration
1. Access calibration mode. Turn on the ultrasonic thickness gauge and access the calibration settings. Typically, you will use the gauge’s menu to select calibration options.
2. Calibrate at a known point. Begin by calibrating the gauge at one or more known thicknesses. Follow the gauge’s instructions for proper calibration at each standard, and take measurements of the reference standards as instructed by your gauge’s manual.
3. Verify calibration. Take a few measurements of your calibration blocks to ensure the device is calibrated accurately. If the readings are not correct, repeat the calibration procedure or troubleshoot the issue.
Step 3: Measurement
1. Apply couplant. Apply a thin, even layer of couplant to the area where you will be taking a measurement. Couplant ensures proper transmission of sound waves between the probe and the measurement surface.
2. Position the probe. Place the probe firmly and flatly on the surface. Do not apply excessive pressure, and make sure the probe is aligned properly with the material to be measured.
3. Take measurements. Take a measurement by pressing the probe against the test surface. Observe the reading on the gauge display, and wait for the reading to stabilize before taking a record of the measurement.
4. Record the data. Record the reading or save the data according to the gauge’s instructions. If your gauge is capable of storing multiple measurements, make sure you log them properly to save time later.
5. Repeat as necessary. Repeat steps 1-4, taking multiple readings as needed across the inspection area to document all data.
Step 4: Post-Measurement
1. Clean the equipment. Once you have completed your measurements, clean the probe and the material with a soft cloth. Make sure that all couplant is removed from the probe.
2. Data review. Upload and review any saved data from the gauge. Make sure you document all measurements, and generate a report, if necessary.
3. Store the gauge. Store the ultrasonic thickness gauge in a dry and safe place, following any storage recommendations provided by the manufacturer.
Additional Tips for Accurate Measurements
- Maintain consistent pressure. Apply consistent pressure to the probe while taking measurements to avoid inconsistencies.
- Avoid rough surfaces. Try to avoid measuring areas that have rough, uneven, or heavily corroded surfaces, as this will impact readings.
- Use proper couplant. Always use the appropriate couplant for the material you are measuring. Some materials may require specific couplants for optimal readings.
- Regular calibration. Calibrate your gauge regularly and as needed throughout the inspection process. Regular calibration ensures the best possible accuracy.
- Refer to the manual. Always refer to the manufacturer’s manual for detailed instructions on how to use your specific gauge.
Maintenance and Care for Ultrasonic Thickness Gauges
Proper maintenance and care are crucial for ensuring the long-term reliability and accuracy of your ultrasonic thickness gauge.
Following these guidelines will help keep your equipment in optimal condition and prevent costly repairs.
Routine Cleaning
- Probe cleaning. After each use, clean the probe with a soft, dry cloth. Remove any couplant, dirt, or residue that may have accumulated during the inspection. Avoid using harsh chemicals or abrasive cleaners, as they can damage the probe.
- Cable inspection. Regularly inspect the probe cable for any signs of wear, fraying, or damage. Replace the cable if you notice any issues to ensure proper connection and signal transmission.
- Gauge body cleaning. Clean the gauge body with a soft, dry cloth. Avoid getting moisture into any ports, connections, or openings. For tougher stains, a slightly damp cloth may be used, but be sure to dry all parts completely after.
Storage
- Dry environment. Store the ultrasonic thickness gauge in a dry, cool place, away from extreme temperatures, direct sunlight, and humidity. Moisture can damage the electronic components and affect the accuracy of the readings.
- Protective case. If available, store the equipment in its original carrying case or a suitable protective container. This will help prevent any accidental damage during storage or transportation.
- Avoid stress on cables. Make sure that the probe cables are not bent sharply or stored in a way that causes stress. The cable should be coiled loosely or stored flat to avoid damage.
Battery Care
- Charging. Follow the manufacturer’s recommendations for charging the battery. Avoid overcharging, and ensure the batteries are fully charged before prolonged periods of storage.
- Storage. If the battery will not be used for a long time, store it separately and charge it periodically to prevent deep discharge.
- Replacement. Replace the batteries when they no longer hold a full charge and/or have been used for their recommended lifecycle.
Regular Inspections
- Probe check. Before each use, inspect the probe for any damage, wear, or corrosion. Replace any damaged parts to ensure proper performance.
- Cable check. Inspect the probe cable for any signs of wear, kinks, or breaks. Replace the cable if you notice any issues.
- Calibration check. Check the calibration of the gauge regularly, and calibrate the device as needed before use, as this is essential for accurate readings.
Professional Servicing
- Regular maintenance. Schedule periodic maintenance and servicing with a qualified technician. This will ensure proper calibration and help identify potential issues before they become major problems.
- Repairs. If you experience any malfunctions or issues with your ultrasonic thickness gauge, consult a professional technician or the manufacturer for repairs. Avoid attempting to fix the equipment yourself, as this may cause further damage and void the warranty.
Additional Tips
- Read the manual. Always refer to the manufacturer’s manual for specific maintenance recommendations and instructions. Each gauge has unique features and proper care will ensure optimal operation.
- Handle with care. Handle the ultrasonic thickness gauge carefully at all times. Avoid dropping or bumping the equipment during transportation and use.
- Avoid extreme environments. Avoid using the gauge in environments with extreme temperatures or humidity. If the gauge is not suited to a particular environment, it can be damaged by extreme conditions.
Ultrasonic Thickness Gauge FAQ
Here are answers to the most commonly asked questions about ultrasonic thickness gauges.
What is an ultrasonic thickness gauge?
An ultrasonic thickness gauge is a device that uses high-frequency sound waves to measure the thickness of materials. It is a non-destructive testing (NDT) tool, which means that it can provide accurate thickness readings without damaging the test object.
How does an ultrasonic thickness gauge work?
Ultrasonic thickness gauges work by sending sound waves through a material. The device measures the time it takes for the sound waves to travel through the material and reflect back. Using this information, the gauge calculates the thickness of the material.
What are the advantages of using an ultrasonic thickness gauge?
Ultrasonic thickness gauges offer several advantages, including non-destructive testing capabilities, high accuracy, the ability to measure a wide range of materials and thicknesses, and quick and efficient measurements. They are also portable and can be used in the field.
What types of materials can be measured with an ultrasonic thickness gauge?
Ultrasonic thickness gauges can measure a wide variety of materials, including metals, plastics, composites, ceramics, and glass. The specific type of material may affect which kind of probe you should use, or require a different method of calibration, so it’s important to follow the manufacturer’s recommendations.
What is a probe in ultrasonic testing?
A probe, also known as a transducer, is a key component of an ultrasonic thickness gauge. It is used to generate and receive ultrasonic sound waves. Different types of probes are available, each designed for specific materials and measuring conditions. A probe’s frequency, shape, and size will affect the quality of the measurement.
How do you calibrate an ultrasonic thickness gauge?
Ultrasonic thickness gauges are calibrated using calibration blocks with known thicknesses. You’ll need to access the gauge’s calibration settings and follow the device’s recommended steps to adjust the gauge to read the calibration blocks accurately. Regular calibration is essential for accurate measurements.
What is a couplant, and why is it needed?
A couplant is a gel, liquid, or paste material used to ensure proper transmission of sound waves between the probe and the material being measured. Couplant eliminates air gaps between the probe and material surface, improving accuracy, and should always be used when operating an ultrasonic thickness gauge.
What is A-scan and B-scan in ultrasonic thickness gauges?
A-scan is a graphical representation of the ultrasonic signal, which provides additional information about the material’s structure. B-scan offers a cross-sectional view of the material, created by moving the probe along a line. Both A-scan and B-scan provide the user with additional data during the inspection process.
How often should an ultrasonic thickness gauge be calibrated?
The frequency of calibration depends on the usage and requirements. However, in most industrial settings, it is best practice to calibrate the gauge at the beginning of each shift, before each use, and any time the gauge has been dropped or damaged. Frequent calibration ensures accurate readings and reliability.
How do I maintain an ultrasonic thickness gauge?
Proper maintenance includes cleaning the probe after each use, storing the gauge in a dry place, replacing batteries as needed, and regularly inspecting the gauge for any damage. It’s also important to schedule periodic maintenance and servicing with a qualified technician to ensure proper calibration and long-term reliability.